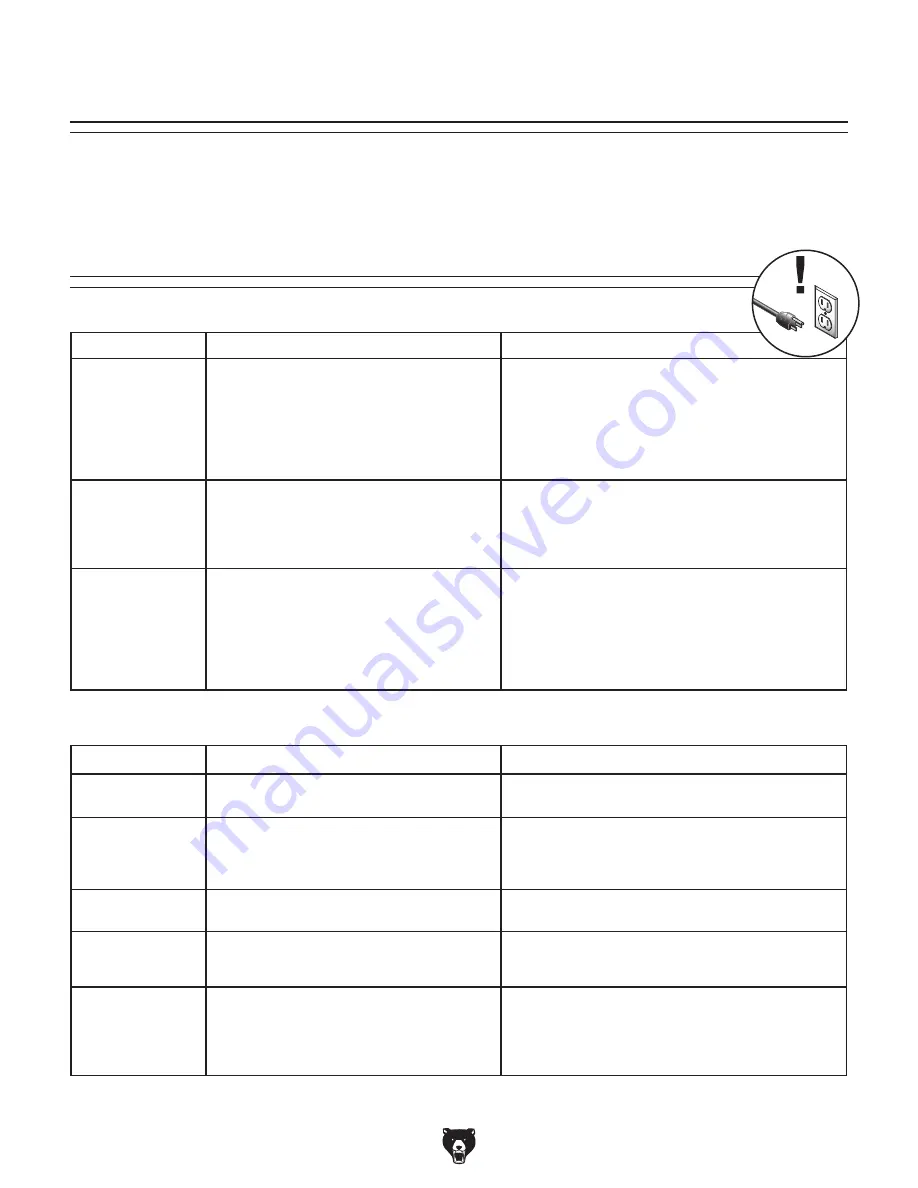
-24-
Model T28523 (Mfd. Since 05/19)
Review the troubleshooting procedures in this section if a problem develops with your machine. If you need
replacement parts or additional help with a procedure, call our Technical Support.
Note: Please gather the
serial number and manufacture date of your machine before calling.
SECTION 7: SERVICE
Troubleshooting
Symptom
Possible Cause
Possible Solution
Machine does not
start, or power-
supply fuse/breaker
trips immediately
after startup.
1. Switch disabling key removed.
2. Incorrect power supply voltage or circuit
size.
3. Power supply circuit breaker tripped or fuse
blown.
4. ON/OFF switch at fault.
5. Motor at fault.
1. Install switch disabling key.
2. Ensure correct power supply voltage and circuit
size.
3. Ensure circuit is sized correctly and free of shorts.
Reset circuit breaker or replace fuse.
4. Replace switch.
5. Test/repair/replace.
Machine stalls or is
underpowered.
1. Machine undersized for task.
2. Motor overheated.
3. Run capacitor at fault.
4. Motor bearings at fault.
5. Motor at fault.
1. Use new grinding wheel; reduce feed rate.
2. Let cool, and reduce workload.
3. Test/repair/replace.
4. Test/repair/replace.
5. Test/repair/replace.
Machine has
vibration or noisy
operation.
1. Motor or component loose.
2. Machine incorrectly mounted to workbench
or stand.
3. Grinding wheel at fault/arbor hole not round.
4. Motor bearings at fault.
5. Motor shaft bent.
1. Inspect/replace damaged parts; tighten if loose.
2. Tighten mounting hardware.
3. Dress/replace grinding wheel.
4. Test by rotating shaft; rotational grinding/loose shaft
requires bearing replacement.
5. Test with dial indicator and replace motor.
Motor & Electrical
Symptom
Possible Cause
Possible Solution
Machine slows
when operating.
1. Operator applying too much pressure.
1. Use less pressure when grinding.
Wavy condition
on surface of
workpiece.
1. Machine vibrating.
2. Workpiece not held firmly.
3. Wheel face uneven.
4. Wheel is too hard.
1. Securely mount on solid surface (
Page 13).
2. Use a holding device to firmly hold workpiece.
3. Dress grinding wheel (
Page 20).
4. Use softer wheel, or reduce feed rate.
Lines on surface of
workpiece.
1. Wheel surface loaded with residue.
2. Workpiece not held tightly.
1. Dress grinding wheel (
Page 20).
2. Use holding device to firmly hold workpiece.
Burning spots
or cracks in the
workpiece.
1. Improper type of grinding wheel.
2. Improper feed rate.
3. Workpiece requires quenching.
1. Try softer wheel or a wheel with coarser grit.
2. Slow down rate of workpiece movement into wheel.
3. Quench workpiece in water to cool.
Wheel dulls quickly,
grit falls off.
1. Depth of cut too great.
2. Wheel is too soft for material being ground.
3. Wheel diameter too small.
4. Bad wheel dress.
5. Defective wheel bonding.
1. Slow down rate of workpiece movement into wheel.
2. Select harder bond.
3. Replace grinding wheel (
Page 20).
4. Dress grinding wheel (
Page 20).
5. Consult manufacturer of grinding wheel.
Operations
Содержание T28523
Страница 32: ......