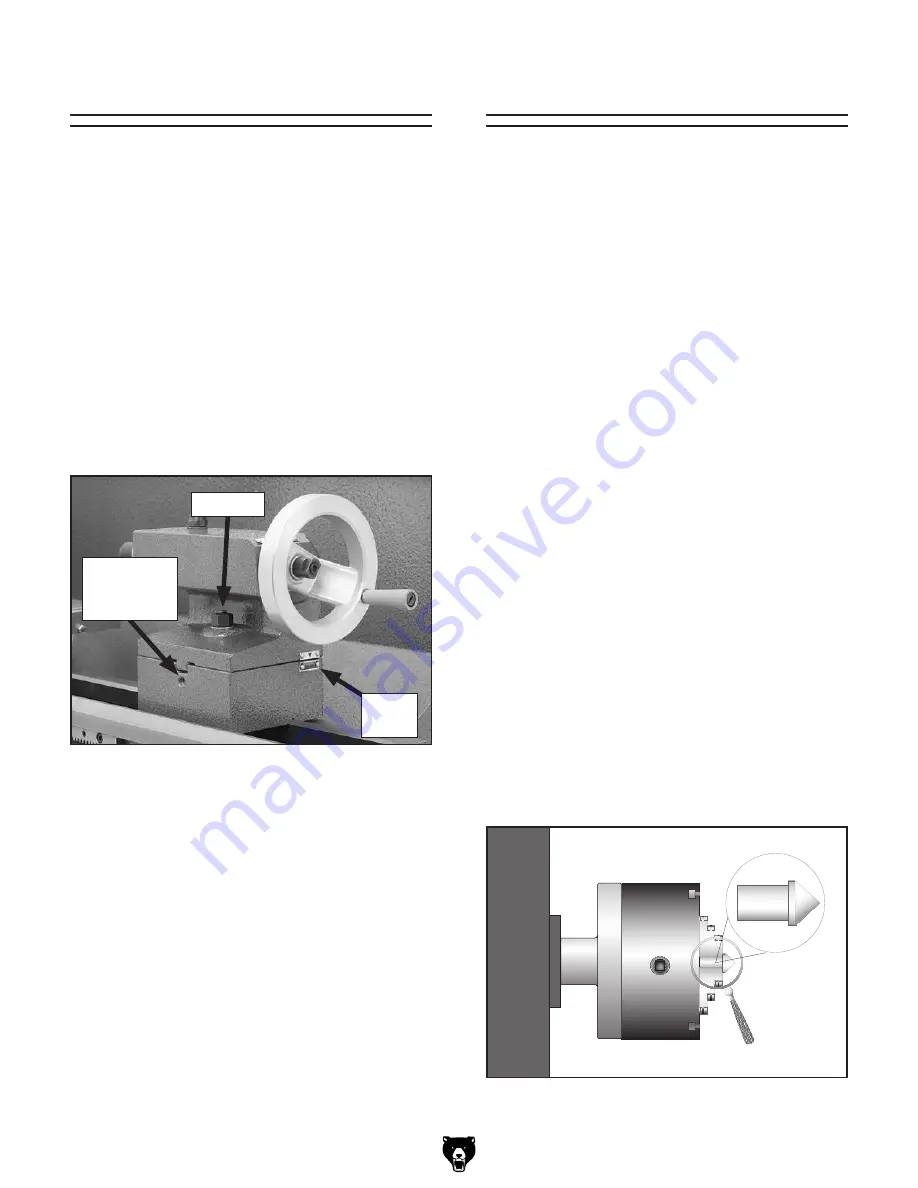
Model G4000 (Mfg. Since 8/09)
-27-
Offsetting Tailstock
the tailstock can be offset slightly from the spin-
dle center line to cut shallow tapers in a workpiece
mounted between centers. When the tailstock is
offset toward the operator, the machined workpiece
will be smaller at the tailstock end. Conversely, if
the tailstock is offset away from the operator, the
taper will be smaller at the spindle end.
Tools Needed
Qty
hex Wrench 4mm .............................................. 1
Wrench 14mm ................................................... 1
To set the tailstock offset:
1. Loosen the tailstock lock nut (see figure 28).
2. Alternately loosen and tighten the two adjust-
ment set screws (one on either side of the
tailstock) until the desired offset is indicated
on the offset scale, then retighten the lock
nut.
3. to return the tailstock back to the original
position, repeat
Step 2 until the centered
position is reached.
Note: For purposes of accuracy, you may
want to perform the
Aligning Tailstock pro-
cedure on
this page after offset adjustments
have been made.
Aligning Tailstock
the tailstock was aligned with the spindle at the
factory. however, we recommend that you take
the time to ensure that the tailstock is aligned
to your own desired tolerances, especially if you
have made tailstock offset adjustments.
To align the tailstock with the spindle:
1. use a precision level to make sure the lathe
bedway is exactly level from side-to-side
and front-to-back. if necessary, use shims
between the lathe and chip pan.
2. Center drill a 6" long piece of round bar stock
on both ends. set it aside for use in
Step 5.
Note: If the tailstock is out of alignment by
only a few thousands of an inch, the center
drill will find the center point during the drilling
process. If the tailstock appears grossly out
of alignment, adjust the tailstock offset until it
appears to be centered.
3. Make a dead center by turning a shoulder on
a similar piece of round stock, then flip the
piece over in the chuck and turn a 60° point
(see
figure 29).
Note: As long as the fabricated dead center
remains in the chuck, the point of this center
will remain true to the spindle center line.
However, if it is removed, the point will have
to be re-finished before using it for this proce-
dure again.
figure 29. the fabricated dead center.
figure 28. tailstock offsetting controls.
Lock nut
offset
scale
Adjustment
set screw
(1 of 2)