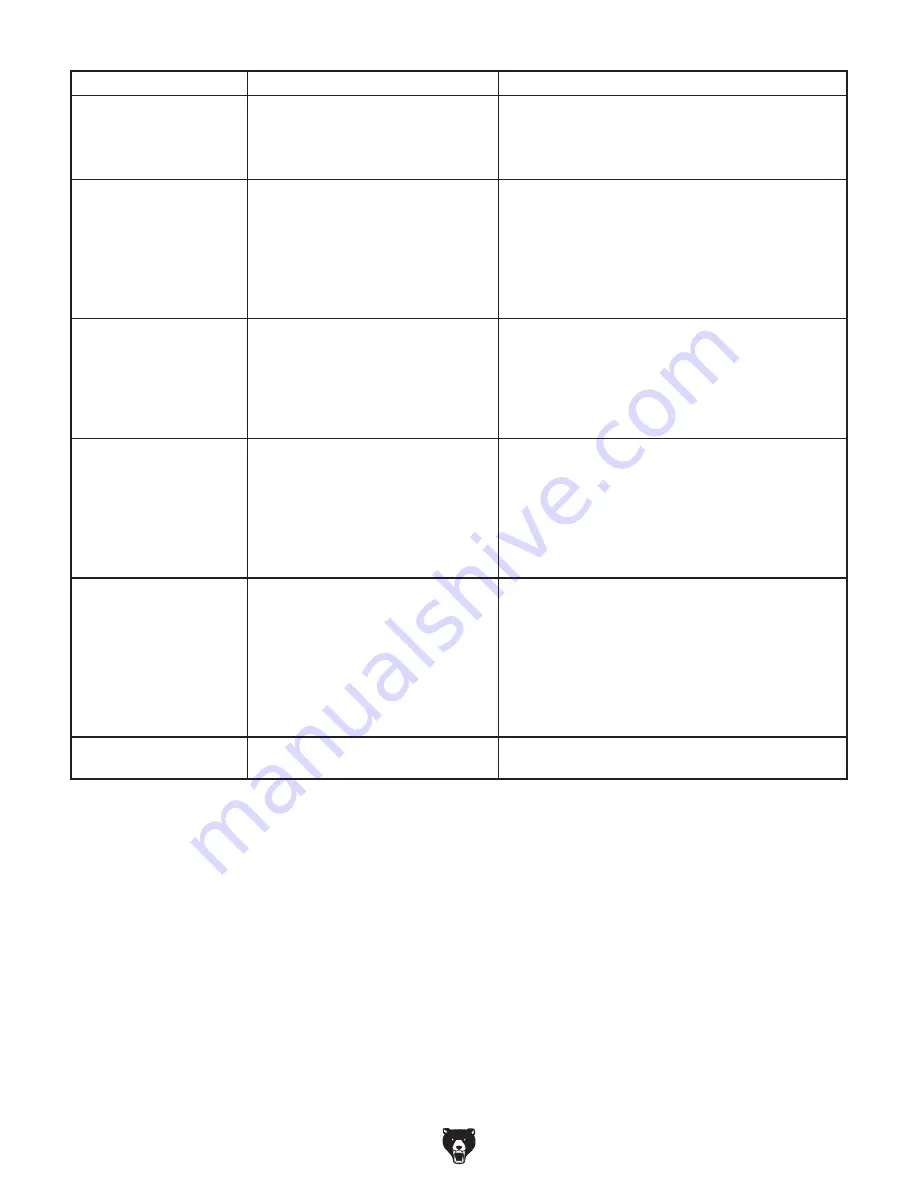
-36-
Model G0755 (Mfg. Since 1/13)
symptom
possible Cause
possible solution
tool loose in spindle.
1. tool is not fully drawn up into
spindle taper.
2. debris on tool or in spindle taper.
3. taking too big of a cut.
1. tighten draw bar.
2. Clean collet and spindle taper.
3. Lessen depth of cut and allow chips to clear.
Breaking tools or cutters.
1. spindle speed/feed rate is too fast.
2. Cutting tool too small.
3. Cutting tool getting too hot.
4. taking too big of a cut.
5. spindle extended too far down.
1. set spindle speed correctly (
Page 25) or use slower
feed rate.
2. use larger cutting tool and slower feed rate.
3. use coolant fluid or oil for appropriate application.
4. decrease depth of cut.
5. Fully retract spindle and lower headstock. this
increases rigidity.
Workpiece vibrates or
chatters during operation.
1. table locks not tight.
2. Workpiece not secure.
3. spindle speed/feed rate is too fast.
4. spindle extended too far down.
1. tighten down table locks.
2. properly clamp workpiece on table or in vise.
3. set spindle speed correctly (
Page 25) or use a
slower feed rate.
4. Fully retract spindle and lower headstock. this
increases rigidity.
table is hard to move.
1. table locks are tightened down.
2. Chips have loaded up on ways.
3. Ways are dry and need lubrication.
4. table limit stops are interfering.
5. gibs are too tight.
1. Make sure table locks are fully released.
2. Frequently clean away chips that load up during
operations.
3. Lubricate ways (
Page 32).
4. Check to make sure that all table limit stops are not
in the way.
5. Adjust gibs (see
Page 37).
Bad surface finish.
1. spindle speed/feed rate is too fast.
2. using a dull or incorrect cutting tool.
3. Wrong rotation of cutting tool.
4. Workpiece not secure.
5. spindle extended too far down.
1. set spindle speed correctly (
Page 25) or use a
slower feed rate.
2. sharpen cutting tool or select one that better suits
the operation.
3. Check for proper cutting rotation for cutting tool.
4. properly clamp workpiece on table or in vise.
5. Fully retract spindle and lower headstock. this
increases rigidity.
Cutting results not square.
1. table and spindle are not at 90° to
each other.
1. tram the spindle (
Page 38).
Содержание G0755
Страница 60: ......