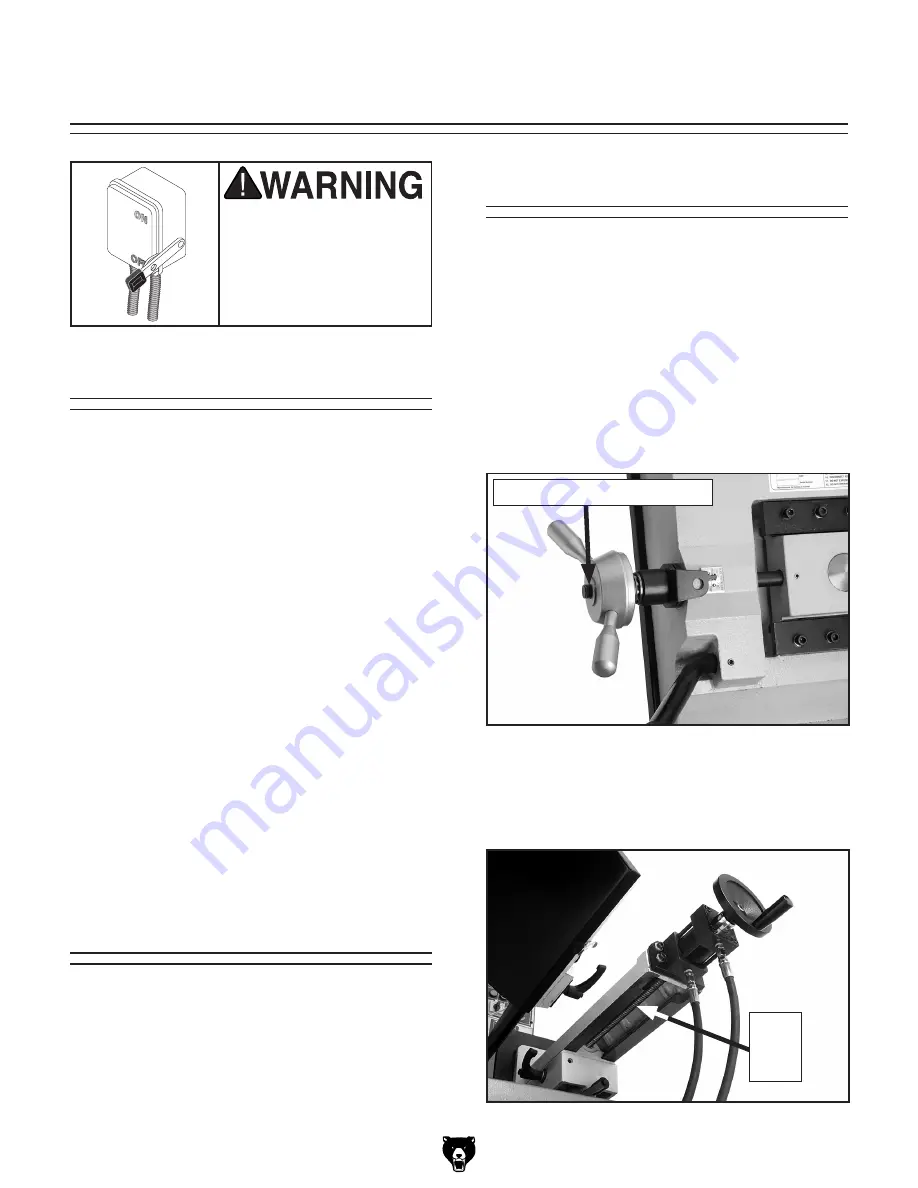
g0664 heavy duty Metal-Cutting Bandsaw
-41-
SECTION 6: MAINTENANCE
Always disconnect power
to the machine before
performing maintenance.
failure to do this may
result in serious person-
al injury.
Lubrication
For optimum performance from your machine,
follow this maintenance schedule and refer to any
specific instructions given in this section.
After first 50 hours:
•
Change hydraulic fluid.
Daily Check:
•
loose mounting bolts.
•
damaged or worn saw blade.
•
Worn or damaged wires.
•
proper blade tension.
•
hydraulic/cutting fluid level.
•
Clean and wipe down machine.
Monthly Check:
•
lubricate vise and blade tensioner leadscrew.
Six-Month Check:
•
Change hydraulic fluid.
Annual Check:
•
replace cutting fluid and clean out tank. if
the saw is used heavily, clean the tank and
replace the cutting fluid at shorter intervals.
Schedule
Cleaning the Model g0664 is relatively easy. after
using your bandsaw, clean excess chips by vacu-
uming or sweeping them up.
if using water based cutting fluid, wipe down and
lubricate areas where the liquid may collect and
cause corrosion.
Cleaning
all bearings and the gearbox on the Model g0664
are lubricated and sealed for life. no further atten-
tion is needed unless damage occurs.
To lubricate the bandsaw:
1. lubricate the blade tensioner leadscrew
(
figure 46) with multi-purpose grease, and
apply a coat of high-quality metal protectant
such as slipit® on
page 40 to all unpro-
tected cast iron surfaces.
2. lubricate the leadscrew as needed with multi-
purpose grease by applying a thin layer along
the leadscrew surface (see
figure 47).
figure 46. lubrication point.
Blade tensioner lead screw
figure 47. Vise leadscrew lubrication area.
Vise
lead
screw