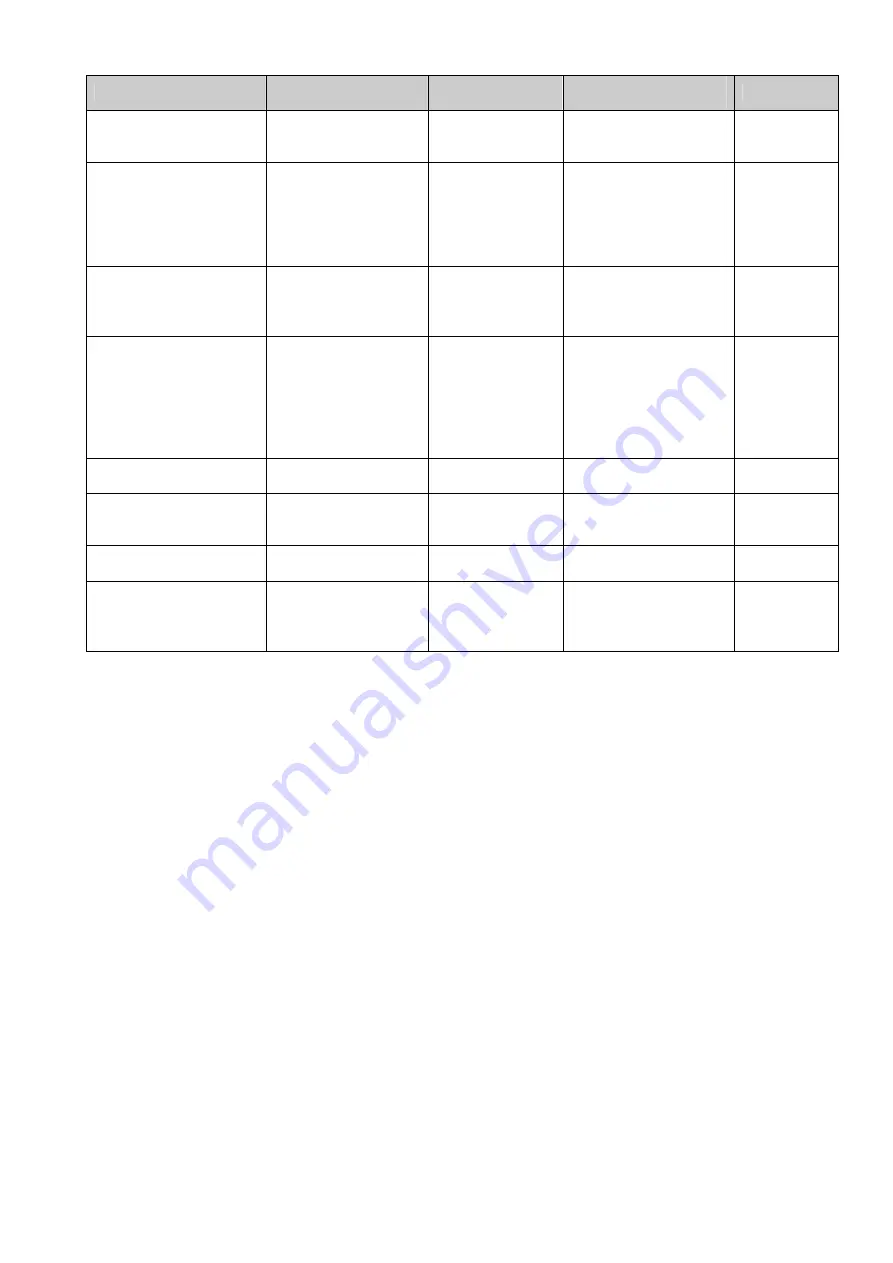
19
Lubricated parts
Lubricant
Lubrication
frequency
Standard lubricating
volume
Notes
Shaft bearings
Belt tensioning
bearings
High temperature
lubricant (heat test
higher than 120 ºC)
Once every six
month
Injection as defined
Milling cutter spindle
moving elements:
chains, threaded
screws, bevel gears, etc,
milling cutter spindle
sliding sleeve
Grease type CA ZG-3
Once a month
Grease covered
Swallow-tailed movable
table for vertical shafts
(lubricate at centralized
oil injection point)
Grease type CA ZG-0 Once a month
Considerable grease
spillage
Feeding unit;
roller gearbox
Gear oil 90
Change oil after
500 hours the first
time; after 2000
hours the second
time.
Subsequently
every two years
800
~
1250 cm
3
Feeding unit;
roller shaft bearings
Grease type CA ZG-3
Once every 6
months
As defined
Feeding unit; cardan
joint
Grease type CA ZG-3
Once every
change
Considerable grease
spillage
Grease covered
Feeding unit; lifting
reduction gears
Grease type CA ZG-3
Once every 6
months
As defined
Table
Motor oil N46
As needed and
based on type of
wood being
machined
Press 4
~
5 times
Manual oil
pump
22. BELT TENSIONING AND REPLACEMENT
During the first usage period of the machine, belts will break in and this will unavoidably reduce tension.
After a few days' usage, re-adjust belt tension, without overtensioning, to avoid overloading and damaging motor
and shaft bearings.
Inspect belts at least once every 2 months to check for wear and restore an optimal tensioning.
Tension is to be checked by applying pressure on belts halfway through their length: a belt sagging of approx. 10
mm should be noticed.
To tension or replace belts, lockout the main switch after setting it to "0", then remove the machine rear guard.
Belt tensioning - upper and lower horizontal shafts
a)
Slacken the nut in the tie-rod fixed to the motor flange.
b)
Axially adjust the motor by acting on the tie-rod until belts are tensioned as indicated above
c)
Re-tighten the tie-rod nut.
Belt tensioning - left- and right-hand vertical shafts
a)
Slacken the 4 motor flange fastening screws.
b)
Tension the belt by prying on the motor flange using the wrench supplied (1) (Fig. 18)
c)
Tighten the motor flange screws
When replacing the belt, make sure the arrow printed on the external side indicates the shaft direction of rotation.
23. MACHINE STARTING AND STOPPING
- Make sure the emergency mushroom buttons are not pressed; if they are, give the mushroom button ¼ turn to the
left;
- Make sure that air system pressure is correct
- Make sure the upper guard is properly closed;
- Make sure the suction plant is on;
- Set the main switch to "1";