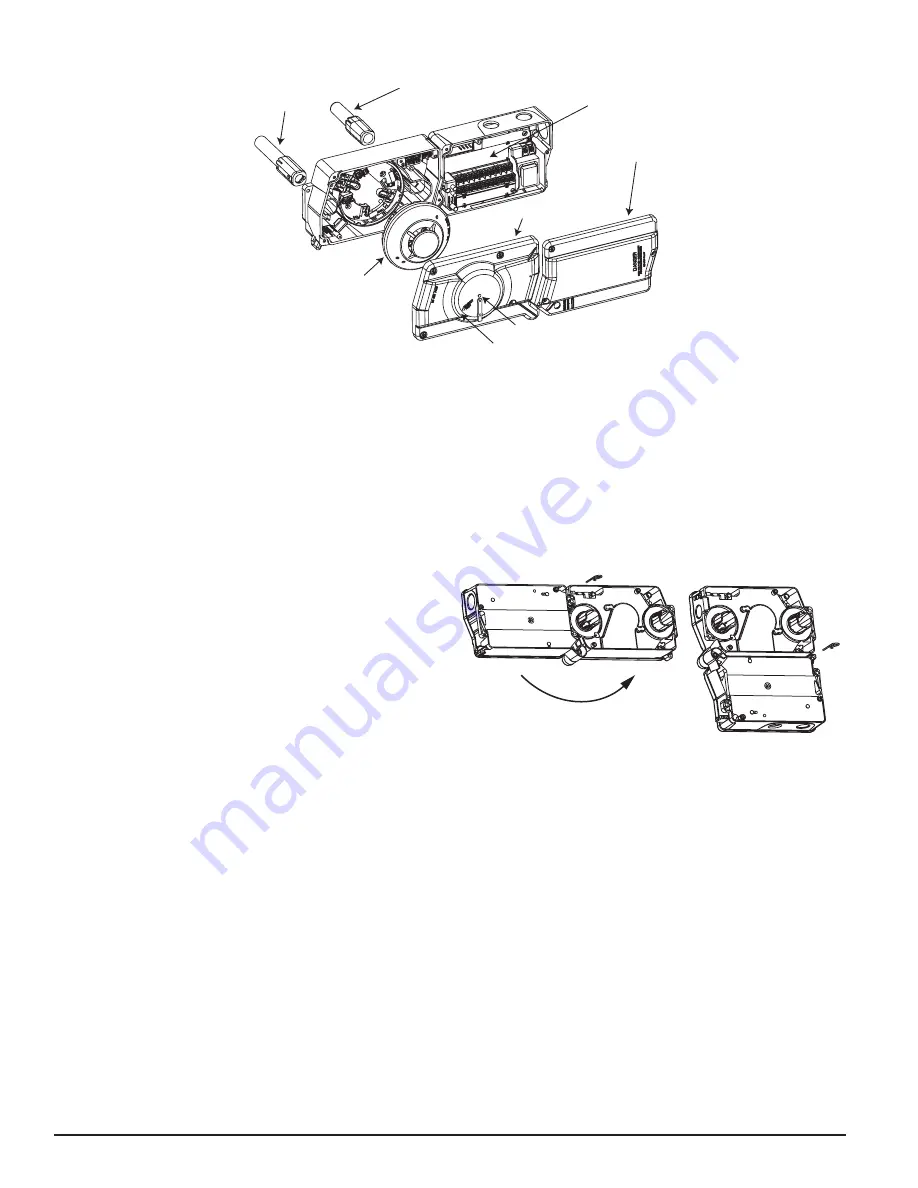
POWER BOARD
EXHAUST TUBE
METAL SAMPLING TUBE
(sold separately)
POWER BOARD
MODULE COVER
SENSOR HEAD
SENSOR MODULE
COVER
MAGNET TEST
SMOKE TEST PORT
[3] GENERAL DESCRIPTION
Smoke introduced into an air duct system will be distributed throughout the
entire building. Smoke detectors designed for use in air duct systems are used to
sense the presence of smoke in the duct.
Model DSD240 Duct Smoke Detector utilizes 4-wire photoelectric technology
for the detection of smoke. This detection method, when combined with an
efficient housing, samples air passing through the duct allowing detection of
a developing hazardous condition. When sufficient smoke is sensed, an alarm
signal is initiated and appropriate action can be taken to shut off fans, blowers,
change over air handling systems, etc. These actions can facilitate the manage-
ment of toxic smoke and fire gases throughout the areas served by the duct
system.
The DSD240 detector is designed to operate on 24 VDC/VAC or 240 VAC. Alarm
and supervisory relay contacts are available for control panel interface (alarm
initiation), HVAC control, and other auxiliary functions. The fire alarm control
panel is NOT notified when sensor maintenance its required. Auxiliary relays
are provided for fan shut down. Detector interconnection provides signaling of
up to 30 other detectors in the loop for multiple fan shut down. These detectors
are not designed for 2-wire applications.
[3.1] DETECTOR FEATURE SET
-Utilizes 2D51 plug-in head
-Cover missing signal
-Sampling tubes install from front or rear of detector
-Compatible with existing accessories
[4] CONTENTS OF THE DUCT SMOKE DETECTOR KIT
1. Sensor/power board assembly and cover(s)
2. Three #10 sheet metal screws for mounting
3. Drilling template
4. One sampling tube end cap
5. One plastic exhaust tube
NOTE: A sampling tube must be ordered to complete the installation. It must be
the correct length for the width of the duct where it will be installed. See Table 1
on page 3 to determine the inlet tube required for different duct widths.
[5] DETECTOR INSTALLATION
[5.1] VERIFY AIR FLOW DIRECTION AND VELOCITY
Model DSD240 detectors are designed to be used in air handling systems with
air velocities of 100 to 4000 feet per minute. Duct widths from 6 inches to 12 feet
can be accommodated. Be sure to check engineering specifications to ensure
that the air velocity in the duct falls within these parameters. If necessary, use a
velocity meter (anemometer) to check the air velocity in the duct.
[5.2] DETERMINE MOUNTING LOCATION AND CONFIGURATION
On ducts wider than 18 inches it is recommended that the detector be mounted
downstream of a bend, obstruction in the duct, or the supply or return air inlet.
Exception:
Installation of duct detectors can be on or within a commercial
packaged rooftop heating and air-conditioning system, fire/smoke dampers and
economizers. They may be mounted in either the supply and/or return air sec-
tion as determined by local code.
Once a suitable location is selected, determine if the detector is to be mounted
in a side-by-side “rectangular” configuration or a top-over-bottom “square”
configuration as shown in
Figure 2. I
f mounting in the square configuration,
remove the rear attachment pin, rotate the unit at the hinge, and replace the
pin into the new attachment hole as shown in
Figure 2
. Do NOT remove the
hinge screw during this process. Final installation approval shall be based upon
passing section 7.2.
FIGURE 2:
REMOVE PIN AND PIVOT
DETECTOR AS SHOWN BELOW.
REPLACE PIN TO
SECURE DETECTOR
IN PLACE.
H0638-00
[5.3] DRILL THE MOUNTING HOLES
Remove the paper backing from the mounting template supplied. Affix the tem-
plate to the duct at the desired mounting location. Make sure the template lies
flat and smooth on the duct.
[5.3.1] FOR RECTANGULAR SIDE-BY-SIDE MOUNTING CONFIGURATION:
Center punch at (4) target centers: (2) “A” for sampling tubes and (2) “B” for the
rectangular configuration mounting tabs as shown on mounting template. Drill
pilot holes at target “A” centers and cut two 1.375 inch diameter holes using a
1
3
/
8
inch hole saw or punch. Drill .156 inch diameter holes using a
5
/
32
inch drill
at target “B” centers.
[5.3.2] FOR SQUARE TOP-OVER-BOTTOM MOUNTING CONFIGURATION:
Center punch at (4) target centers: (2) “A” for sampling tubes and (2) “C” for
the square configuration mounting tabs as shown on mounting template. Drill
pilot holes at target “A” centers and cut two 1.375 inch diameter holes using a
1
3
/
8
inch hole saw or punch. Drill .156 inch diameter holes using a
5
/
32
inch drill
at target “C” centers. If desired, drill an additional .156 inch hole at the location
of one of the mounting tabs on the lower housing.
[5.4] SECURE THE DUCT DETECTOR TO THE DUCT
Use two (rectangular configuration) or three (square configuration) of the pro-
vided sheet metal screws to screw the duct detector to the duct.
CAUTION:
Do not overtighten the screws.
[2] FIGURE 1. EXPLODED VIEW OF DUCT SMOKE DETECTOR COMPONENTS:
H0637-00
IN-GE-DSD240-01-01 2
I56-9200-001
5/6/2019