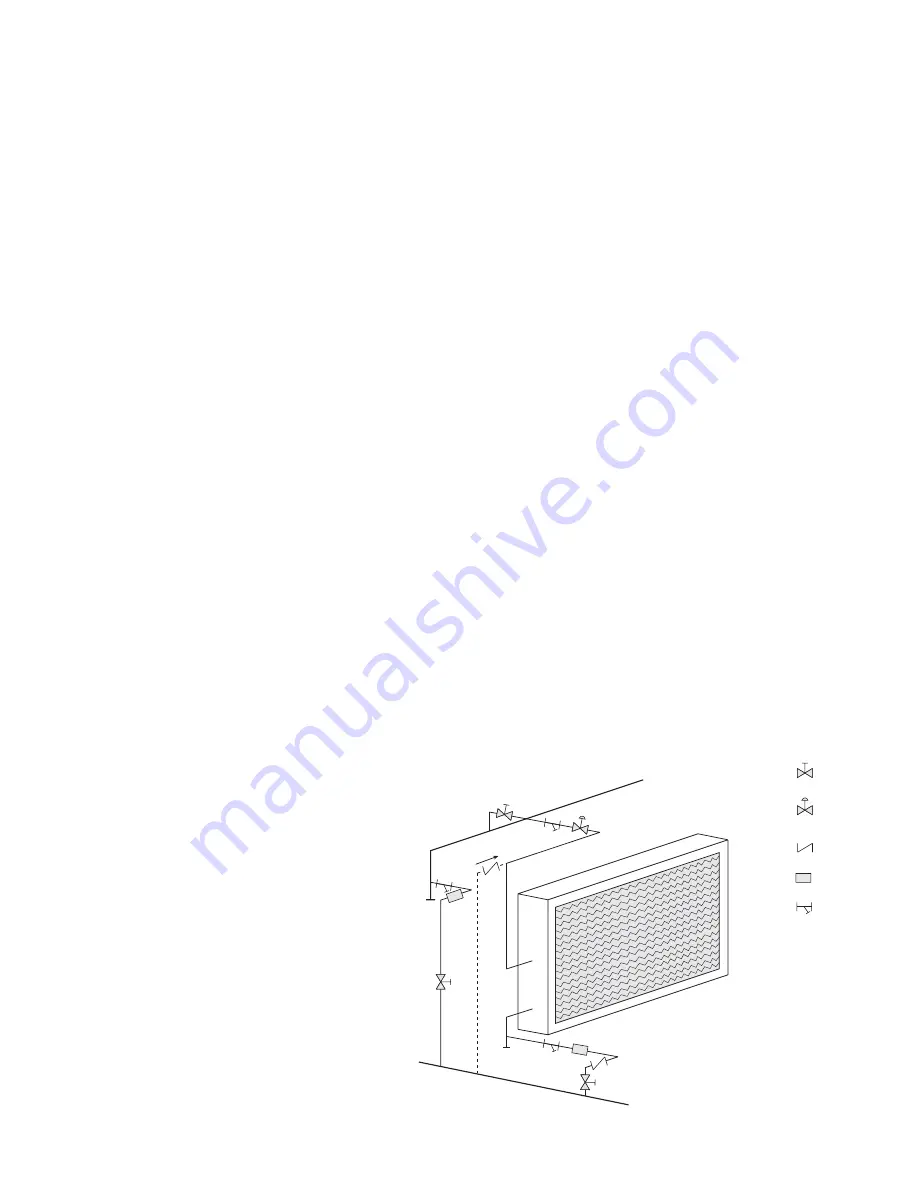
Steam Coils
Application Recommendations:
Satisfactory operation and service life are best ensured when coils are installed with proper piping, trap, and
support arrangement. The following notes and Figure 5 are recommended for the coil unit installation and
operation.
General:
1.
Provide separate supports and hangers for the unit and the piping.
2.
Be certain that adequate piping flexibility is provided. Stresses resulting from expansion of closely
coupled piping and coil arrangement can cause serious damage.
3.
Standard steam coils are pitched in the casings when installed for horizontal air flow. The casing must
BE LEVEL after the unit is installed for proper condensate drainage. If condensate is not removed the coil
will suffer from water hammering and will have a shortened life. On vertical air flow applications, the coils
must be pitched when installed.
4. Do not reduce pipe size at the coil return connection. Carry return connection size through the dirt
pocket, making the reduction at the branch leading to the trap.
5.
It is recommended that vacuum breakers be installed on all applications to prevent retaining condensate
in the coil. Generally, the vacuum breaker is to be connected between the coil inlet and the return main.
The vacuum breaker should be open to the atmosphere and the trap design should allow venting of large
quantities of air.
6. Do not attempt to lift condensate when using modulating or on-off control.
7.
Do not reduce the pipe size leaving the coil.
Traps:
1.
Size traps in accordance with the manufacturer’s recommendations. Be certain that the required pressure
differential will always be available. DO NOT UNDERSIZE.
2.
Float and thermostatic or bucket traps are recommended for low pressure steam. On high pressure
systems, bucket traps are normally recommended. The thermostatic traps should be used only for air
venting.
3. Bucket traps are recommended for use with on-off control only.
4.
Locate traps at least 12 inches below the coil return connection.
Controls:
1.
On high pressure installations, a two-position steam valve with a face and bypass arrangement is
preferred where modulating control is required.
2.
Modulating valves must be size properly. DO NOT UNDERSIZE.
Freezing Conditions
(Entering air below 35ºF)
:
1. 5 PSI steam must be supplied to the coil at all times.
2.
Modulating valves are not recommended. Control should be by means of face and bypass dampers.
3.
Provision should always be made to thoroughly mix fresh air and
return air before it enters the coil on return air units.
Also, temperature control elements must be
properly located to obtain true air mixture
temperatures.
4.
As additional protection against freeze-
up, the trap should be
installed
sufficiently far below the coil to provide
an adequate hydrostatic head to ensure
removal of condensate during an
interruption in the steam pressure.
Estimate 3 feet for each 1 PSI of trap
differential required.
5.
On start up, admit steam to coil ten
minutes before admitting outdoor air.
6.
Provision must be made to close fresh air
dampers if steam supply pressure falls
below minimum specified.
Steam Main
Retur
n Main
Gate Valve
Control Valve, Modulating
Two-Position
Check Valve-Vacuum Breaker
Float and Thermostat Trap
Strainer
Figure 5
Recommended Steam Coil Piping
9