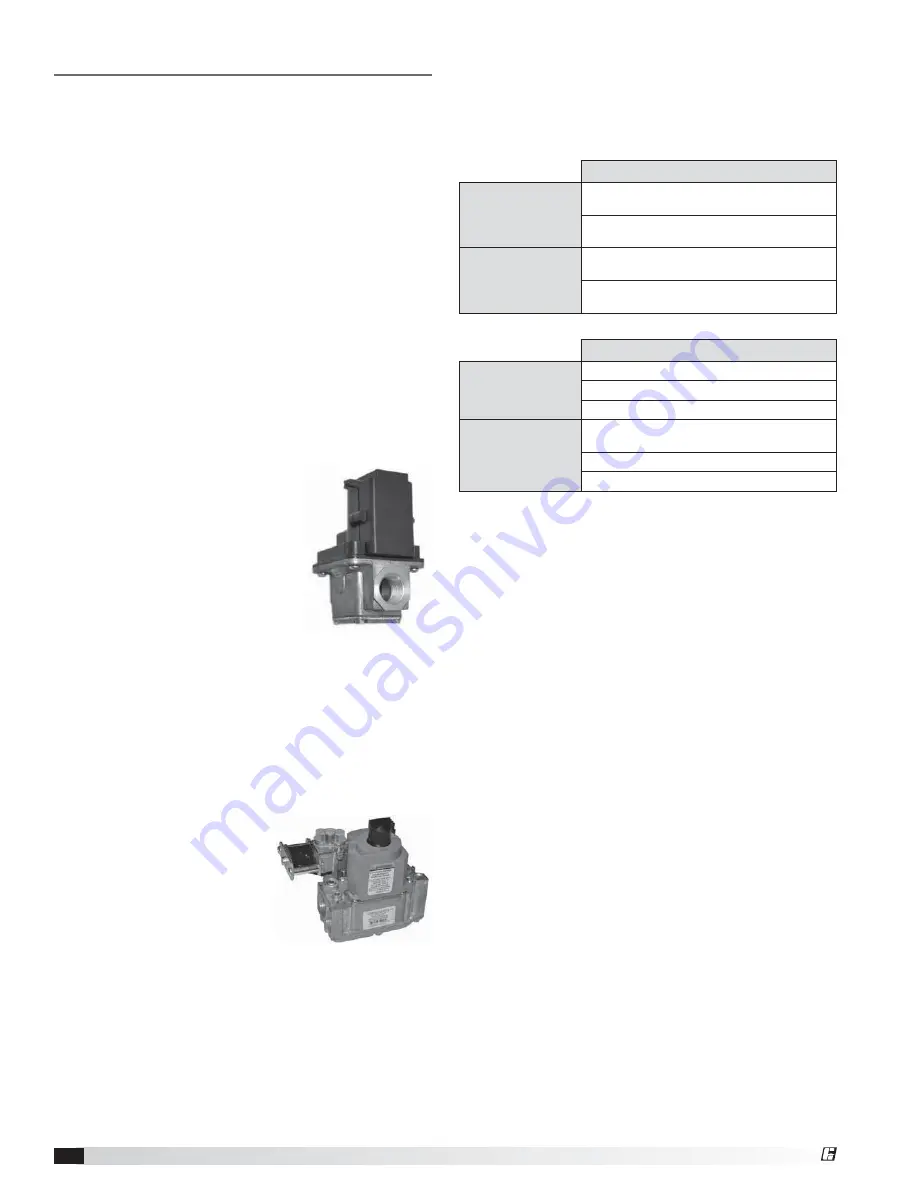
Indirect Gas-Fired Heat Modules
6
Gas-Fired Burner Turndown
Furnaces are available in single stage, multi-stage or
electronically modulated configurations. In single stage,
the entire furnace is either on or off. In multi-stage
furnaces, combustion occurs in stages and is expressed
as the number of different stages (example: 8 stage).
Electronically modulated furnaces have continuously
variable firing rates. In both staged and electronically
modulated furnaces, the result is burner turndown.
Turndown is the capability of the furnace to operate
at less than full capacity, accomplished by reducing
the amount of gas flow when the unit is operating. The
advantage in being able to turn down firing rate is that
when the demand for heat is low, the furnace will not
cycle as often. Turndown is expressed as a ratio and
is found by dividing the maximum BTU input by the
minimum BTU input.
Electronic Modulation
Turndown is specified by the customer. Most common
is the use of an electronically-controlled gas valve which
provides a 4:1 turndown. The entire furnace is sized
appropriately for the maximum heat
output ordered by the customer,
but it can operate as low as 25%
of its maximum capacity. The
electronically-controlled gas valve
will modulate the combustion rate
continuously, dependent on the
output from an FX controller. With
this method, all the burners fire
at the same time but at a varying
capacity. The Modulating Valve is used in conjunction
with an FX electronic controller and a combination valve
which provides an ON/OFF function.
Two Stage Valve
The two-stage valve is switched electrically from closed
to full output to half output, producing a 2:1 turndown.
In some cases, multiple furnaces may be used in a
ventilating unit. When this is done with two single-stage
furnaces, it is possible to run just one furnace at a time,
resulting in a 2:1 turndown.
If each furnace is already
configured for a 2:1 turndown,
the overall result can then be a
4:1 turndown.
Combinations
Various combinations of the methods outlined may be
used to accomplish the turndown requested by the
customer.
Available turndown control options include:
Electronic Modulation
Single Furnace
Unit
4:1 uses modulating valve and FX
programmable controller
2:1 uses modulating valve and
1092 control system
Two Furnace
Unit
8:1 uses one 4:1 modulating furnace with
FX controller and one 2 stage furnace
4:1 uses two 4:1 modulating furnaces
running in parallel
Staged
Single Furnace
Unit
8 stage
2 stage
1 stage
Two Furnace
Unit
16 stage uses one 8 stage furnace and
one single-stage furnace
4 stage uses two 2 stage furnaces
2 stage uses two single-stage furnaces
®