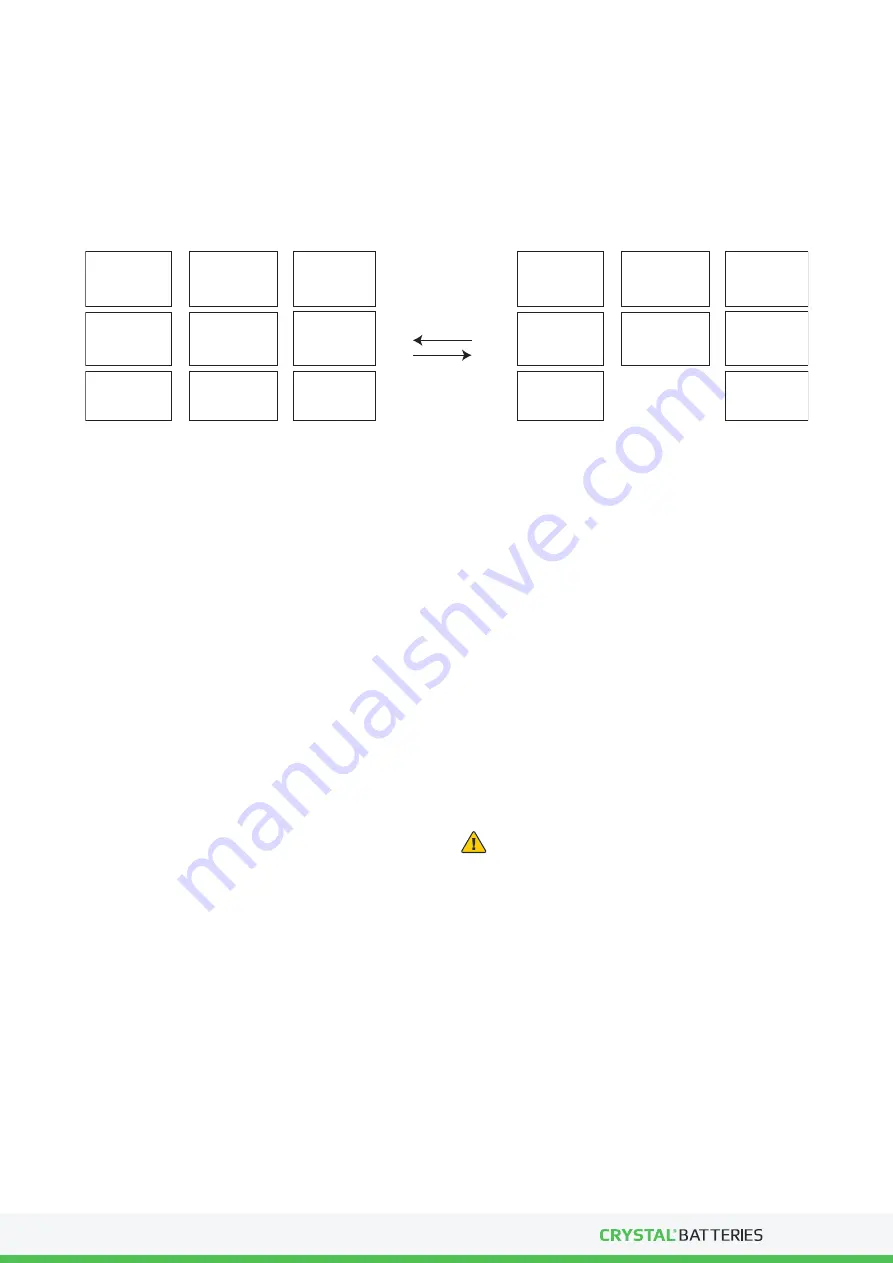
|
13
CRYSTAL® BATTERY USER MANUAL
2.1.8 Special Manufacturing Process
Using negative pressure filling technology in combination with patented gravity filling containers to fill the
batteries with electrolyte and the patented terminal connecting equipment, ensures an even distribution of
electrolyte in each cell which further enhances the performance of the battery and increases efficiency.
2.2 GENERIC
WORKING PRINCIPLE
pbO
2
+
2H
2
SO
4
+ Pb + PbSO
4
DISCHARGE
CHARGE
+
+
+
+
PbSO4 + H2O
LEAD
DIOXIDE
POSITIVE
PLATE
ACTIVE
MATERIAL
DILUTE
SULPHORIC
ACID
LEAD
COMPOSITE
NEGATIVE
PLATE
ELECTROLYTE
NEGATIVE
PLATE
LEAD
SULPHATE
POSITIVE
DISCHARGE
MATERIAL
DISCHARGE
MATERIAL
WATER
LEAD
SULPHATE
WATER
NEGATIVE
Figure 1. The main electrochemical reaction during charge / discharge.
into active material when discharging, prolonging the
battery’s useful life and making it resistant to
sulphation.
Crystal® batteries use a new and patented advanced
type of super absorbent matt (SAM) as a separator.
The SAM has much higher electrical conductivity, heat
resistance, and acid resistance abilities than standard
commercial AGM separators.
The crystallized electrolyte in combination with the
SAM effectively protects the plates and prevents the
active material from falling off during regular use.
The electrolyte is completely absorbed and stored in
the SAM. Since the SAM is completely saturated with
electrolyte when crystalized, no free liquid electrolyte
will be present in the battery. The battery can now be
used in various directional positions without leaking.
CAUTIONARY NOTE: Long-term storage with the
plates horizontal to the ground may cause problems
in the longer term as vibration or gravity may
eventually reduce usage life.
The positive and negative active material reacts with
the acidic element of the electrolyte and becomes
lead sulphate and water when discharging, causing
the acid density to decrease. When charging, the acid
that concentrated in the positive oxide paste during
discharge cycles is released back into the electrolyte.
At this time, the lead sulphate in the positive and
negative plate transforms into lead dioxide and a
spongy type of lead which causes the acid density in
the electrolyte to increase. The patented
formulation acts to reduce the acidity of the solution
and in turn, increases the hydrogen concentration
that is required for ion exchange. None of the
confidential chemical ingredients are indicated in
Figure 1 due to the sensitive nature and to
safeguard our intellectual property.
After charging or prior to charge completion, all the
charging current is used for electrolysis of the
moisture in the electrolyte with conventional
lead-based batteries. The positive plates release
oxygen and the negative plates release hydrogen gas.
If the gas recombination efficiency of the battery is
low, a large percentage of the gas will escape
reducing moisture in the battery after every charge.
This action causes the electrolyte content to
decrease due to water loss which raises the acidity in
the battery and shortens the life of the battery. This is
known as late-charge fluid-loss phenomenon.
With Crystal® batteries, the composite electrolyte has
various additives that participate in the electrochem-
ical reaction in addition to the regular chemical reac-
tion. The additives inhibit the oxygen and hydrogen
gas formation during the charging cycle increasing
the batteries’ recombination rate. This, in turn,
reduces the water loss during and after charging.
The lead sulphate can be totally transformed back