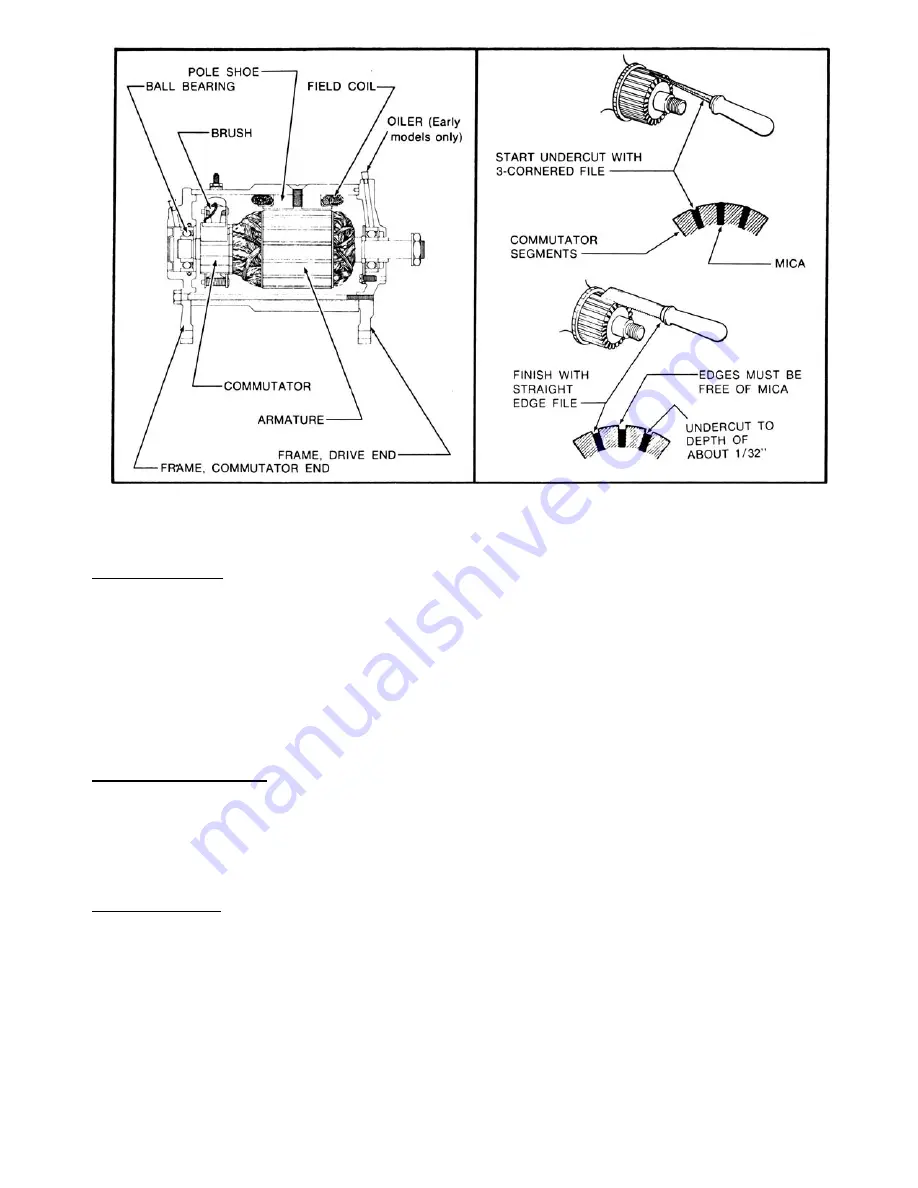
19
Figure 12 Motor - Generator, Cutaway View
Figure 13 Undercutting Mica On Commutator
be cleaned and repacked with ball bearing grease upon disassembly of the motor-generator. The armature
shaft should be wiped clean and coated with a light grade engine oil.
MOTOR TESTS:
If unit fails to crank properly, inspect entire cranking circuit for loose or badly corroded
connections and damaged wiring. Check battery to determine condition. When battery is satisfactory and
wiring and connections are in good condition, close starting switch. If unit fails to crank, wire around motor
switch with a heavy jumper lead. If motor-generator operates, the switch is defective and should be replaced.
If unit fails to operate, the trouble can be attributed to the engine or to the motor-generator. Excessive friction
in the engine from tight bearings or pistons or from too heavy oil causes hard cranking. If unit fails to crank
properly when engine is known to be in good operating condition and the rest of the cranking circuit is found
to be satisfactory, the motor-generator should be removed for further checking. With the motor-generator
removed from the engine, the armature should be checked for freedom of operation by turning the shaft.
Tight, dirty or worn bearings, a bent armature shaft or loose pole shoe screws may cause the armature to drag
and fail to turn freely. If armature does not turn freely, the motor must be disassembled.
GENERATOR TESTS:
If generator output is zero, check the commutator, brushes and internal connections.
Sticking brushes, a dirty or gummy commutator or poor connections may prevent the generator from
producing any output. Solder thrown from the commutator riser bars indicates that the generator has been
overheated from excessive output. Often this leads to an open circuit and burned commutator bars and,
consequently, no output. If the brushes are satisfactorily seated and making good contact with the commutator
and the cause of trouble is not apparent, the unit should be disassembled and tested according to
manufacturer's specifications. Special test equipment will usually be needed for further analysis.
DISASSEMBLY:
Noise emanating from a generator may be caused by a loose mounting or drive pulley. It
can also be caused by worn or dirty bearings or improperly seated brushes. Dirty bearings may sometimes be
saved by cleaning and re-lubrication, but worn bearings should be replaced. Excessive noise may result if the
brush holder is bent resulting in improper seating of the brush. Such a brush holder should be replaced. The
end frames, bearings and armatures can be removed or replaced without disturbing any electrical connections.
The brush holder assemblies are mounted individually on the walls of the field frame. To disassemble motor-
generator, use the following procedure:
1. Unscrew thru bolts and remove commutator end frame from the field frame.
2. Place armature in a vise with soft jaws and remove shaft nut, pulley and the drive end frame.
3. Remove brush holders if new ones are to be installed, by drilling out the rivets holding them to
the field frame. Install new holders, securing them to frame with new rivet or screws, nuts and
washers.