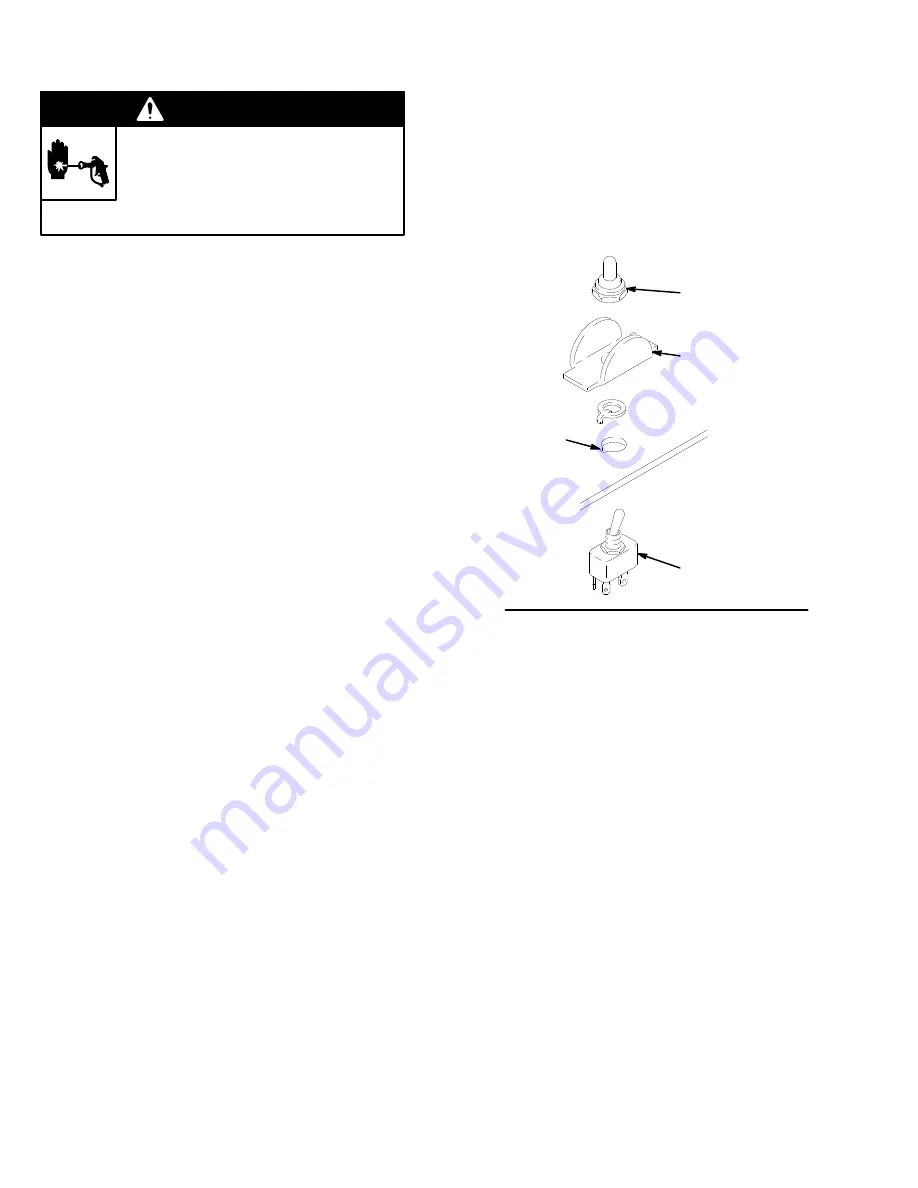
On/Off Switch Replacement (Fig. 16)
WARNING
FLUID INJECTION HAZARD
To reduce the risk of serious injury,
follow the illustrated
Pressure Relief
Procedure
warning on page 13 when-
ever you are instructed to relieve pressure.
NOTE:
Read the GENERAL REP AIR INFORMATION
on page 19 before doing this procedure.
1. Relieve pressure.
2. Remove the pressure control board/cover (301).
3. Disconnect the two wires from the ON/OFF switch
(307). See Fig. 15.
4. Using a 5/8 in. socket wrench, remove the nut and
rubber boot (309). Remove the switch guard (308).
See Fig. 16.
5. Remove the ON/OFF switch (307).
6. Install the new switch so the internal tab of the
pressure control housing (D) engages with the
vertical groove in the threads of the switch.
7. Install the switch guard (308), aligning the internal
tab with the groove in the threads.
8. Powder the inside of the rubber boot (309) with
talcum powder, then shake the excess out of the
boot.
9. Install the nut and rubber boot and tighten.
10. Reconnect all wires.
Fig. 16
307
D
308
309
04795