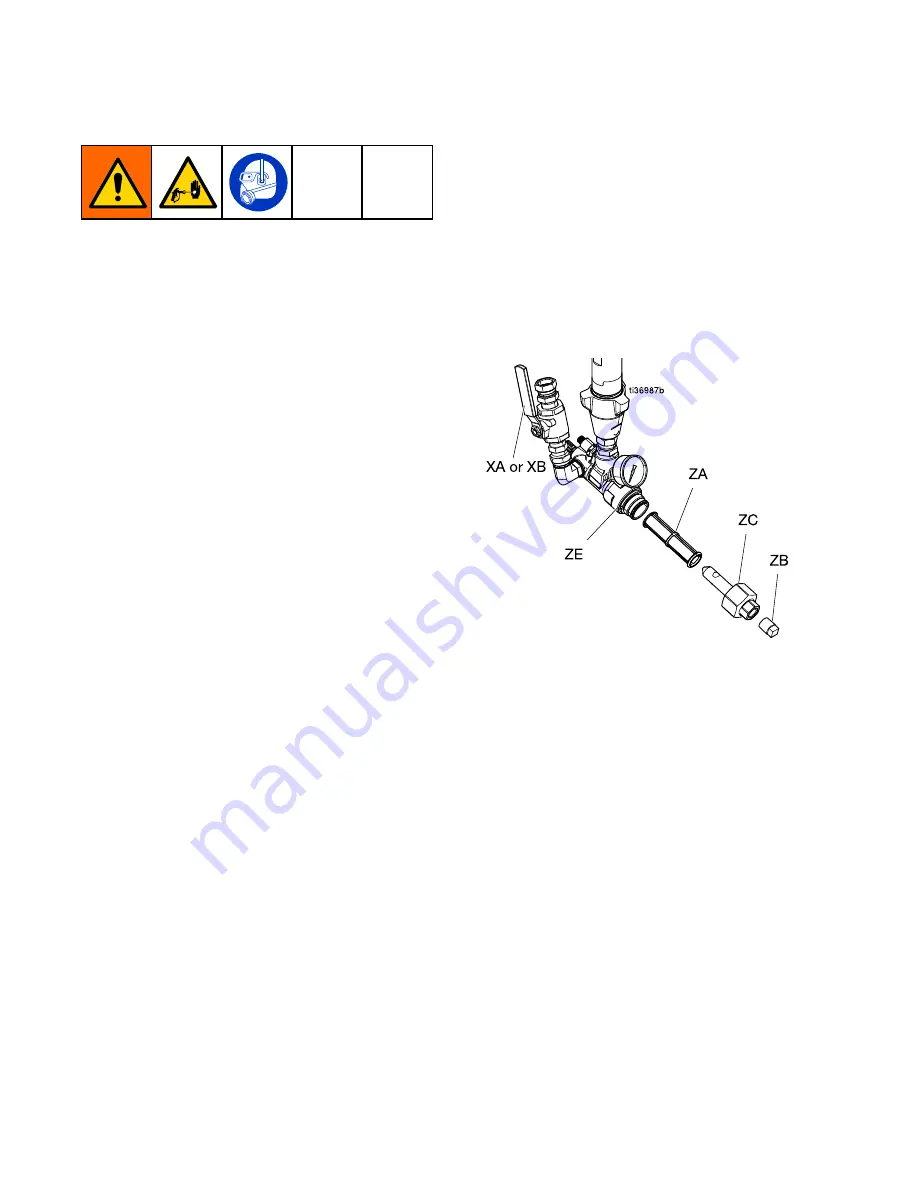
Flush
Flush
Flush Inlet
Inlet
Inlet Strainer
Strainer
Strainer Screen
Screen
Screen
The inlet strainers filter out particles that can
plug the pump inlet check valves. Inspect the
screens daily as part of the startup routine and
clean as required.
Isocyanate can crystallize from moisture
contamination or from freezing. If the chemicals
used are clean and proper storage, transfer, and
operating procedures are followed, there should
be minimal contamination of the A-side screen.
Clean the A-side screen only during daily
startup. This minimizes moisture contamination
by immediately flushing out any isocyanate
residue at the start of dispensing operations.
1. Follow the
Pressure Relief Procedure, page
.
2. Close the Fluid Inlet Valve (XA) at the pump
inlet. This prevents material from being
pumped while cleaning the screen.
3. Place a container under the strainer base to
catch fluid when removing the strainer drain
plug (ZB).
4. After the fluid has drained, remove inlet
cap (ZC) and inlet strainer screen (ZA) from
the strainer manifold. Thoroughly flush the
screen with compatible solvent and shake it
dry. Inspect the screen. No more than 25%
of the mesh should be restricted. If more
than 25% of the mesh is blocked, replace
the screen. Inspect the gasket and replace
as required.
5. Install the strainer plug (ZB) with the screen
(ZA).
6. Open the fluid inlet valve (XA), then ensure
that there are no leaks and wipe the
equipment clean. Proceed with operation.
ti36987b
Z
E
Z
A
Z
C
Z
B
XA or XB
52
3A8500E