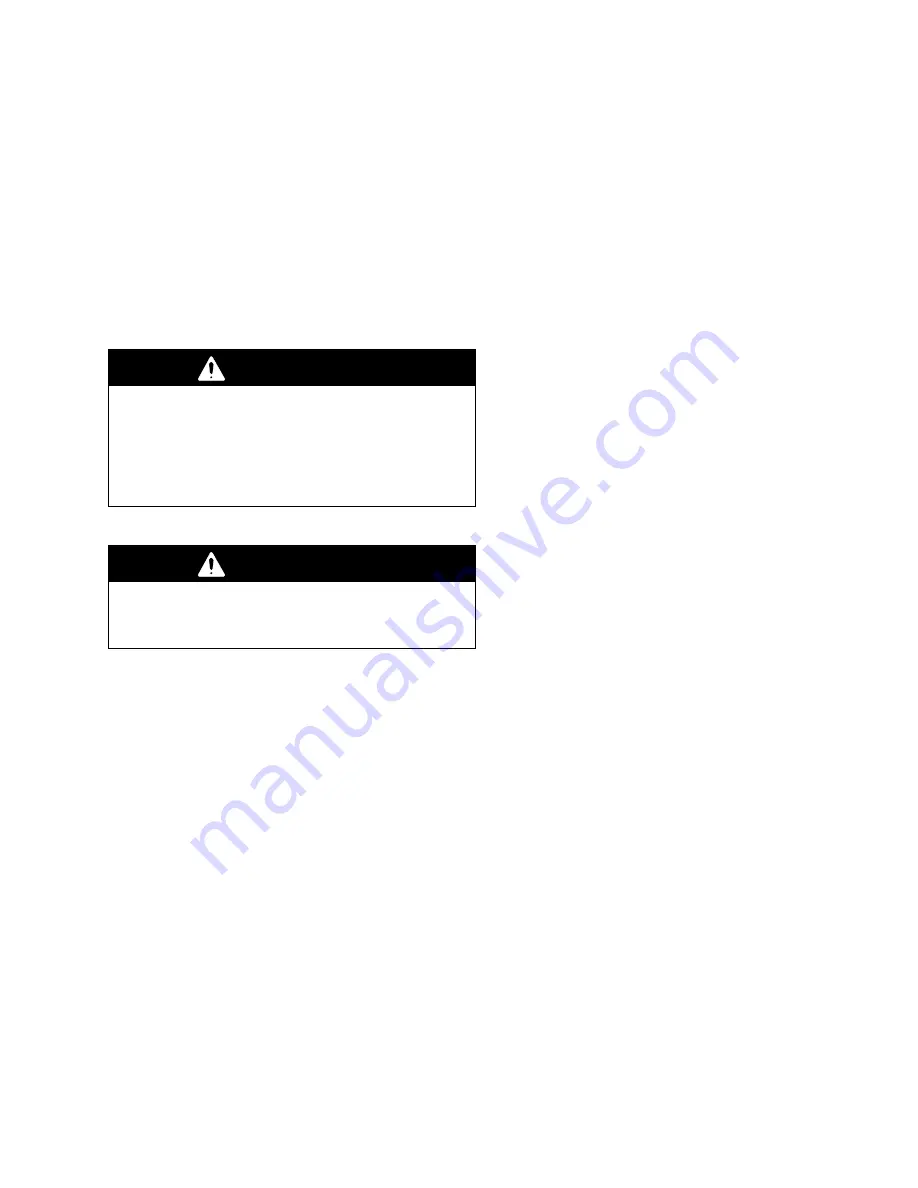
7
307001
Operation
Using Your Proportioning System
When the system is primed and operating, check the
fluid outlet pressure gauges. Check the gauges fre-
quently when using the system. Always make a note of
the pressures indicated. These notes will be helpful in
analyzing any troubles that may occur since a change
in the displacement pump performance will be indi-
cated by a change in the pressure gauge readings.
Note:
A pressure drop does occur during pump stroke
changeover.
Never exceed 120 psi (0.8 MPa, 8 bar) air pressure to
the pump.
WARNING
Always close the air supply valve to the pump
before operating the drain valves to relieve system
pressure. This will reduce the risk of excessive
pressure buildup in the opposite component hose
and fittings, and component rupture, which can
cause serious injury or property damage.
Lubrication and Care
WARNING
To reduce the risk of serious injury whenever you
are instructed to relieve pressure, always follow the
Pressure Relief Procedure
on page 6.
Keep the wet cups/packing nuts 1/3 filled with ISO
Pump Oil and check the tightness of the packing nut
weekly. The packing nut should be tight enough to
prevent leakage – no tighter. Too tight an adjustment
will cause the packings to bind or wear prematurely
and leak. Always
relieve the pressure
before adjust-
ing the packing nut.
Never allow the supply containers to run dry of the fluid
being pumped. A dry container allows air to be
pumped into the system and cause incorrect propor-
tioning. One dry displacement pump can also damage
the other displacement pump because it causes a
pressure rise in the other pump. If the supply container
is dry, stop the pump immediately, refill the container,
and prime the system. Be sure to eliminate all of the
air from the system.
Always stop the pump at the bottom of its stroke to
prevent fluid from drying on the displacement pump
which can damage the throat packings.
Flush all fluid out of the displacement pump whenever
you shut down for overnight or longer and fill the pump
with mineral spirits or rust-inhibiting solvent to prevent
corrosion.
Содержание Hydra-Cat A Series
Страница 4: ...4 307001 Notes ...