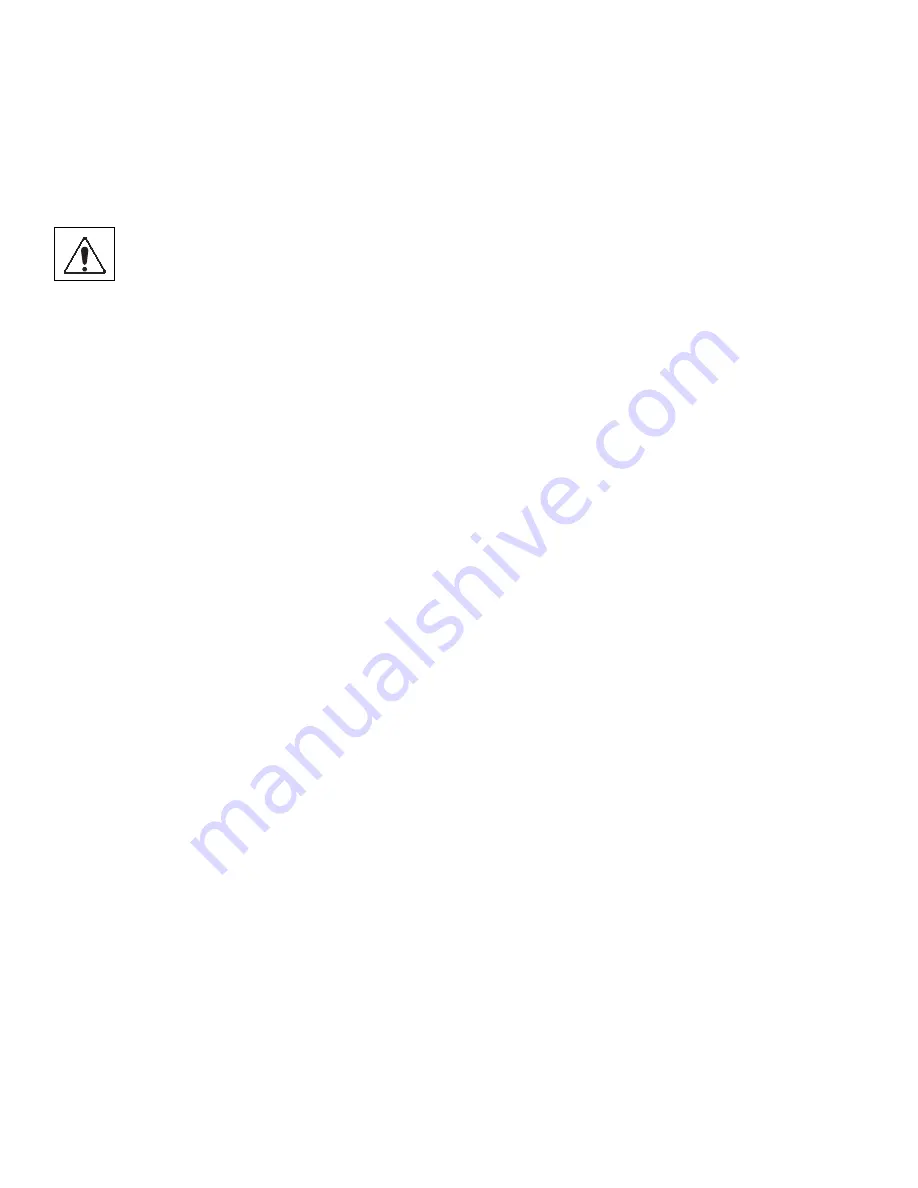
18
308981
Service
Diaphragms (Husky 515)
NOTE:
Fluid Section Repair Kit D05XXX is available. See page 22 to order the correct kit for your pump. Parts
included in the kit are marked with a double dagger (
‡
) in
and in the Parts Drawings and Lists. General pur-
Disassembly
1. Remove manifolds (102 and 103) and fluid covers
(101).
NOTE:
Make sure all the check valve parts stay in
.
2. Remove one of the fluid-side diaphragm plates (105)
(whichever one comes loose first when you use a
wrench on the hex of each), and pull the diaphragm
shaft out of the center housing (11).
Overmolded Diaphragms
: The air cover bolts may
make it difficult to remove the overmolded diaphragms
on the 515 pump. Use a flat surface that fits within the
bolt pattern to apply pressure on one of the diaphragms
to shift the diaphragm shaft to one side. Apply pressure
until the other diaphragm is separated from the air
cover. Rotate the separated diaphragm counterclock-
wise until the diaphragm assembly comes free. Pull the
second diaphragm assembly and the diaphragm shaft
(15) out of the center housing. (11)
3. Use a wrench on the flats of the diaphragm shaft (15)
to remove the other fluid-side diaphragm plate (105)
from the diaphragm shaft.
Overmolded Diaphragms
: Use a wrench on the flats of
the diaphragm shaft (15) to remove the second dia-
phragm.
4. Remove the screws (106), remove the left (114) and
right (113) air covers, and remove all old gasket (12)
material from the ends of the center housing (11) and
the surfaces of the air covers.
5. Remove the diaphragm shaft u-cups (416) and pilot
pin o-rings (1).
6. Inspect all parts for wear or damage, and replace as
necessary.
Reassembly
1. Insert a diaphragm shaft u-cup (416) and a pilot pin
o-ring (1) into the bores of the center housing (11).
NOTE:
Make sure the lips of the u-cup face out of the
center housing.
2. Line up the holes in the gasket (12) with the holes in
the end of the center housing (11), and use six screws
(106) to fasten an air cover (113 or 114) to the end of
the center housing (11). Torque the screws to 35 to
45 in-lb (4.0 to 5.1 N-m).
3. Position the exhaust cover (13) and o-ring (4) on the
center housing (11).
4. Repeat steps 1 and 2 for the other end of the center
housing and the remaining air cover.
5. Apply medium-strength (blue) thread locker to the
threads of the fluid-side diaphragm plate (105). Install
on one end of the diaphragm shaft (15) the following
parts (see proper order in
phragm plate (6), backup diaphragm (402, used only
on models with PTFE diaphragms), diaphragm (401),
and fluid-side diaphragm plate (105).
NOTE:
The words “AIR SIDE” on the diaphragm (401),
the backup diaphragm (402, used only on models with
PTFE diaphragms) and the flat side of the air-side dia-
phragm plate (6) must face toward the diaphragm shaft
(15).
Overmolded Diaphragms
: Assemble the air-side plate
(6) onto the diaphragm (401). The words AIR SIDE on
the air-side plate must face away from the diaphragm.
Apply medium-strength (blue) thread locking adhesive
to the threads of the diaphragm assembly. Screw the
assembly into the diaphragm shaft (15) hand tight.
6. Put grease on the diaphragm shaft (15), and carefully
(do not damage the shaft u-cups) run the diaphragm
shaft (15) through the center housing (11) bore.
7. Repeat step 5 for the other end of the diaphragm
shaft (15), and torque the fluid-side diaphragm plates
(105) to 80 to 90 in-lb (9 to 10 N-m) at 100 rpm maxi-
mum.
Overmolded Diaphragms
: The air cover bolts may
make it difficult to assemble the overmolded
diaphragms on the 515 pump. Two people are
needed. Use a flat surface that fits within the bolt
pattern to apply pressure on the diaphragm that has
already been assembled. Apply pressure until the
diaphragm shaft sticks out of the other end of the
center housing far enough to attach the second
diaphragm assembly. Screw the assembly into the
shaft (15) hand tight.
8. Install the muffler (3).
9. Make sure all the check valve parts are in place.
10. See
11. Reinstall the fluid covers (101) and manifolds (102
and 103), and torque the fluid cover and manifold nuts
(109) to 80 to 90 in-lb (9 to 10 N-m). See