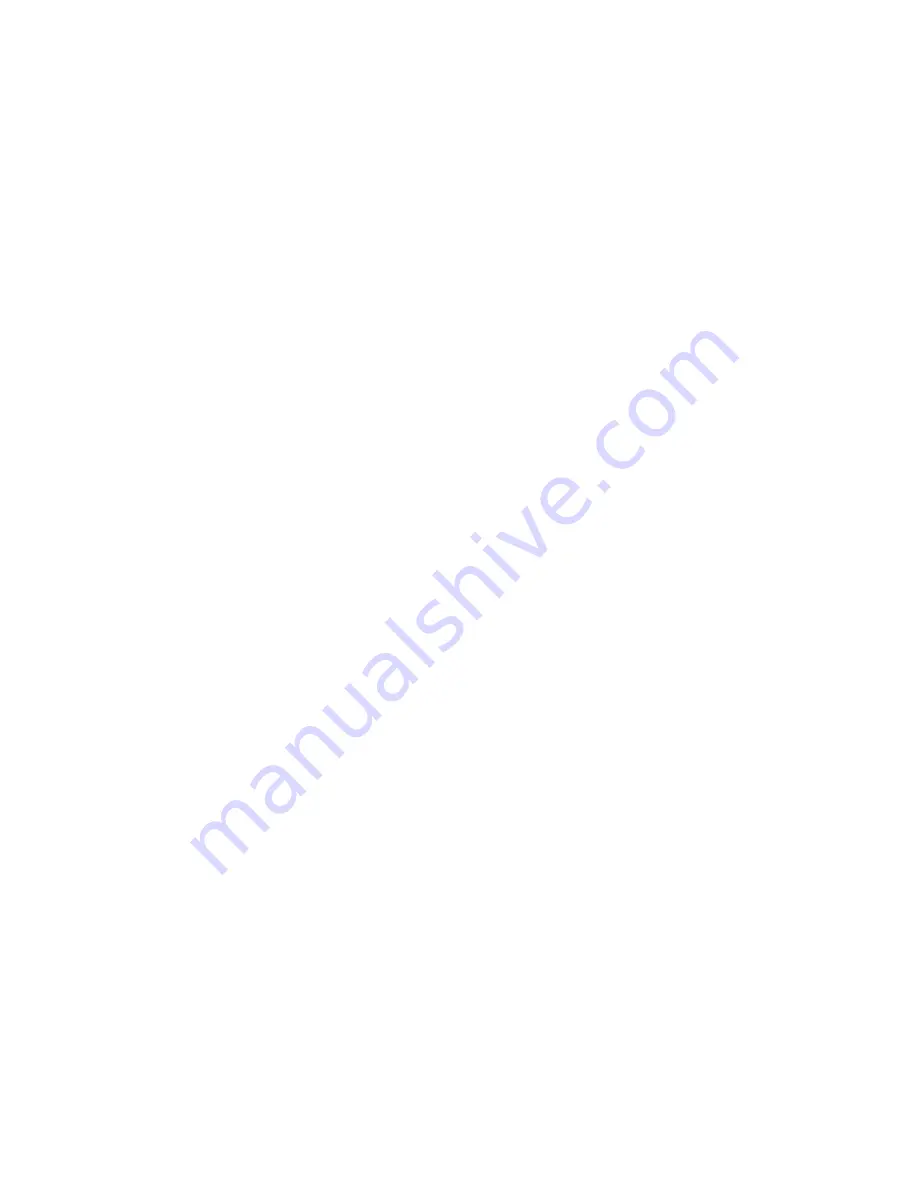
18
309015
Automatic Lubrication System Design Guide
Step 4: Determine supply line and feed line plumbing requirements
When connecting the supply line to several groups of injectors, use a branch supply line that comes off the main
supply line to prevent having to vent through a number of injector manifolds. Use the same size lines for the main
supply line and branch supply lines with these systems.
NOTE: Per JIC standards, copper tubing should not be used in lubricant systems.
Supply line recommendations:
Up to 40 ft in any one direction from the pump to the furthest injector bank.
3500 psi minimum working pressure.
1/2 in. ID hose or 1/2 in. steel tubing (.049 wall thickness) or 3/8 in. Schedule 40 pipe.
Up to 70 ft in any one direction from the pump to the furthest injector bank.
3500 psi minimum working pressure.
5/8 in. ID hose or 5/8 in. steel tubing (.049 wall thickness) or 1/2 in. Schedule 40 pipe.
Steel tubing must be soft annealed D.O.M. welded or seamless hydraulic fluid line tubing.
Feed line recommendations:
Up to 17 ft maximum hose length
3000 psi minimum working pressure.
1/4 in. ID hose.
Up to 26 ft maximum hose length
3000 psi minimum working pressure.
3/8 in. ID hose.
Step 5: Determine bill of material
From the original layout sketch determine how many injectors will be required in each group. Make sure to allow for
additional injectors for those lubrication points that require more than one injector. Determine the number of injector
manifold assemblies required for each bank of injectors and total. Include injector accessories such as cover caps
and outlet adapter kits.
Select the proper pump and reservoir assembly, timer, solenoid and necessary controls. The final step is to calcu-
late the supply line, feed line tubing, fittings and connectors for a complete system. As a rule, you can calculate 15
ft per point for the bulk feed line hose which is cut to length and assembled during installation.
Содержание 309015B
Страница 3: ...3 309015 Notes ...