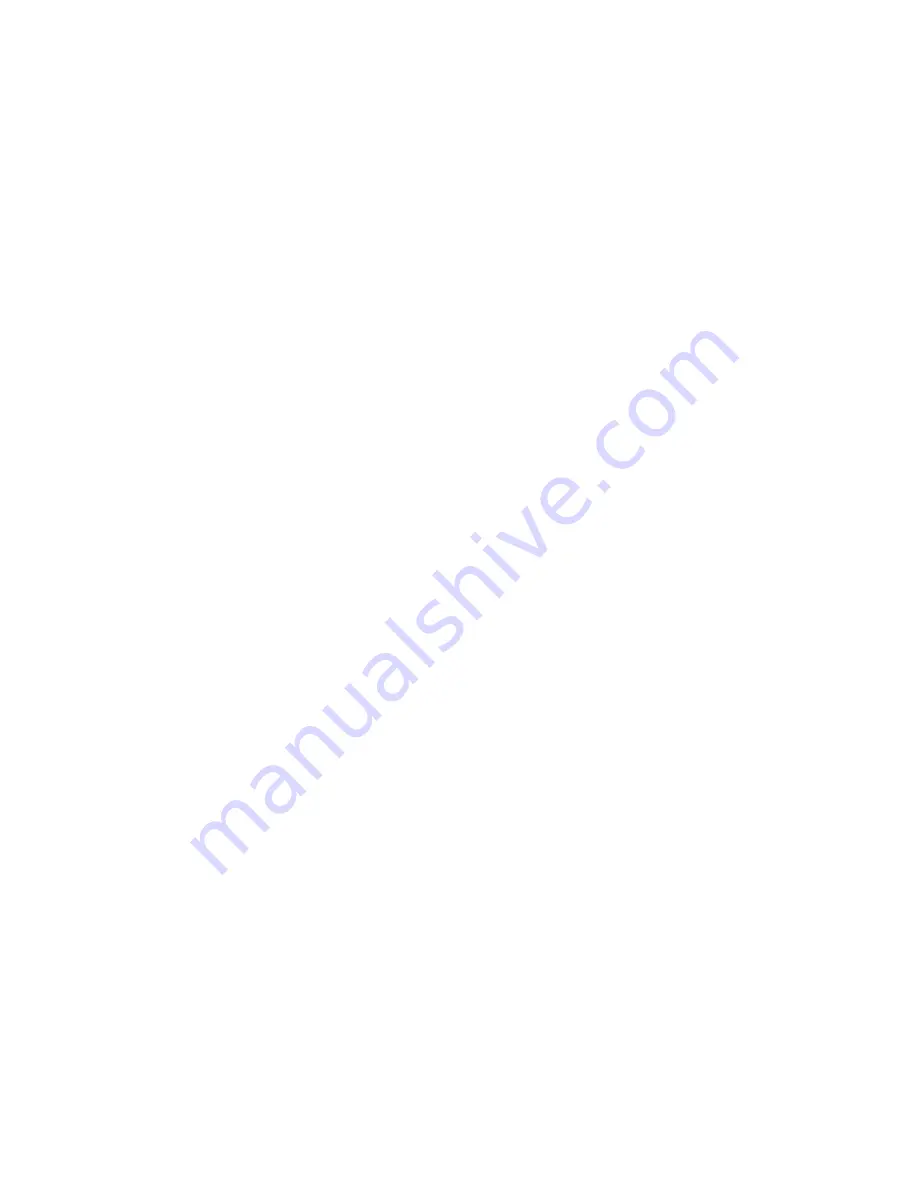
Parts
36
3A4802D
Enclosure Parts List
Ref. Part
Description Qty.
2
17R663 HOUSING, check valve, triclamp /
1 npt
1
4
17R854 NUT, 1-1/4 nps, sst
3
5
17R852 MANIFOLD, blast circuit, inlet
1
6
129574 FITTING, PTC, union y, 1/4 t
1
9
- - - - -
MANIFOLD, slurry inlet, EcoQuip
1
10
17R840 HOSE, pinch (includes 34, 37)
1
11
17R853 MANIFOLD, blast circuit, outlet,
weld
1
12
106228 FITTING, tee, street
1
13
17L324 REGULATOR, pressure, water,
185 psi (includes 32, 35, 70)
1
14
17R969 LABEL, instructions
1
15
680454 GASKET, sanitary fitting
1
19
24Z932 PUMP, water, EcoQuip, 15:1, sst
1
20
126109 FITTING, bushing, adapter,
3/8 x 1/4
1
22
▲
17R191 LABEL, warning
1
23
▲
17R192 LABEL, safety instructions
1
30
115942 NUT, hex, flange head
2
32
- - - - -
LABEL, operations
1
34
128642 CLAMP, hose, t-bolt, 1.75-2.00, sst
2
35
128670 BOLT, flange hd, serrated, m5, sst
2
37
128718 CAP, vinyl, 1/4-5/16
2
39
17K052 VALVE, pinch (includes 41, 52, 57)
1
41
128787 BOLT, button hd, 3/8-16 x 3/4, ss
2
42
128791 CLAMP, triclamp, 1.5, hex wing nut
1
44
129080 GROMMET, 1-55/64 in. id, rubber,
black
1
45
120444 SCREW, hex hd, flanged
4
48
129561 FITTING, PTC, straight,
1/4 MPT, 1/4 t
2
51
129565 FITTING, PTC, elbow, 1/8 MPT,
1/4 t
1
52
129566 FITTING, PTC, elbow, 1/4mpt, 1/4 t
10
54
EQ1500 FITTING, elbow, swivel, male,
3/8 in.
2
55
129569 FITTING, PTC, elbow, 3/8mpt, 1/4 t
5
56
17R497 HOSE, fluid, 1/4 npsm, 15.5 in.
1
57
▲
15F744 LABEL, warning, iso pinch hazard
1
59
17L622 VALVE, safety relief, 220 psi
1
61
C20179 PACKING, o-ring
1
64
17R849 REGULATOR, air, pilot, 1 npt
1
65
17S067 PLUNGER, check valve
(includes 61)
1
66
17R929 GUIDE, plunger, check valve
1
67
166863 FITTING, nipple, reducing
1
70
128918 CAP, vinyl, 3/4-13/16
1
79
128963 SPRING, 1.38 in., 2 lb/in, sst
1
▲
Replacement Danger and Warning Labels avail-
able at no cost.
Ref. Part
Description Qty.
Содержание 278860
Страница 31: ...Notes 3A4802D 31 Notes ...
Страница 35: ...Parts 3A4802D 35 Enclosure Parts WL D 1 Apply anti sieze to threads ...
Страница 37: ...Parts 3A4802D 37 Enclosure Parts continued WL D ...
Страница 43: ...Dimensions 3A4802D 43 Dimensions WL D PP PP PP ...
Страница 44: ...Notes 44 3A4802D Notes ...