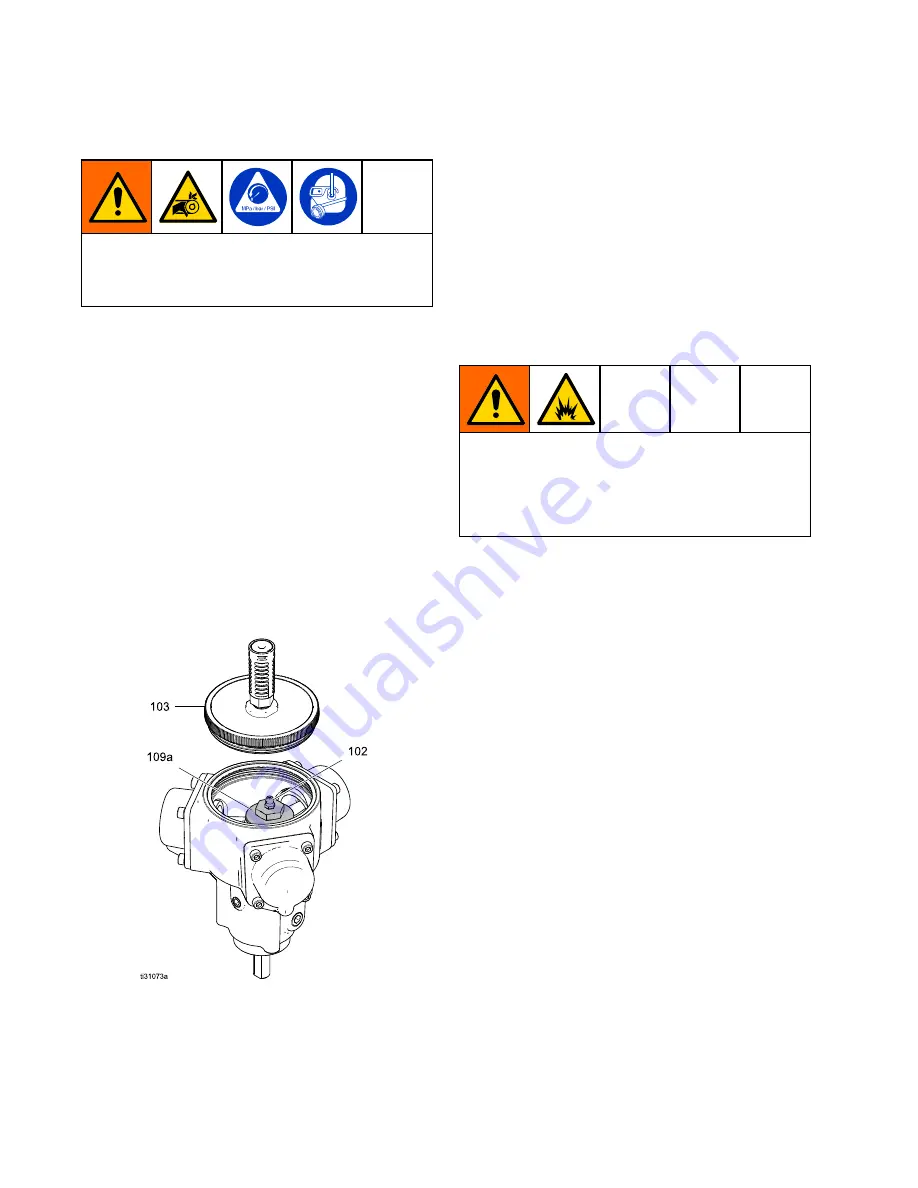
Maintenance
Maintenance
Maintenance
Moving parts, such as an impeller blade, can cut
or amputate fingers. To reduce the risk of serious
injury, always shut off the agitator and disconnect
the air line before checking or repairing the agitator.
Before performing any maintenance procedure,
follow the
Pressure Relief Procedure, page 19
Greasing
Greasing
Greasing the
the
the Air
Air
Air Motor
Motor
Motor
After approximately 20 million revolutions or every
three to four months (whichever comes first), grease
the motor needle bearing. Recommended grease:
MOBILGREASE XHP 222 SPECIAL or equivalent
with minimum flash point temperature of 399.2° F
(204° C).
1.
Follow the
Pressure Relief Procedure, page 19
.
2.
Remove the motor top cover (103).
3.
Using a manual grease gun, push grease into
the 21RC fitting (102) until grease is seen below
the top washer (109a).
Air
Air
Air Motor
Motor
Motor Muffler
Muffler
Muffler
Depending on the environment of the motor,
periodically check the cleanliness of the air motor
muffler. Dirty or clogged air mufflers result in
decreased motor efficiency and may cause the motor
to run irregularly. If the muffler is dirty or clogged,
replace it with a new muffler.
Agitator
Agitator
Agitator Blades
Blades
Blades
Materials can become electrostatically charged
when stirred or blended. To prevent fire and
explosion, ground equipment and do not allow
material to build up on agitator. Dried material
could allow static build up and interfere with
grounding.
Regularly check the agitator for dried material
buildup. Clean using a rag soaked in solvent that is
compatible with the spray material and the surfaces
being cleaned. Additionally, extra precautions need
to be taken if using lower conductive materials
(<1,000 pS/m) such as:
• Avoid stirring/mixing at high speeds.
• Avoid insoluble mixtures.
• When possible, increase the material conductivity
with additives.
• Use liquids with a high conductivity (>1000 pS/m)
20
3A4792G