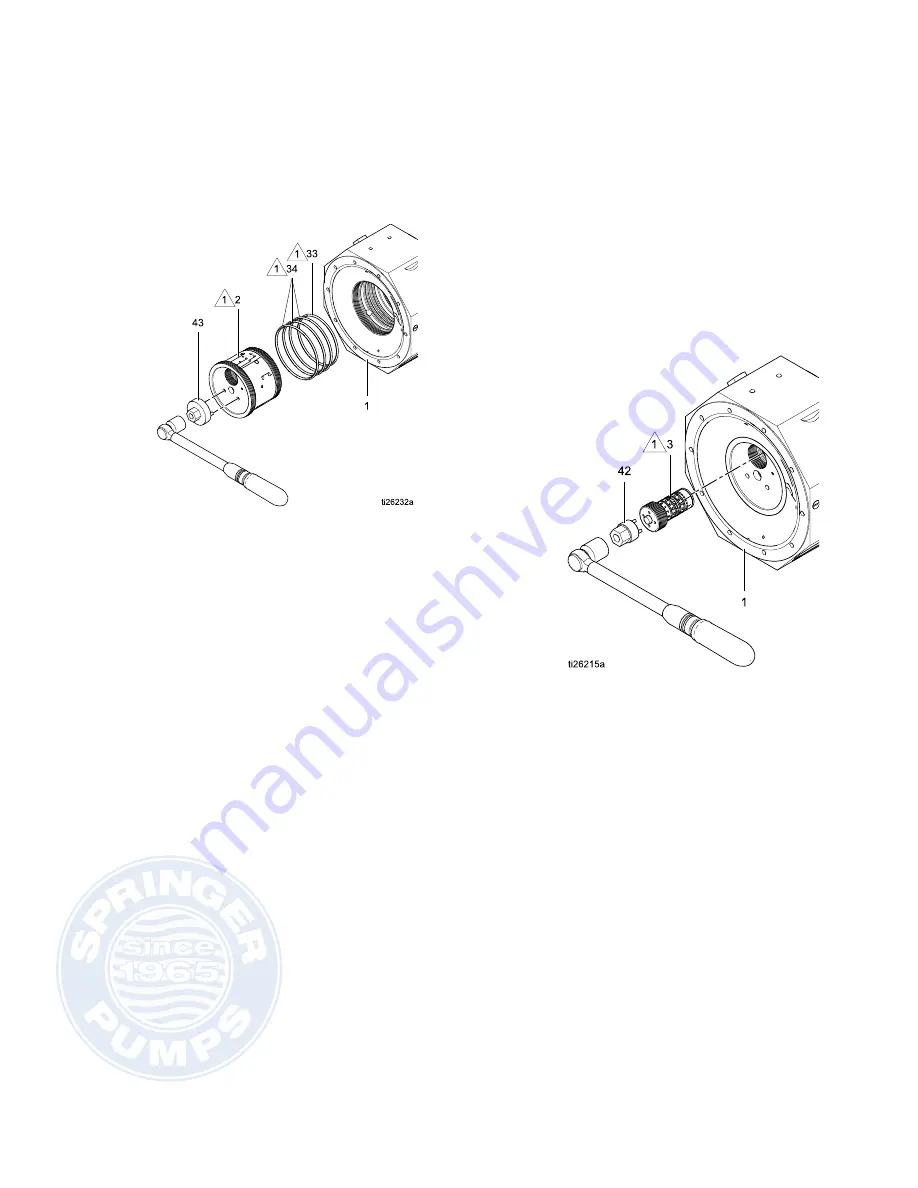
3.
Apply a thin film of lubricant (46) to air motor
o-rings (34) & (33), and to the outside of the air
motor assembly (2), and screw back into the
body (1), small end first.
NOTE:
NOTE:
NOTE: Be careful not to clog air holes with
lubricant.
NOTE:
NOTE:
NOTE: Use only the lubricant (46) supplied with
the rebuild kits.
Reassemble
Reassemble
Reassemble the
the
the Center
Center
Center Section
Section
Section
1.
Carefully lubricate the spool assembly o-rings
with a thin film of the appropriate lubricant (46).
NOTE:
NOTE:
NOTE: Be careful not to clog air holes with
lubricant.
2.
Verify the o-rings on the first spool assembly (3)
are properly seated and carefully insert it into one
of the ports of the air motor assembly (2). The
o-ring at the end of the spool assembly (3) fits
into a groove at the bottom of the port. It may be
necessary to separately insert this o-ring in the
groove first to ensure proper seating.
3.
Use a 19 mm socket and the supplied tool (42) to
tighten the spool assembly (3) until it is flush with
surface of the air motor assembly.
NOTE:
NOTE:
NOTE: Do not overtighten the spool assembly.
4.
Repeat Step 3 for the spool assembly (3) on the
other side of the air motor assembly.
5.
Perform a quick field test to verify the o-rings
were not nicked or broken when the spool
assemblies (3) were inserted.
a.
Attach an air hose to the port on the body (1).
b.
Set the air pressure to 30 psi. This will cause
one or both spools (3) to pop or shift.
c.
Press each spool (3) individually to verify that
the other spool (3) has a corresponding shift.
d.
Plug the air holes on the air motor (2) to
verify no air is escaping from either of the
spools (3).
20
334795F
Tel: 866-777-6060
Fax: 866-777-6383
Springer Pumps, LLC
Website: www.springerpumps.com
Int'l: +001 267 404 2910