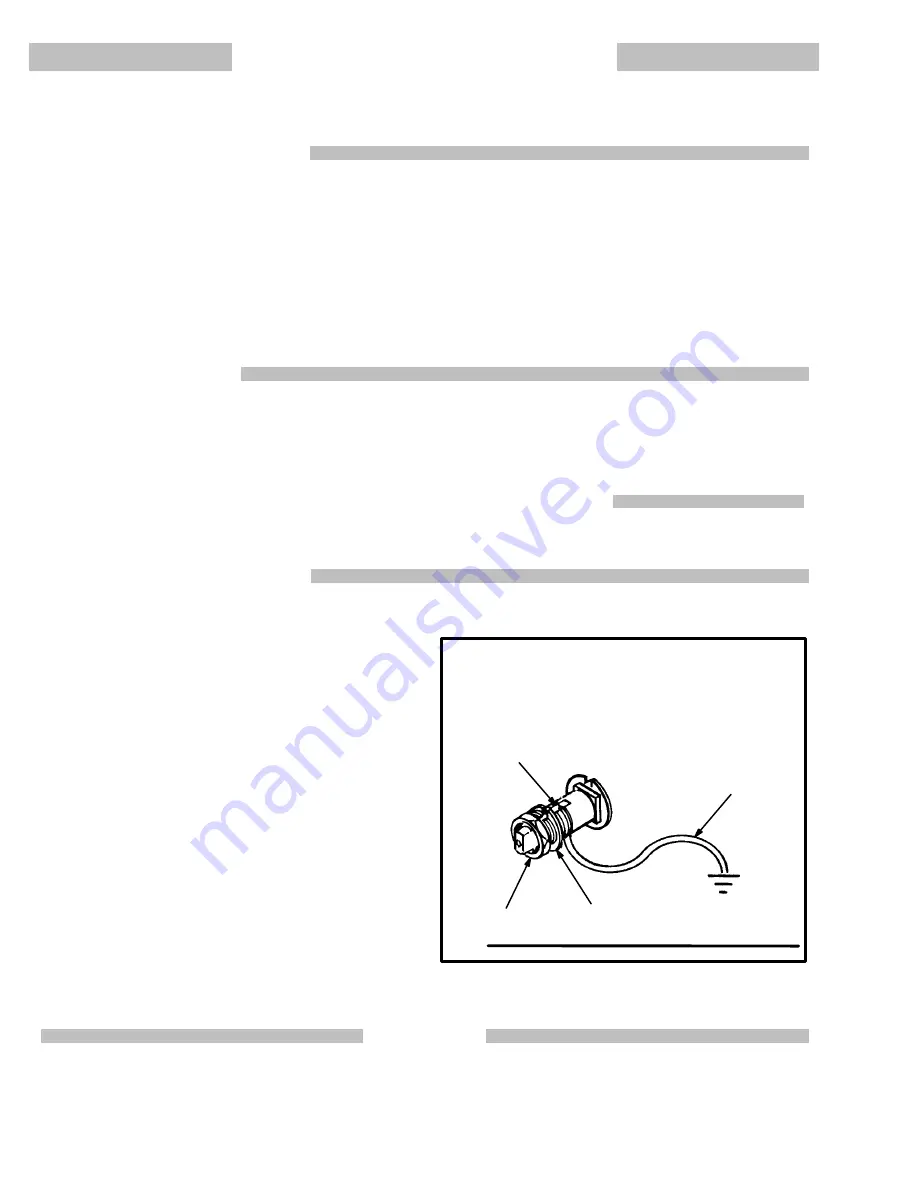
SAFETY WARNINGS
FOR PROFESSIONAL USE ONLY.
OBSERVE ALL WARNINGS.
Read And Understand All Instruction Manuals Before Operating Equipment.
EQUIPMENT MISUSE HAZARD
General Safety
Any misuse of the equipment or accessories, such as overpressurizing,
modifying parts, using incompatible chemicals and fluids, or using worn
or damaged parts, can cause them to rupture and result in serious bodily
injury, including eye injury, or fire, explosion or property damage.
NEVER alter or modify any part of this equipment; doing so could cause it
to malfunction.
CHECK all equipment regularly and repair or replace worn or damaged
parts immediately.
Take precautions to avoid a toxic fluid spill. See
TOXIC FLUID HAZARD
,
below.
System Pressure
This pump develops 8 bar (120 psi) MAXIMUM WORKING PRESSURE
at 8 bar (120 psi) incoming air pressure. NEVER exceed 8 bar (120 psi)
air pressure to the pump. DO NOT exceed the maximum working pres-
sure of any component or accessory used in the system.
Fluid Compatibility
BE SURE that all fluids and solvents used are chemically compatible with
the wetted parts shown in the
TECHNICAL DATA
on the back page. Al-
ways read the manufacturer’s literature before using fluid or solvent in
this pump.
TOXIC FLUID HAZARD
Improper handling of toxic fluids or inhaling toxic vapors can cause ex-
tremely serious bodily injury, even death, due to splashing in the eyes,
ingestion, or bodily contamination. Know what fluid you are pumping and
its specific hazards. Store toxic fluid in an appropriate, approved con-
tainer. Dispose of it according to all Local, State and Federal guidelines
for toxic fluids. Be sure to observe all the following precautions when han-
dling known or potentially toxic fluids.
1.
Always wear appropriate clothing and equipment, such as eye pro-
tection and breathing apparatus, to protect yourself.
2.
Be sure to pipe and dispose of the exhaust air safely . If the dia-
phragm fails, the fluid will be exhausted along with the air.
3.
Be sure to secure the fluid outlet hose tightly into the receiving con-
tainer to prevent it from coming loose and improperly draining the
fluid.
SUCTION HAZARD
NEVER place your hands on or near the pump suction inlet. Powerful
suction could cause serious bodily injury.
FIRE OR EXPLOSION HAZARD
Static electricity is created by the flow of fluid through the pump and hose.
If every part of the equipment is not properly grounded, sparking may oc-
cur, and the system may become hazardous. Sparking may also occur
when plugging in or unplugging a power supply cord. Sparks can ignite
fumes from solvents and the fluid being pumped, dust particles and other
flammable substances, whether you are pumping indoors or outdoors,
and can cause a fire or explosion and serious bodily injury and property
damage. Do not plug in or unplug any power supply cords in the pumping
area when there is any chance of igniting fumes still in the air.
If you experience any static sparking or even a slight shock while using
this equipment,
STOP PUMPING IMMEDIATELY.
Check the entire sys-
tem for proper grounding. Do not use the system again until the problem
has been identified and corrected.
Grounding
To reduce the risk of static sparking, ground the pump and all other spray
equipment used or located in the spray area. CHECK your local electrical
code for detailed grounding instructions for your area and type of equip-
ment. BE SURE to ground all of this spray equipment:
1.
Pump: use a ground wire and clamp as shown in Fig 1.
2.
Air and fluid hoses: use only grounded hoses with a maximum of
150 m (500 ft) combined hose length to ensure grounding continuity.
3.
Air compressor: according to the manufacturer ’s recommenda-
tions.
4.
All solvent pails used when flushing, according to local code. Use
only metal pails, which are conductive. Do not place the pail on a
nonconductive surface, such as paper or cardboard, which inter-
rupts the grounding continuity.
5.
Fluid supply container: according to your local code.
To ground the pump:
To ground the pump, loosen the grounding lug locknut (W) and
washer (X). Insert one end of a 1.5 mm
@
(12 ga) minimum ground
wire (Y) into the slot in lug (Z) and tighten the locknut securely. See
Fig 1. Connect the clamp end of the wire to a true earth ground. Refer
to ACCESSORIES on page 20 to order a ground wire and clamp.
Fig 1
W
X
Y
Z
IMPORTANT
United States Government safety standards have been adopted under the Occupational Safety and Health Act. These standards – particularly the Gen-
eral Standards, Part 1910, and the Construction Standards, Part 1926 – should be consulted.