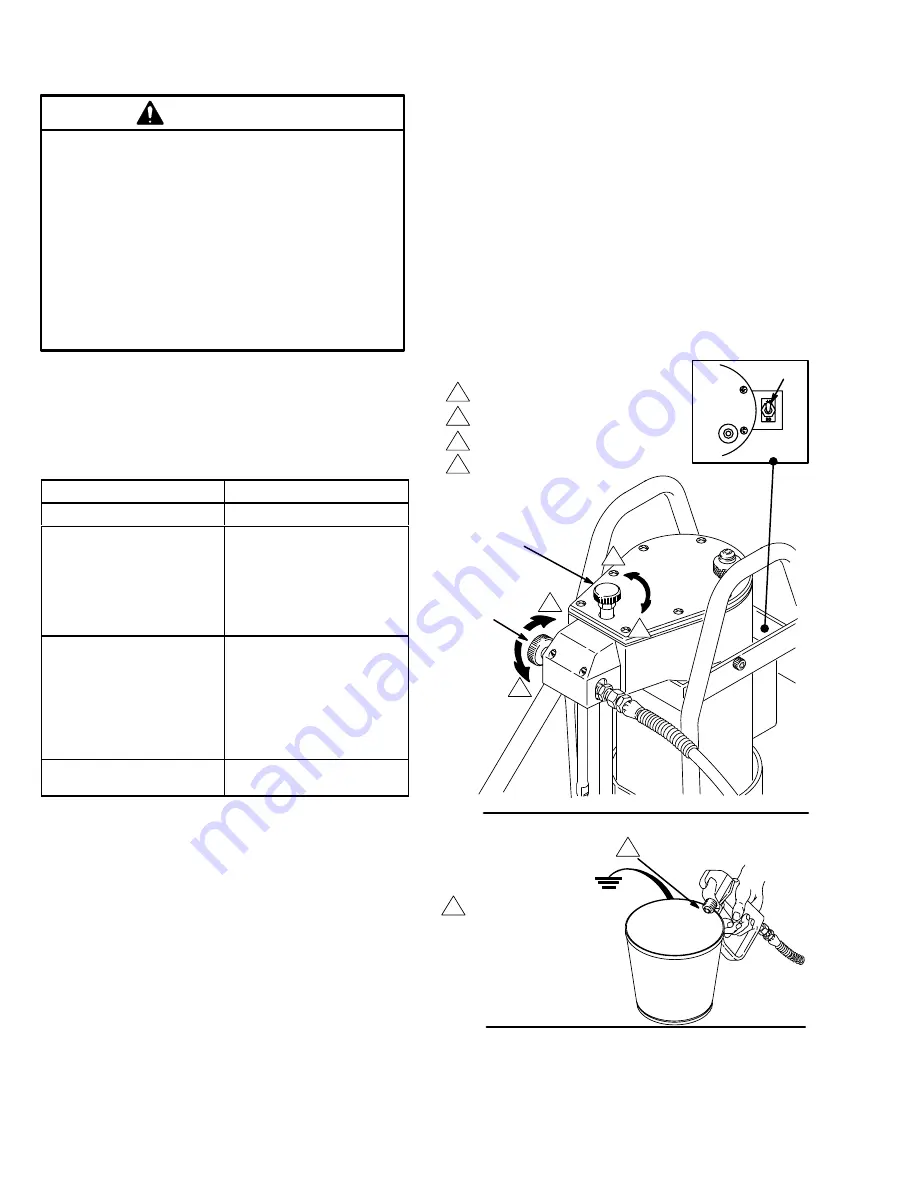
Maintenance
Thorough flushing and proper maintenance are
essential to keep the sprayer working properly
and avoid costly damage to the sprayer or the ob-
ject being sprayed.
Diaphragm Failure: Always replace the diaphragm
after every 500 hours of operation (once every 4 to 6
months). The diaphragm weakens with use. If the
diaphragm ruptures, hydraulic oil and paint may mix,
damaging the sprayer and/or the surface of the object
being sprayed may be damaged.
Follow the Maintenance Intervals outlined below.
CAUTION
Maintenance Intervals
Flushing
Immediately after each use.
Lubricate the intake valve.
Immediately after each use.
Tighten the paint pump
screws and the inlet valve.
1. After the first 3 to 5 hours of
operation.
2. After the next 3 to 5 hours
of operation.
3. Each 25 hours thereafter
(about weekly).
Check or change the hydrau-
lic oil.
1. Check the oil after each
use of the sprayer.
2. Change the oil after the first
20 hours of operation.
3. Change the oil each 50
hours thereafter (about twice
monthly).
Replace the diaphragm.
After every 500 gallons of
paint sprayed (4 to 6 months).
Flushing Procedure
1.
Shut off the sprayer. Lock the gun trigger safety le-
ver. Open the bypass valve ONE turn counterclock-
wise. Raise the paint pump just above the paint and
turn on the sprayer to drain the paint. Now turn off the
sprayer. See Fig. 7.
2.
Place the paint pump in a grounded flushing pail of
solvent.
3.
Check to be sure the trigger safety lever is locked.
Remove the spray tip from the gun. Unlock the safety
lever. Hold a metal part of the gun firmly to the side
of a grounded metal pail. Close the bypass valve.
Trigger the gun into the pail. Turn on the sprayer.
Watch the side of the pail for solvent to appear. Then
release the gun trigger. Turn off the sprayer.
4.
With the bypass valve closed, turn on the sprayer,
trigger the gun into the flushing pail and allow the sol-
vent to circulate through the hose and gun for two to
three minutes, using the lowest possible pressure.
See Fig. 8. Release the gun trigger and lock the safe-
ty lever. Turn off the sprayer.
Fig. 7
Decrease pressure
(counterclockwise).
Increase pressure (clockwise).
Open (counterclockwise).
Close (clockwise).
66
4
11
Maintain firm metal–
to–metal contact
between gun and
container
Fig. 8
ÄÄ
ÄÄ
ÄÄ
Содержание 218-501
Страница 11: ... Notes ...
Страница 15: ...307 711 15 Notes ...