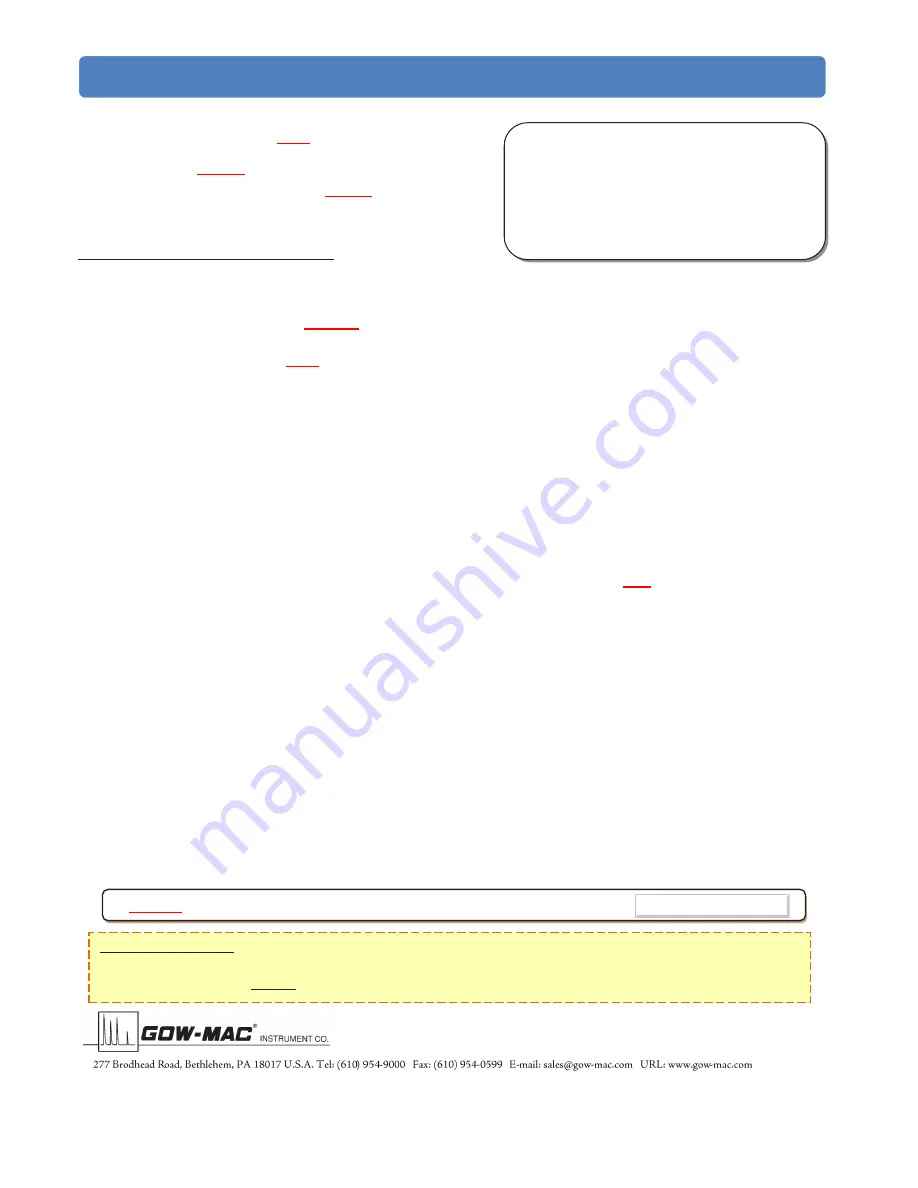
44
GOW-MAC Instrument Co.
Health and Safety Declaration for the Return of GOW-MAC Instrument Co. Equipment
In order to protect our employees from exposure to various hazards, the
following statements and/or questions
MUST
be answered by you. Fill out this
document in its entirety and either fax or e-mail it to GOW-MAC Instrument
Co., Attn: Repair Dept,
BEFORE
returning the product.
The instrument/device/part being returned
will not
be accepted into
GOW-MAC’s facility until we receive this completed document. Once the
product has been approved for return by our Chemical Safety Officer, an
acknowledgement will be promptly issued to you with notification of your
Return Materials Authorization (RMA) number
and the procedure to follow
for returning the product.
All applicable regulations should be followed when
returning instrumentation, devices, and or parts.
If this form is not approved by our chemical safety officer, the instrument/device/part
WILL NOT
be permitted into our facility for servicing!
A] Briefly list the application(s) for which the instrument/device/part was used, as well as any and all chemicals, gases, and/or materials
analyzed and their concentrations. (
MUST be filled in
): ________________________________________________________________
____________________________________________________________________________________________________________
B] Is there the possibility of internal or external contamination on or in this instrument/device/part?
Yes – see below
No – proceed to C.
Please check the appropriate box.
Chemicals or Substances That Are Hazardous to Health
Blood, Body Fluids, (e.g. Urine, Secretions), Pathological Specimens
Regulated Medical Wastes
Infectious Substances or other Bio-Agents (e.g. Protein, Enzymes, Antibodies)
Radioactive Isotopes used in the area. Detail type (ECD, Isotopic Labels, etc) and Activity in Micro Curies
Biodegradable Material That Could Become Hazardous
Other Hazards ____________________________________________________________________________________________
If any of the above boxes are checked the following statements and/or questions
must
be answered.
1. Specifically describe where (on or in) the instrument/device/part there could be any residual contamination (for example: blood spill
on the surface).____________________________________________________________________________________________
________________________________________________________________________________________________________
2. Provide details of these hazards. Include names, Material Safety Data Sheets (MSDS), and concentration of contaminants, where
possible. ________________________________________________________________________________________________
________________________________________________________________________________________________________
3. Describe the method of decontamination used. Attach Procedure.____________________________________________________
________________________________________________________________________________________________________
C] I declare that the above information is true and complete to the best of my knowledge. I acknowledge that any inconsistencies between
the condition of the instrument and the statements made on this form will delay the repair process.
Authorized signature _________________________________________________ Date: ____________________________________
Name (Printed) ______________________________________________________ Phone number: ____________________________
Company name: ____________________________________________________ Fax number: ______________________________
Shipping address: _____________________________________________________________________________________________
City: _________________________________________ State/Country: _______________________ Zip :_______________________
E-mail address: ______________________________________________________________________________________________
BEFORE
item can be shipped, fax completed form to: (610) 954-0599 or e-mail it to: [email protected]
Customer to Record the Following:
Model # / Part #:
___________________
Serial #:
___________________
Service Technician spoken to: ___________________
Today’s Date:
___________________
For GOW-MAC Use Only:
Signed: ________
Date ____/____/____
□
Passed
Safety Inspection.
OK
to proceed to Repair Dept.
Chem. Safety Off.
Comments: ( ) None
□
Failed Safety Inspection. DO NOT
proceed to Repair Dept.
RMA No: __________________
( ) On Back >>>>
Содержание 5900 Series
Страница 2: ......
Страница 16: ...16 GOW MAC Instrument Co ...
Страница 22: ...22 GOW MAC Instrument Co ...
Страница 30: ...30 GOW MAC Instrument Co ...