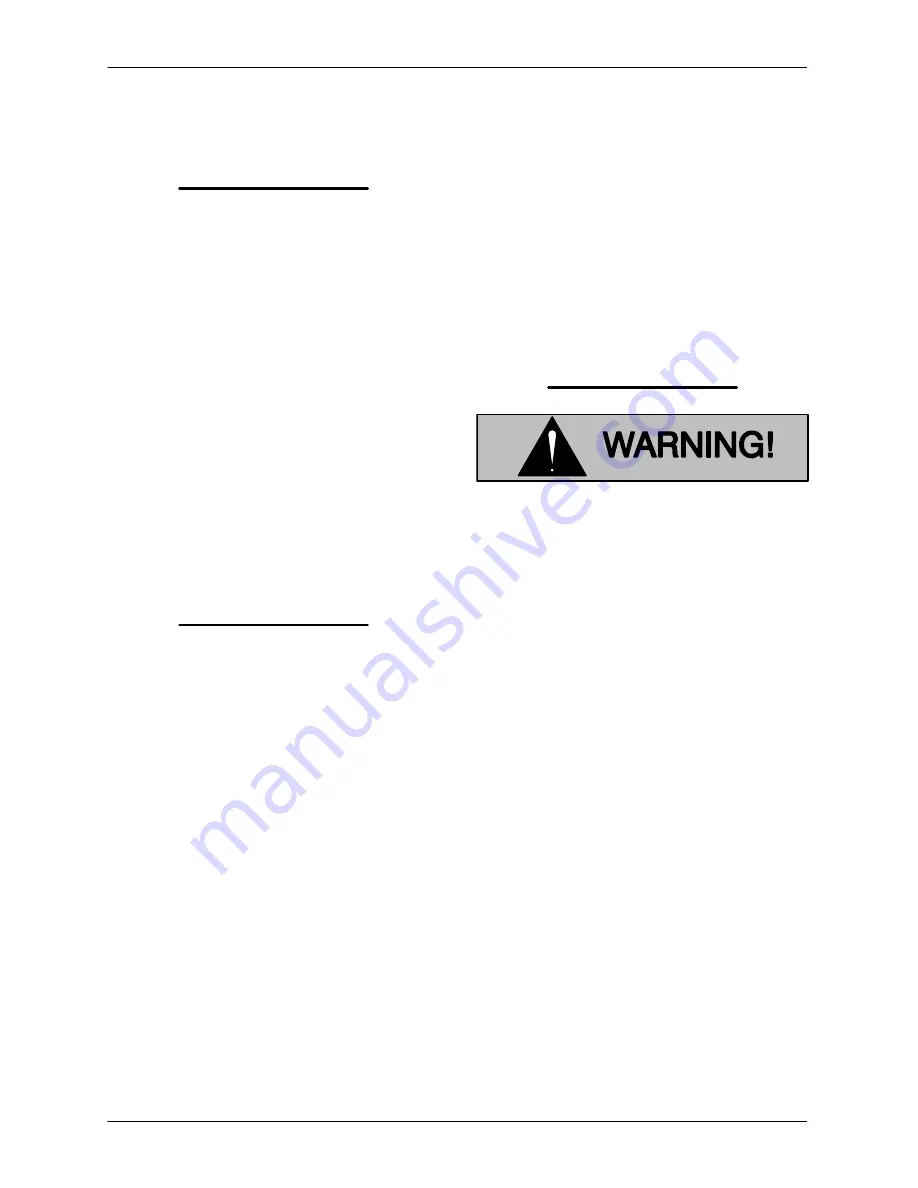
S SERIES PUMPS
OM-07089
MAINTENANCE AND REPAIR
PAGE E - 16
the diffuser, the shaft and lower bearing have been
driven out of position during impeller removal. If this
occurs, the lower bearing must be pressed back
into place (see
MOTOR DISASSEMBLY
and
MO
TOR REASSEMBLY
).
After the impeller has been installed, coat the
threads of the rotor shaft with `Loctite Threadlocker
No. 242' or equivalent compound. Install the impel
ler nut (27). Block impeller rotation with a steel rod,
install the impeller nut (27) and torque to 300 ft. lbs.
(3600 in. lbs. or 41,5 m. kg.).
Suction Head And Wear Ring Installation
(Figure E-1)
If the wear ring (5) was removed, position the re
placement ring in the suction head with the cham
fered end toward the bore shoulder. Press the wear
ring into the suction head until fully seated.
NOTE
The wear ring
must
seat squarely in the suction
head; otherwise, binding and/or excessive wear
will occur as the shaft turns.
Install the suction head gasket (6). Position the
suction head (4) on the first stage diffuser. Apply
`Never‐Seez' or equivalent compound on the
threads of the capscrews (29) and secure the suc
tion head with the hardware (28 and 29). Torque
the capscrews in a cross sequence to 120 ft. lbs.
(1440 in. lbs or 16,6 m. kg.).
Strainer Installation
(Figure E-1)
Inspect the strainer screen (3) for cracks, distortion
or erosion, and replace it if defective.
Install the strainer screen and the base plate (1).
Apply `Loctite Threadlocker No. 242' or equivalent
compound on the threads of the capscrews (2),
and secure the complete strainer assembly to the
first stage diffuser. Tighten the nuts just enough to
draw the strainer screen down tightly, but not tight
enough to distort it. Make certain that the strainer
seats properly against the shoulder of the diffuser.
See
LUBRICATION
and
FINAL ASSEMBLY
be
fore putting the pump back into service.
MOTOR DISASSEMBLY
Disassembly of the motor is rarely required except
to replace the motor rotor, stator or bearings. Do
not disassemble the motor unless it is necessary
and a clean, well‐equipped shop is available.
NOTE
It is recommended that a pump with a defective mo
tor be returned to Gorman‐Rupp, or to one of the
Gorman‐Rupp authorized Submersible Repair
Centers.
The electrical power used to operate
this pump is high enough to cause inju
ry or death. Make certain that the control
handle on the control box is in the off po
sition and locked out, or that the power
supply to the control box has been
otherwise cut off and locked out, before
attempting to open or service the pump
assembly. Tag electrical circuits to pre
vent accidental start‐up.
Carefully inspect any O‐rings or gaskets before re
moval and cleaning to determine if a proper seal
and compression existed prior to disassembly. If
sealing was faulty or questionable, the cause must
be determined and corrected before reassembly.
Replace any parts as required.
Terminal Housing And Power Cable
Removal And Disassembly
(Figure E-1)
Total disassembly of the terminal housing and
power cable (65) is not always required. Disassem
ble and replace
only
the parts proven defective by
inspection or testing. See
Electrical Testing
in
TROUBLESHOOTING
.
The terminal housing and power cable assembly
(65) may be serviced without disassembling the
motor housing or pump end.