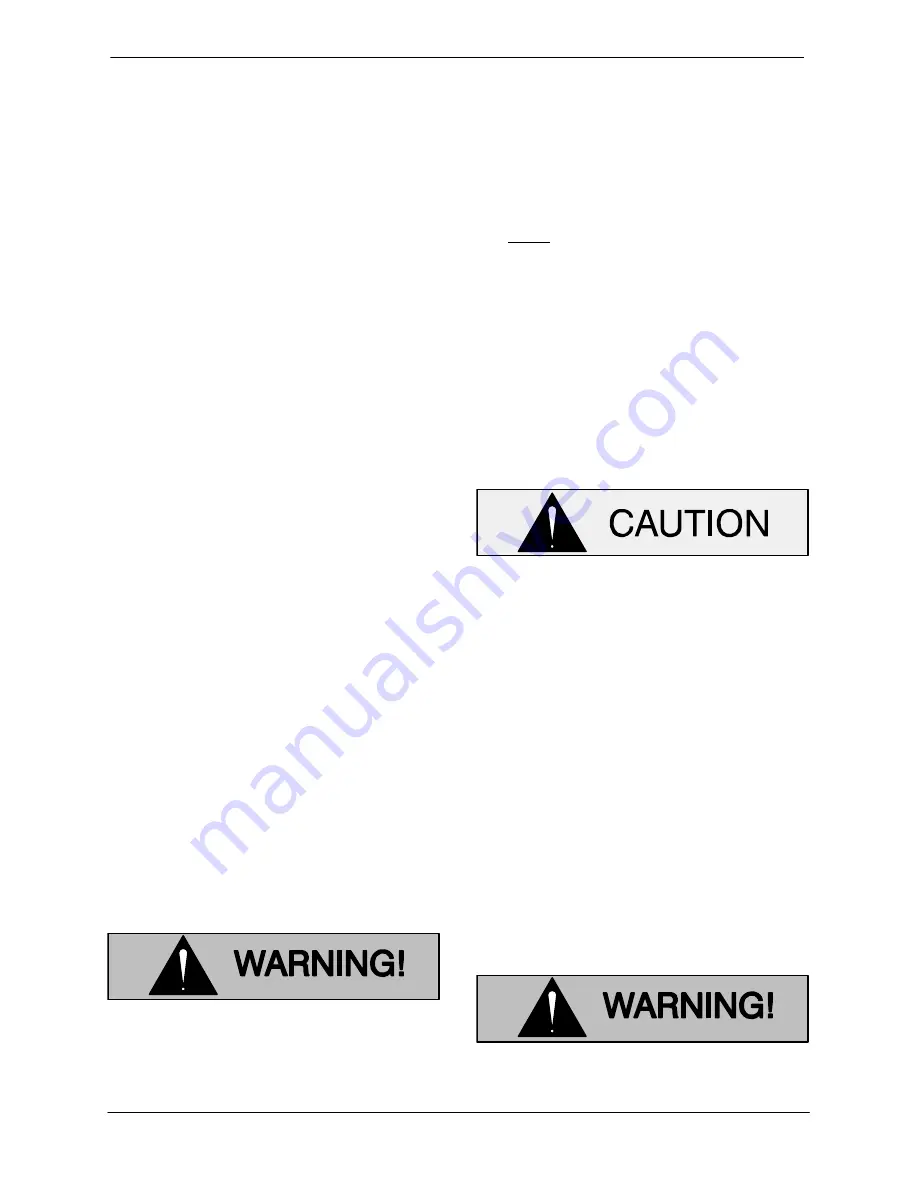
OM−06078
PA SERIES
PAGE B − 2
INSTALLATION
c. Carefully read all tags, decals, and markings
on the pump assembly, and perform all duties
indicated. Note that the pump shaft rotates in
the required direction.
d. Check levels and lubricate as necessary. Re-
fer to
LUBRICATION
in the
Maintenance and
Repair Manual
and perform duties as in-
structed.
e. If the pump has been stored for more than 12
months, some of the components or lubri-
cants may have exceeded their maximum
shelf life. These
must be inspected or re-
placed
to ensure maximum pump service.
If the maximum shelf life has been exceeded, or if
anything appears to be abnormal, contact your
Gorman-Rupp distributor or the factory to deter-
mine the repair or updating policy.
Do not
put the
pump into service until appropriate action has
been taken.
Battery Installation
Unless otherwise specified on the pump order, the
engine battery is
not
included with engine driven
units.
Refer to the information accompanying the battery
and/or electrolyte solution for activation and charg-
ing instructions.
Before installing the battery, clean the positive and
negative cable connectors, and the battery termi-
nals. Secure the battery by tightening the
holddown brackets. The terminals and clamps
may be coated with petroleum jelly to retard corro-
sion. Connect and tighten the positive cable first,
then the negative cable.
POSITIONING PUMP
Use lifting and moving equipment in
good repair and with adequate capacity
to prevent injuries to personnel or dam-
age to equipment. Attach lifting equip-
ment to the lifting device fitted to the
pump. If chains or cable are wrapped
around the pump to lift it, make certain
that they are positioned so as not to
damage the pump, and so that the load
will be balanced. The bail is intended for
use in lifting the pump assembly only.
Suction and discharge hoses and pip-
ing must be removed from the pump be-
fore lifting.
Lifting
Pump unit weights will vary depending on the
mounting and drive provided. Check the shipping
tag on the unit packaging for the actual weight, and
use lifting equipment with appropriate capacity.
Drain the pump and remove all customer-installed
equipment such as suction and discharge hoses
or piping before attempting to lift existing, installed
units.
The pump assembly can be seriously
damaged if the chains or cables used to lift
and move the unit are improperly wrapped
around the pump.
Mounting
Locate the pump in an accessible place as close as
practical to the liquid being pumped. Level mount-
ing is essential for proper operation. The pump
may have to be supported or shimmed to provide
for level operation and eliminate vibration.
For engine driven units, the pump
must
be posi-
tioned as level as possible to ensure sufficient lubri-
cation and fuel supply to the engine.
If the pump has been mounted on a moveable
base, make certain the base is stationary by setting
the brake and blocking the wheels before attempt-
ing to operate the pump.
If the pump has been mounted on a mov-
able base, do not attempt to operate the
pump unless the unit is level. Be sure
Содержание PA4C60-4045H
Страница 22: ...OM 06078 PA SERIES MAINTENANCE REPAIR PAGE E 2 PARTSPAGE SECTION DRAWING Figure 1 Pump Model PA4C60 4045H...
Страница 24: ...OM 06078 PA SERIES MAINTENANCE REPAIR PAGE E 4 SECTION DRAWING Figure 2 46143 064 Power Unit Kit...
Страница 26: ...OM 06078 PA SERIES MAINTENANCE REPAIR PAGE E 6 SECTION DRAWING Figure 3 PA4C60 SAE 4 10 Pump End Assembly...
Страница 28: ...OM 06078 PA SERIES MAINTENANCE REPAIR PAGE E 8 SECTION DRAWING Figure 4 Pump Assembly...