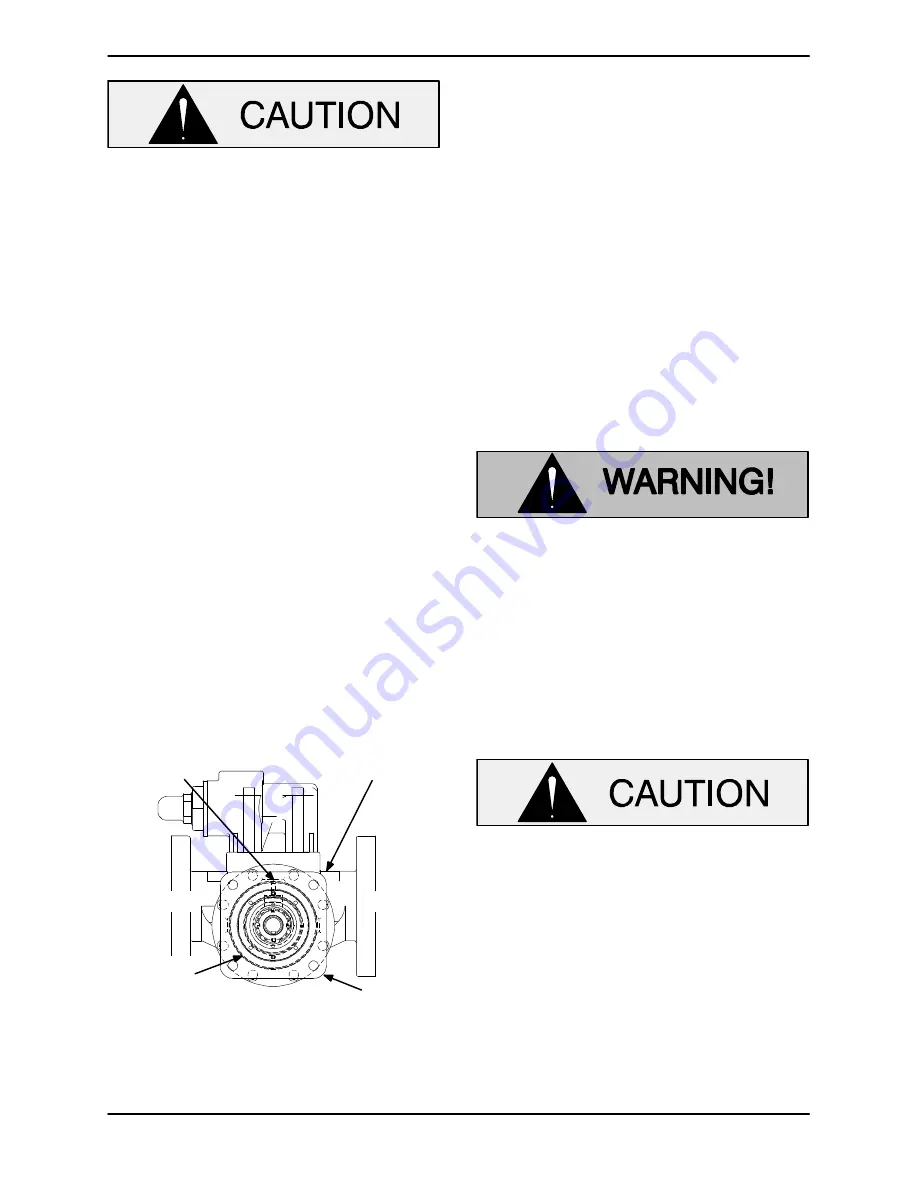
GHC SERIES
OM-05845
PAGE E-9
MAINTENANCE AND REPAIR
If the socket head pipe plugs (P) in the
back side of the housing were removed in
order to change the direction of pump rota
tion, the smaller diameter plug
must
be
installed in the hole adjacent to the dis
charge port of the housing. Otherwise,
over‐pressurization of the seal cavity could
result in premature seal failure.
If the socket head pipe plugs (P) in the back side of
the housing were removed, install the smaller di
ameter plug in the hole adjacent to the discharge
port, and install one of the larger diameter pipe
plugs over the smaller one. Install the second large
pipe plug in the other hole in the back of the hous
ing adjacent to the suction port.
Backhead Kit (06
)
(Figures E‐1 and E‐4)
Position the backhead (06A) on the bed of an arbor
(or hydraulic) press with the rotor end facing up.
Use an arbor (or hydraulic) press and a suitably
sized dowel to install the shaft bushing in the back
head until it is just flush with the machined face.
Apply a small amount of grease to the gasket (06B)
to hold it in place and position it against the hous
ing (04).
BACKHEAD
HOUSING
BALANCE
HOLE AT 12
O'CLOCK
3 O'CLOCK
9 O'CLOCK
ROTOR
ADJUSTING
SLEEVE
Figure E‐4.
Housing/Backhead
Alignment
Position the backhead assembly (06A) against the
housing (04) with the balance hole in the backhead
in the 12 o'clock position (see Figure E‐4). Secure
with the capscrews (B).
Rotor/Shaft Assembly (03)
Inspect the rotor/shaft assembly (03A) for exces
sive wear, scoring or scratches along the shaft
sealing surface. If replacement is required, the
shaft and rotor must be replaced as an assembly.
Small scratches can be dressed with a fine file or
emery cloth. Replace the rotor/shaft assembly or
any other parts if wear or damage is extensive.
Slide the rotor/shaft assembly into the housing and
backhead.
Use caution
not to scratch the I.D. of
the bushing (06AE).
Seal Installation (05)
Clean the seal cavity and shaft with a cloth soaked
in fresh cleaning solvent.
Most cleaning solvents are toxic and
flammable. Use them only in a well ven
tilated area free from flame, sparks, and
excessive heat. Read and follow all pre
cautions printed on solvent containers.
The seal is not normally reused because wear pat
terns on the finished faces cannot be realigned
during reassembly. This could result in premature
failure. If necessary to reuse an old seal in an emer
gency,
carefully
wash all metallic parts in fresh
cleaning solvent and allow to dry thoroughly.
Seal components
must
be kept clean.
Handle seal parts with extreme caution to
prevent damage. Use care not to contami
nate the precision‐finished faces; even fin
gerprints on the faces can shorten seal life.
If necessary to clean the faces, use a clean
cloth and wipe in a circular pattern.
Inspect the seal components for wear, scoring,
grooves, and other damage that might cause leak
age. If any components are worn, replace the com
plete seal;
never mix old and new seal parts
.
If a replacement seal is being used, unwrap the
mechanical seal components. Check that the seal