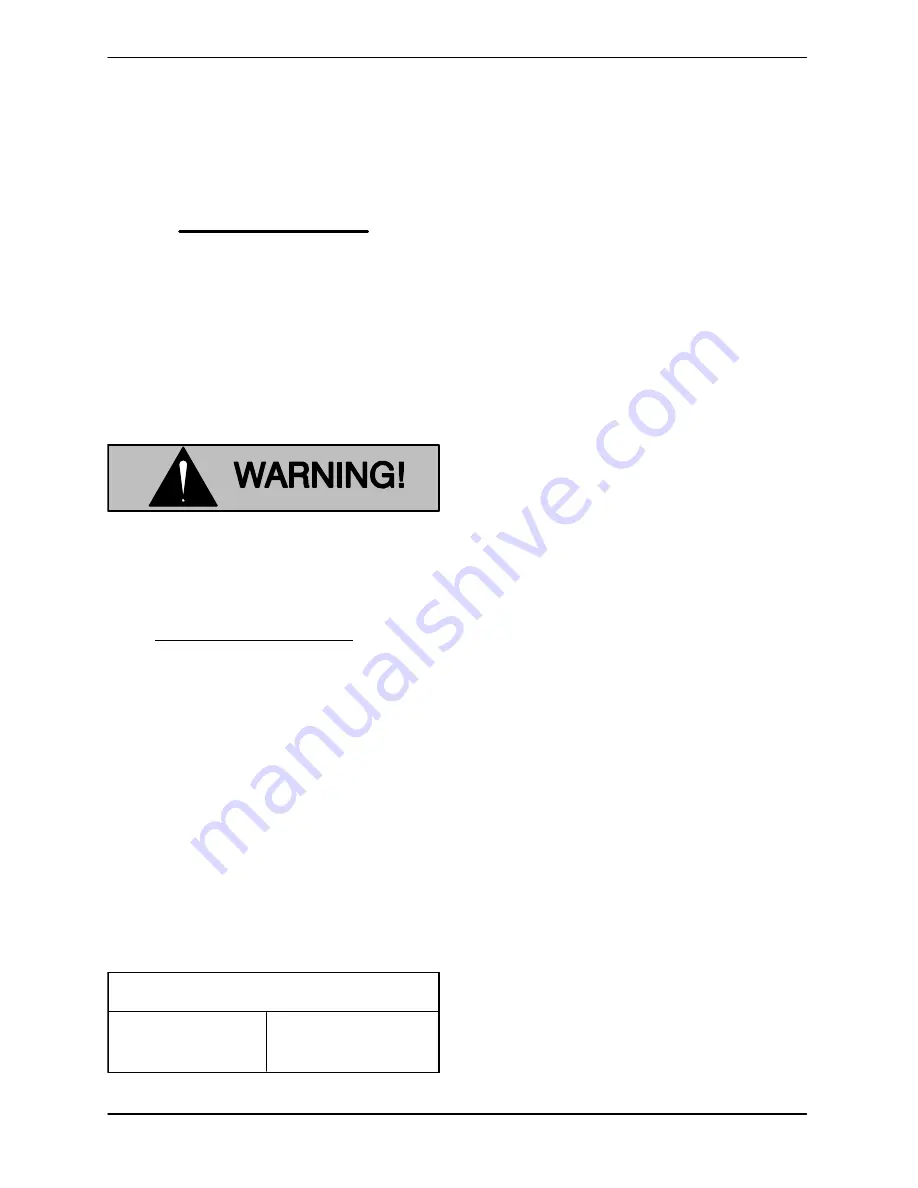
GHC SERIES
OM-05845
PAGE B-3
INSTALLATION
NOTE
Simple flushing of the wetted end of the pump to re
move test liquid may not be sufficient to thoroughly
clean the seal cavity. Pump design and the particu
lar seal assembly being used may require draining
the seal area by removing the backhead plug and
then flushing through a separate line.
To flush the pump, use an approved solvent com
patible with the liquid being pumped.
Make cer
tain that the solvent will not attack pump com
ponents, particularly seals and gaskets.
PUMP INSTALLATION
Pump dimensions are shown in the separate
Pump Specification Bulletin.
Never operate the pump without a pres
sure relief valve installed on the pump
or in the discharge piping. Make certain
that pump‐mounted pressure relief
valves are installed with their adjusting
ends toward the suction port. If bi‐rota
tional operation is required, a pressure
relief device must be provided for both
directions of flow. Operation without a
pressure relief valve or with an improp
erly installed relief valve could cause
the pump to explode, resulting in seri
ous injury or death to personnel.
Maximum Operating Parameters
Rotary gear pumps are capable of different operat
ing parameters depending on such things a specif
ic materials of construction, pump options, liquid
being pumped, etc.
In
no
case
should the applica
tion exceed the parameters shown below. Consult
the factory for specific ratings.
Maximum Operating Parameters
Pressure
400 psi (28 Bar)
Speed*
1750 rpm
Temperature
350
F (177
C)
* Consult Factory for Specific Speed Rating
Lifting
Remove suction and discharge hose and piping
before attempting to lift the pump. Use lifting equip
ment with a capacity of at least five times the total
weight of the equipment being lifted.
Positioning The Pump
Locate the pump as close as possible to the liquid
being pumped. Locating the pump below the liq
uid source will help self‐priming and reduce the
possibility of cavitation.
Mounting
The pump may be shipped alone, mounted on a
base, or with pump and motor mounted on a base.
Install the pump and motor on a base before
mounting the base on a foundation.
Mount the base on a foundation that will provide
permanent, rigid support for the pump, and will be
heavy enough to absorb any vibration, strain or
shock.
Piping
Before establishing suction and discharge lines,
determine pump port positions and rotation. Fig
ure B-1 shows typical port positions for the stan
dard 180
housing; if you have selected a 90
housing port option, your port positions will be dif
ferent.
Either hose or rigid pipe may be used to make con
nections. If rigid piping is used, install expansion
joints to protect the pump from vibration and ther
mal expansion in the piping. Do not use expansion
joints or flexible connectors to adjust misaligned
piping.
Begin piping layout at the pump, and work toward
the source of supply and the point of discharge. If
an obstacle is in the way of a suction or discharge
line, run the piping around the obstruction, not
over it. Running piping over an obstruction will
creat an air pocket which will make priming more
difficult.
If possible, slope the piping toward the pump so no
air or liquid is trapped in the piping. If a long hori
zontal suction line is necessary, install the line be
low the liquid level whenever possible in order to