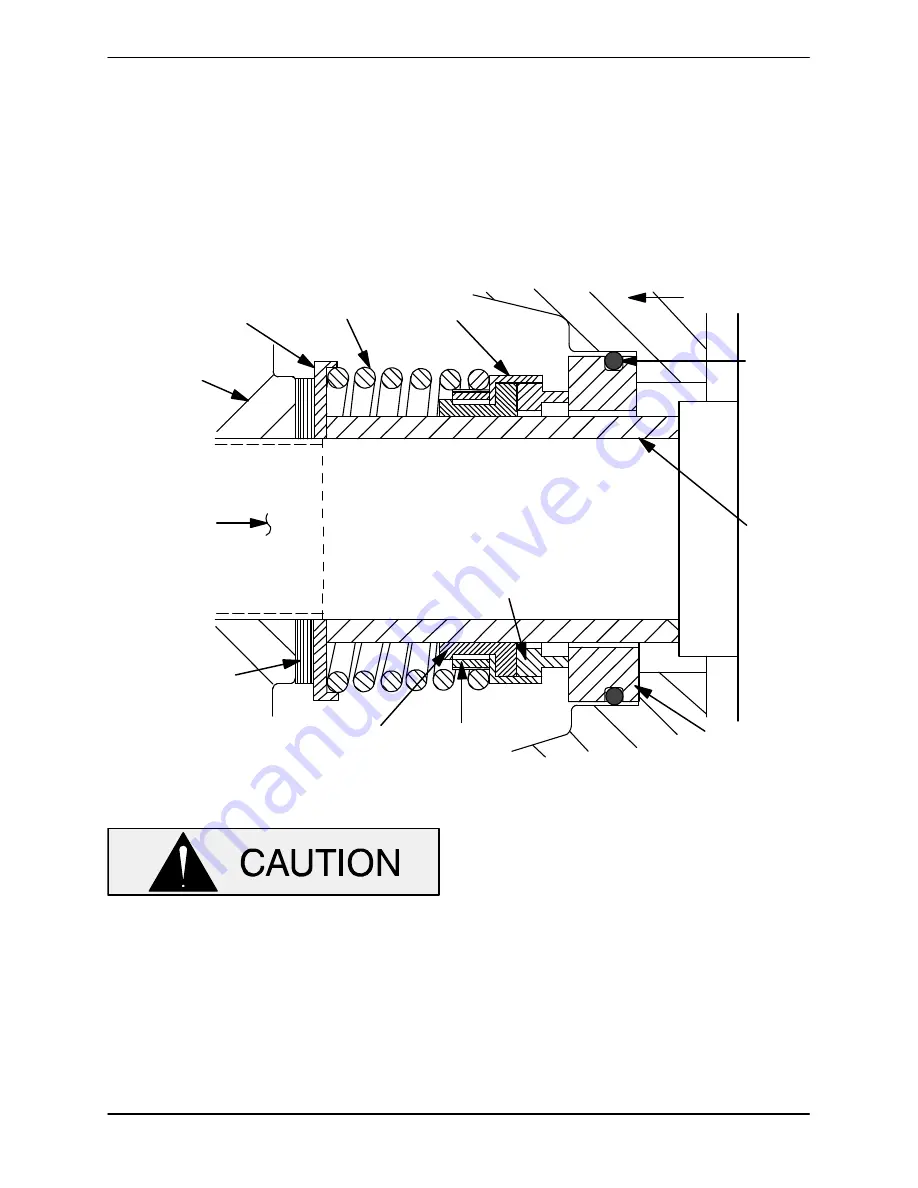
80 SERIES
OM−06362
MAINTENANCE & REPAIR
PAGE E − 8
finished faces; even fingerprints on the faces can
shorten seal life. If necessary, clean the faces with a
non-oil based solvent and a clean, lint-free tissue.
Wipe
lightly
in a concentric pattern to avoid
scratching the faces.
Inspect the seal components for wear, scoring,
grooves, and other damage that might cause leak-
age. If any components are worn, replace the com-
plete seal;
never mix old and new seal parts
.
If a replacement seal is being used, remove it from
the container and inspect the precision finished
faces to ensure that they are free of any foreign
matter.
To ease installation of the seal, lubricate the bel-
lows and O-rings with water or a very
small
amount of light lubricating oil, and apply a drop of
light lubricating oil on the finished faces. Assemble
the seal as follows, (see Figure 3).
INTERMEDIATE
O-RING
ENGINE
STATIONARY
ELEMENT
ROTATING
BELLOWS
IMPELLER
SHIMS
IMPELLER
SPRING
RETAINER
ELEMENT
CRANKSHAFT
SEAL
SLEEVE
SPRING CENTERING
WASHER
DRIVE BAND
Figure 3. Seal Assembly
This seal is not designed for operation at
temperatures above 160
_
F (71
_
C). How-
ever most petroleum products such as
gasoline are more efficiently handled at
ambient temperatures. Do not use at high-
er operating temperatures.
If the intermediate was removed, lay it on a flat sur-
face with the impeller side facing up.
Subassemble the O-ring onto the stationary seat
and press this subassembly into the intermediate
bore until it seats squarely against the shoulder.
Slide the assembled intermediate and stationary
seat over the shaft and secure the intermediate to
the engine with the hardware (9 and 10). When in-
stalling the intermediate, use caution not to dam-
age the stationary seat on the shaft threads.
NOTE
If the intermediate was not separated from the en-
gine during disassembly, subassemble the O-ring
into the stationary seat and use a piece of plastic
pipe to press the seat into the intermediate bore un-