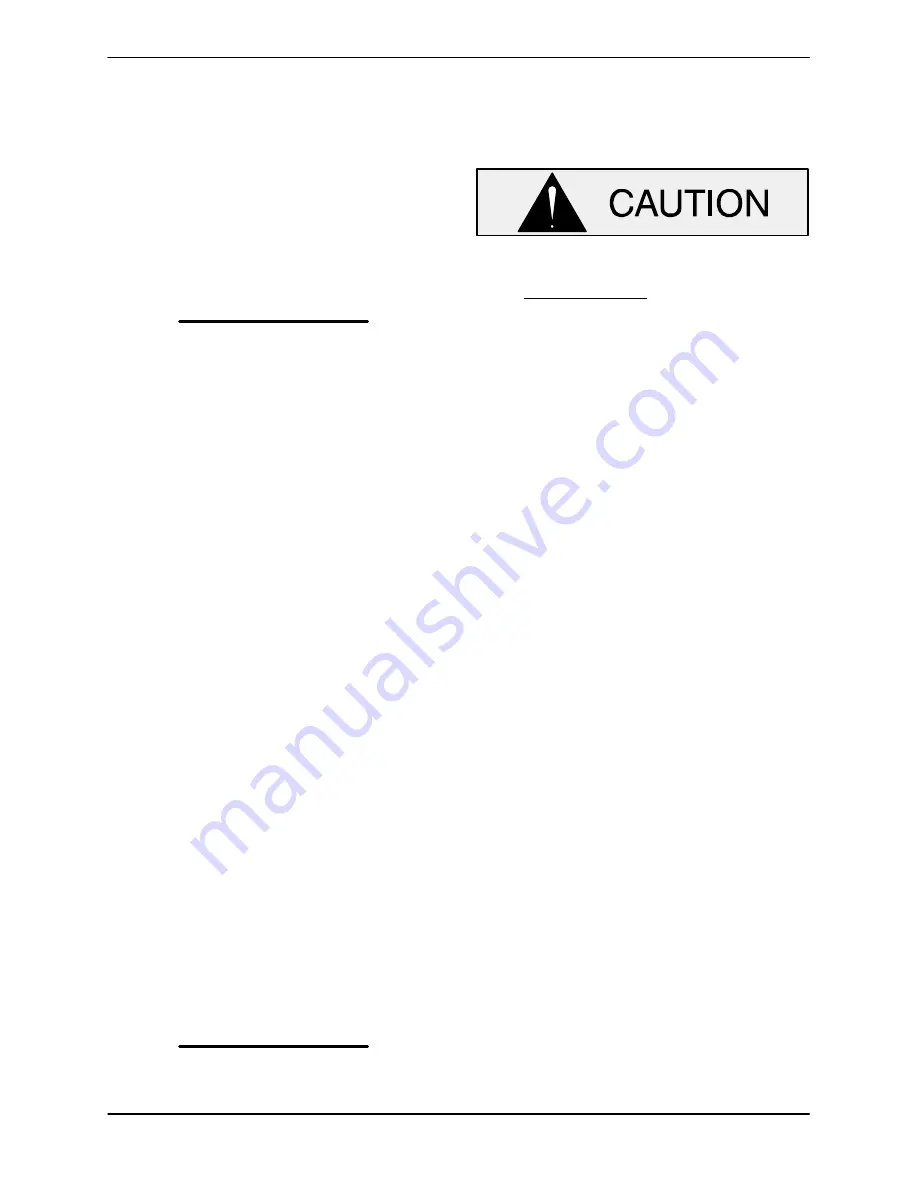
PA SERIES PUMPS
MR−05740
MAINTENANCE & REPAIR
PAGE C − 18
to the shaft, making future removal difficult
or impossible without damage to the im-
peller or shaft.
Install the same thickness of impeller adjusting
shims (29) as previously removed and screw the
impeller assembly onto the shaft until tight.
NOTE
At the slightest sign of binding,
immediately
back
the impeller off, and check the threads for dirt.
Do
not
try to force the impeller onto the shaft
.
A clearance of .025 to .040 inch (0,64 to 1,02 mm)
between the impeller and the seal plate is neces-
sary for maximum pump efficiency. Measure this
clearance, and add or remove impeller adjusting
shims as required.
Secure the impeller to the shaft with the impeller
washer and capscrew (21 and 22).
Pump Casing Installation
(Figure C−4)
Lubricate the rotating assembly O-rings (34 and
35, Figure C−5) with a light coating of grease. Use
a suitable hoist and sling to slide the pump casing
(1) over the rotating assembly.
Install 0.120 inch (3 mm) of shims (11) at each
mounting location and secure the casing to the ro-
tating assembly (2) with the hardware (9 and 10).
Drive Assembly Installation (Engine Driven
Units Only)
(Figure C−6)
Install the shaft key in the shaft keyway. Position
the flexible portion of the coupling assembly (1) on
the shaft as shown in Figure C−6.
NOTE
The flexible portion of the coupling must be proper-
ly positioned on the shaft. The heads of the caps-
crews in the center of the coupling
must be posi-
tioned away from the pump end of the shaft
.
Align the keyway in the bushing (2) with the shaft
key, and slide it onto the shaft to the dimension
shown in Figure C−6. Rotate the flexible portion of
the coupling until the tapped holes for the two set-
screws align with those in the bushing, and install
the setscrews.
Make certain that the flexible portion of the
coupling is mounted as shown in Figure
C−6.
This is critical.
If the coupling is not
properly positioned on the shaft, the
coupling parts may not fully engage, or a
pre-load condition can cause premature
bearing failure.
The coupling must be positioned 1.44
inches (37 mm) from the end of the shaft.
This will allow the two portions of the cou-
pling to fully engage when the drive flange
is secured to the engine bellhousing, with-
out pre-loading the bearings.
With the flexible portion of the coupling and the
bushing properly positioned on the shaft, tighten
the two setscrews in an alternating sequence until
the bushing and coupling are fully secured. Torque
the setscrews to 14.6 ft. lbs. (175 in. lbs. or 2 m.
kg.).
If the complete coupling assembly is being re-
placed, apply ‘Loctite Retaining Compound No.
242’ or equivalent to the threads of the hardware (6
and 7), and secure the outer ring of the coupling to
the engine flywheel by torquing the hardware to 45
ft. lbs. (540 in. lbs. or 6,2 m. kg.).
Securing Pump End to Power Source
(Engine Driven Units Only, Figure C−6)
Using a suitable lifting device, position the pump
end assembly and coupling so the flexible portion
of the coupling seats inside the outer ring attached
to the engine flywheel.
NOTE
To ease installation,
lightly
lubricate the rubber por-
tion of the coupling with a
non-petroleum based
lubricant
such as vegetable oil or glycerin, or a sili-
con-based lubricant such as WD40" or equivalent.
Do not
use petroleum-based lubricants, or any oth-