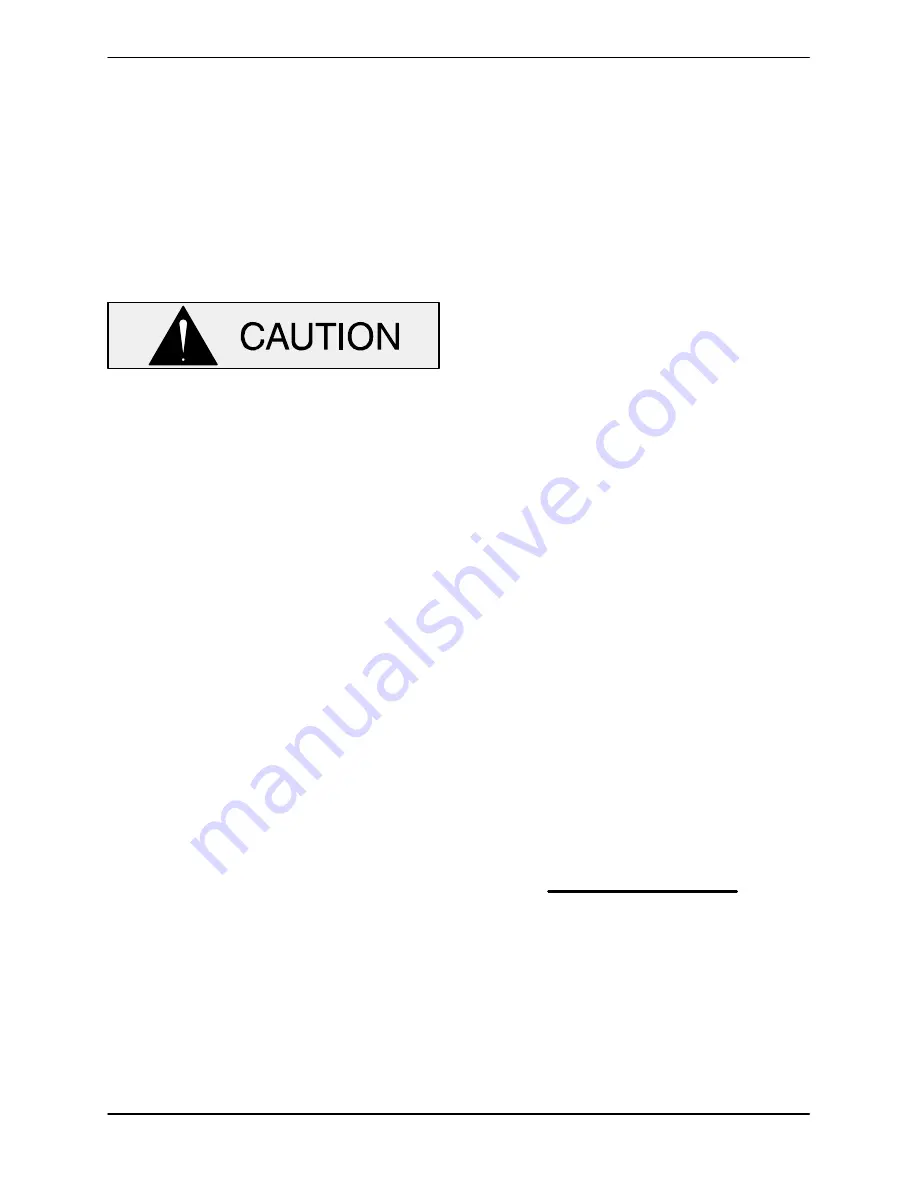
PA SERIES PUMPS
MR−05740
MAINTENANCE & REPAIR
PAGE C − 12
to prevent injuries to personnel or dam-
age to equipment. The bail is intended
for use in lifting the pump assembly
only. Suction and discharge hoses and
piping must be removed from the pump
before lifting. If chains or cables are
used to lift pump components, make
certain that they are positioned so as
not to damage the pump, and so that the
load will be balanced.
Use
only
replacement parts provided or
approved by Gorman-Rupp. Use of non-
authorized parts may result in damage to
the equipment and/or injury to personnel
and
will
invalidate the warranty.
Priming Chamber Removal And Disassembly
(Figure C−2)
Disconnect both the suction piping and the air dis-
charge tubing from the priming chamber assembly
(1). Support the priming chamber assembly using
a sling and a suitable lifting device. Remove the
hardware (6 and 7) and separate the priming
chamber assembly, gasket (8) and baffle (9) from
the pump assembly.
(Figure C−3)
Remove the hardware (3 and 4) securing the prim-
ing valve (1) to the priming chamber (6). Carefully
lift the valve components from the priming cham-
ber. Remove the gasket (7) and clean the mating
surfaces.
If the priming valve float is stuck or the strainer (5) is
clogged, it can usually be cleaned without further
disassembly.
The only serviceable part of the priming valve is the
orifice button (2). If liquid continues to bypass
through the priming chamber after adjusting the
orifice button (see
Priming Chamber Reassemb-
ly and Installation
for adjustment), the button may
require replacement. To replace the orifice button,
remove one of the e-clips" from the pivot pin clos-
est to the orifice button and remove the pivot pin.
This will allow the linkage to be raised high enough
to access the orifice button.
Remove the hex nut and lockwasher securing the
orifice button to the linkage bar and unscrew the
orifice button from the linkage bar.
Discharge Check Valve Removal and
Disassembly
(Figure C−1)
Support the discharge check valve assembly (2)
using a sling and a suitable lifting device. Remove
the hardware securing the discharge check valve
assembly and gasket to the pump assembly.
The flapper and cover O-ring are the only service-
able parts of the check valve. If the flapper requires
replacement, remove the hardware securing the
cover and O-ring. Separate the cover and remove
the flapper.
Back Cover Plate and Wear Plate Removal
(Figure C−4)
The wear plate (5) is easily accessible and may be
serviced by removing the back cover (15). Before
attempting to service the pump, remove the pump
casing drain plug (13) and drain the pump. Clean
and reinstall the drain plug.
Remove the hand knobs (19) and pry the back
cover and assembled wear plate from the pump
casing (1).
NOTE
An alternate method of removing the back cover
from the pump casing is to remove the hand knobs
(19) and two diagonally opposing locking collars
(17). Use the adjusting screws (16) to press the
back cover out of the pump casing.
Remove and discard the O-rings (6 and14).
Inspect the wear plate (5) and, if replacement is re-
quired, remove the hardware (3 and 4) securing it
to the back cover plate.
Separating Pump End From Power Source
Further disassembly of the pump requires separat-
ing the pump end from the power source. Discon-
nect the discharge piping from the pump casing.