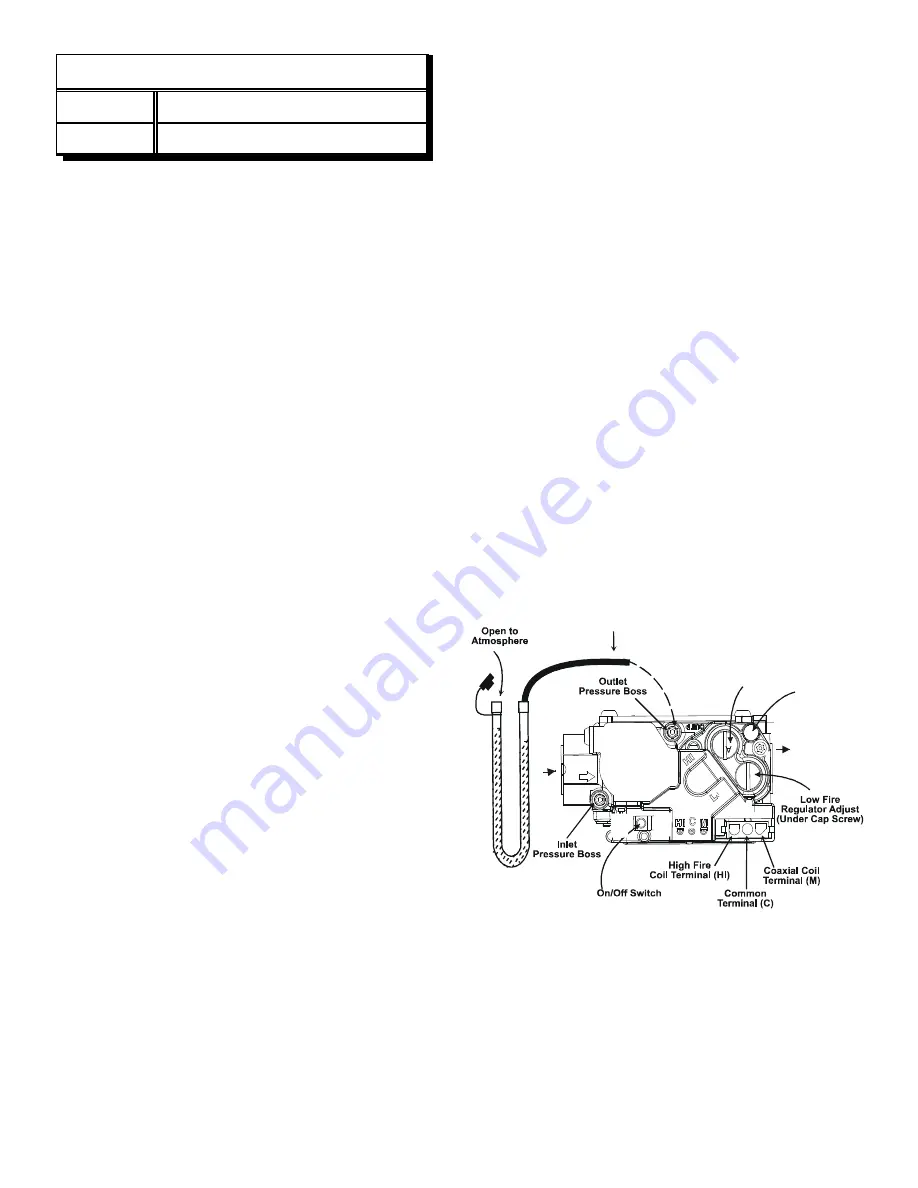
18
NATURAL
Min. 5.0" W.C., Max. 10.0" W.C.
PROPANE
Min. 11.0" W.C., Max. 13.0" W.C.
INLET GAS PRESSURE
notE
: I
nlEt
GaS
PRESSURE
MUSt
bE
WItHIn
lIMItS
SHoWn
abovE
.
If operating pressures differ from above, make necessary
pressure regulator adjustments, check piping size, etc.,
and/or consult with local utility.
M
anIfold
P
RESSURE
c
HEck
and
a
djUStMEnt
The gas valve has a pressure tap to facilitate measurement
of the manifold pressure. The manifold pressure must be
measured with the burners operating.
1.
With disconnect switch open, remove field connected
thermostat wire from terminal R, W1 and W2 on TB1.
Place jumper wire between R, W1 and W2 to engage
high stage heat.
2. See Figure in gas input check section for gas valve
adjustment.
To adjust the pressure regulator, remove the adjustment
screw cover on the gas valve. Turn the adustment screw
out (counterclockwise) to decrease pressure, turn in
(clockwise) to increase pressure. Only small variations
in gas flow should be made by means of the pressure
regulator adjustment. Any major changes in flow should
be made by changing the size of the burner orifices. The
measured input rate to the furnace must not exceed the
rating specified on the unit rating plate.
For natural gas, the high stage manifold pressure must be
between 3.2 and 3.8 inches water column (3.5 nom inal).
Low stage manifold pressure must be between 1.7 to 2.3
inches water column (2.0 nominal).
3.
To set low fire rate, open disconnect switch and
remove jumper from R to W2. To set low fire manifold
pressure, repeat steps above. Refer to Figure in gas
input check section for location of high and low stage
pressure adjustment.
For propane gas, the manifold pressure must be between
9.7 and 10.3 inches water column (10.0 nominal). Low
stage manifold must be between 5.7 and 6.3 inches water
column (6.0 nominal).
G
aS
I
nPUt
(n
atURal
G
aS
o
nly
) c
HEck
It is the responsibility of the contractor to adjust the gas
input to the unit.
To measure the gas input use a gas meter and proceed as
follows:
1. Turn off gas supply to all other appliances except the
unit.
2. With the unit operating, time the smallest dial on the
meter for one complete revolution. If this is a 2 cubic
foot dial, divide the seconds by 2; if it is a 1 cubic foot
dial, use the seconds as is. This gives the seconds
per cubic foot of gas being delivered to the unit.
3. INPUT=GAS HTG VALUE x 3600 / SEC. PER CUBIC
FOOT
Example:
Natural gas with a heating value of 1000 BTU
per cubic foot and 34 seconds per cubic foot as determined
by Step 2, then:
Input = 1000 x 3600 / 34 = 106,000 BTU per Hour.
notE: btU
contEnt
of
tHE
GaS
SHoUld
bE
obtaInEd
fRoM
tHE
GaS
SUPPlIER
. t
HIS
MEaSUREd
InPUt
MUSt
not
bE
GREatER
tHan
SHoWn
on
tHE
UnIt
RatInG
PlatE
.
Adjust input rate by varying the adjustment of the gas
pressure regulator on the gas valve. All adjustments
must be made with furnace operating at high fire and at
normal operating temperature. A manometer should be
connected to the gas valve to verify pressure is within
the specified range (see following figures for manometer
connections). Clockwise rotation of the pressure regulator
screw increases pressure and gas flow rate. Turn screw
counterclockwise to decrease pressure and gas flow rate.
After adjustment the furnace temperature rise must be
within the range specified on the unit data plate.
notE: t
HERMal
EffIcIEncy
of
tHE
fURnacE
IS
a
PRodUct
EffIcIEncy
RatInG
dEtERMInEd
UndER
contInUoUS
oPERatInG
condItIonS
IndEPEndEnt
of
any
InStallEd
SyStEM
.
Ma
n
o
meter
Ma
n
o
meter
Hos
e
High Fire Regulator
Adjust
(Under Cap Screw) Regulator
Vent
Gas Flow
O
N
O
FF
WHItE
-
RodGERS
(2-S
taGE
)
GaS
contRol
valvE
connEctEd
to
ManoMEtER
PRESSURE
adjUStMEntS
To connect manometer to gas valve:
1. Back outlet pressure tap screw (inside inlet pressure
boss) out one turn (counterclockwise, not more than
one turn).
2. Attach a hose and manometer to the outlet pressure
boss of the valve.