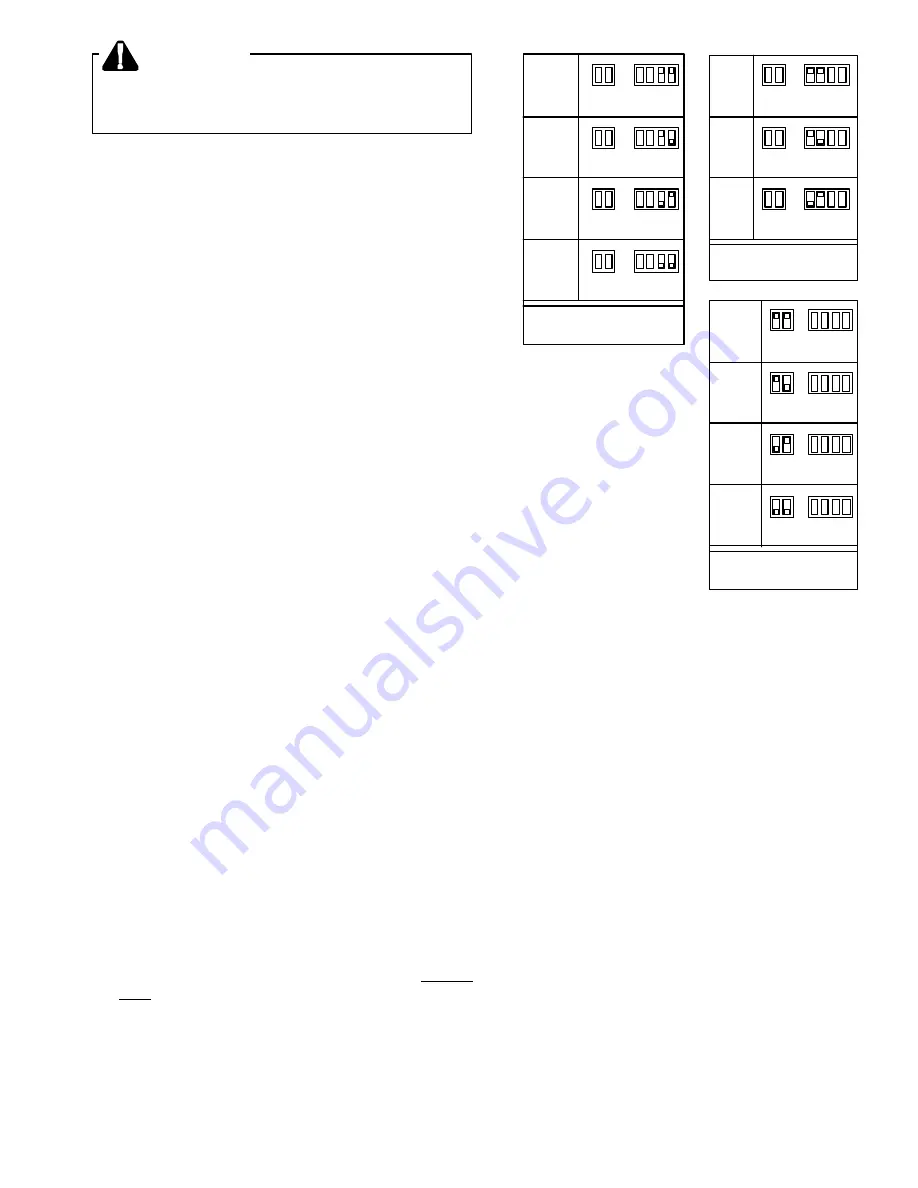
IO-231
6/03
17
All furnaces are shipped with heating speed set at “B” and
cooling speed set at “D”. Use the following procedure to
select the heating and cooling speed needed for your unit.
Use the CFM LED (green), adjacent to the integrated con-
trol module fuse to verify airflow quantity. The green CFM
LED blinks once for each 100 CFM of airflow.
1. Determine the tonnage of the cooling system installed
with the furnace. If the cooling capacity isin BTU/hr di-
vide it by 12,000 to convert capacity to TONs.
Example:
Cooling Capacity of 30,000 BTU/hr.
30,000/12,000 = 2.5 Tons
2. Determine the proper air flow for the cooling system.
Most cooling systems are designed to work with air
flows between 350 and 450 CFM per ton.
Most manufacturers recommend an air flow of about
400 CFM per ton.
Example:
2.5 tons X 400 CFM per ton = 1000 CFM
The cooling system manufacturer’s instructions must be
checked for required air flow. Any electronic air cleaners
or other devices may require specific air flows, consult in-
stallation instructions of those devices for requirements.
3. Knowing the furnace model, locate the high stage cool-
ing air flow data in the following airflow tables. Look up
the cooling air flow determined in step 2 and find the
required cooling speed and adjustment setting.
Example:
A GMNTE080-4 furnace installed with a
2.5 ton air conditioning system. The air flow needed is
1000 CFM. Looking at the cooling speed chart for
GMNTE080-4, find the air flow closest to 1000 CFM. A
cooling airflow of 990 CFM can be attained by setting
the cooling speed to “C” and the adjustment to “-” (mi-
nus).
NOTE:
Continuous Fan Speed will be 38% of high stage
cooling.
4. Locate the blower speed selection DIP switches on
the integrated control module. Select the desired “cool-
ing” speed tap by positioning switches 1 and 2 appro-
priately. Select the desired “adjust” tap by positioning
switches 3 and 4 appropriately. Refer to the following
figure for switch positions and their corresponding taps.
Turn off power to furnace for a minimum of 10 sec-
onds, allowing motor to reset and recognize new speed
selection. Turn on power to furnace and place the unit
into cooling mode. Allow blower to ramp up to full speed.
Verify CFM by counting the number of times the green
CFM LED blinks.
O
F
F
O
F
F
8 7
4 3 2 1
O
F
F
O
N
8 7
4 3 2 1
O
N
O
F
F
8 7
4 3 2 1
O
N
O
N
8 7
4 3 2 1
Cooling
Speed
Tap A
Cooling
Speed
Tap B
Cooling
Speed
Tap C
Cooling
Speed
Tap D
*
Cooling Speed Taps
(
*
indicates factory setting)
O
F
F
O
F
F
8 7
4 3 2 1
O
F
F
O
N
8 7
4 3 2 1
O
N
O
F
F
8 7
4 3 2 1
O
N
O
N
8 7
4 3 2 1
Heating
Speed
Tap A
Heating
Speed
Tap B
Heating
Speed
Tap C
Heating
Speed
Tap D
Heating Speed Taps
(
*
indicates factory setting)
*
O
F
F
O
F
F
8 7
4 3 2 1
O
F
F
O
N
8 7
4 3 2 1
O
N
O
F
F
8 7
4 3 2 1
Normal
+ (Plus)
Adjust
- (Minus)
Adjust
Adjust Taps
(
*
indicates factory setting)
*
5. Select the heating speed from the heating speed chart
in the specification sheet for your model. The adjust
setting (already established by the cooling speed se-
lection) determines which set of speeds are available.
The selected speed must provide a temperature rise
within the rise range listed with the particular model.
Example:
The GMNTE080-4 is set for 990
CFM on
cooling, the “ADJUST” is set to “-” (minus). The four
heating speeds available are “A Minus”, “B Minus”, “C
Minus”, and “D Minus”. “A Minus” has a rise of 63
°
F
for both stages which is within the 35-65°F rise range
for the GMNTE080-4. This setting will keep electrical
consumption to a minimum. Set the “Heat” speed DIP
switches to “A”.
6. Select the desired “heating” speed tap by positioning
switches 7 and 8 appropriately. Refer to figure above.
Turn off power to furnace for a minimum of 10 sec-
onds, allowing motor to reset and recognize new speed
selection. Turn on power to furnace and place the unit
into heating mode. Allow blower to ramp up to full
speed. Verify selected CFM by counting the green
CFM LED blinks.
WARNING
TO AVOID DEATH OR PERSONAL INJURY DUE TO ELEC-
TRICAL SHOCK, TURN OFF POWER TO THE FURNACE
BEFORE CHANGING SPEED TAPS.