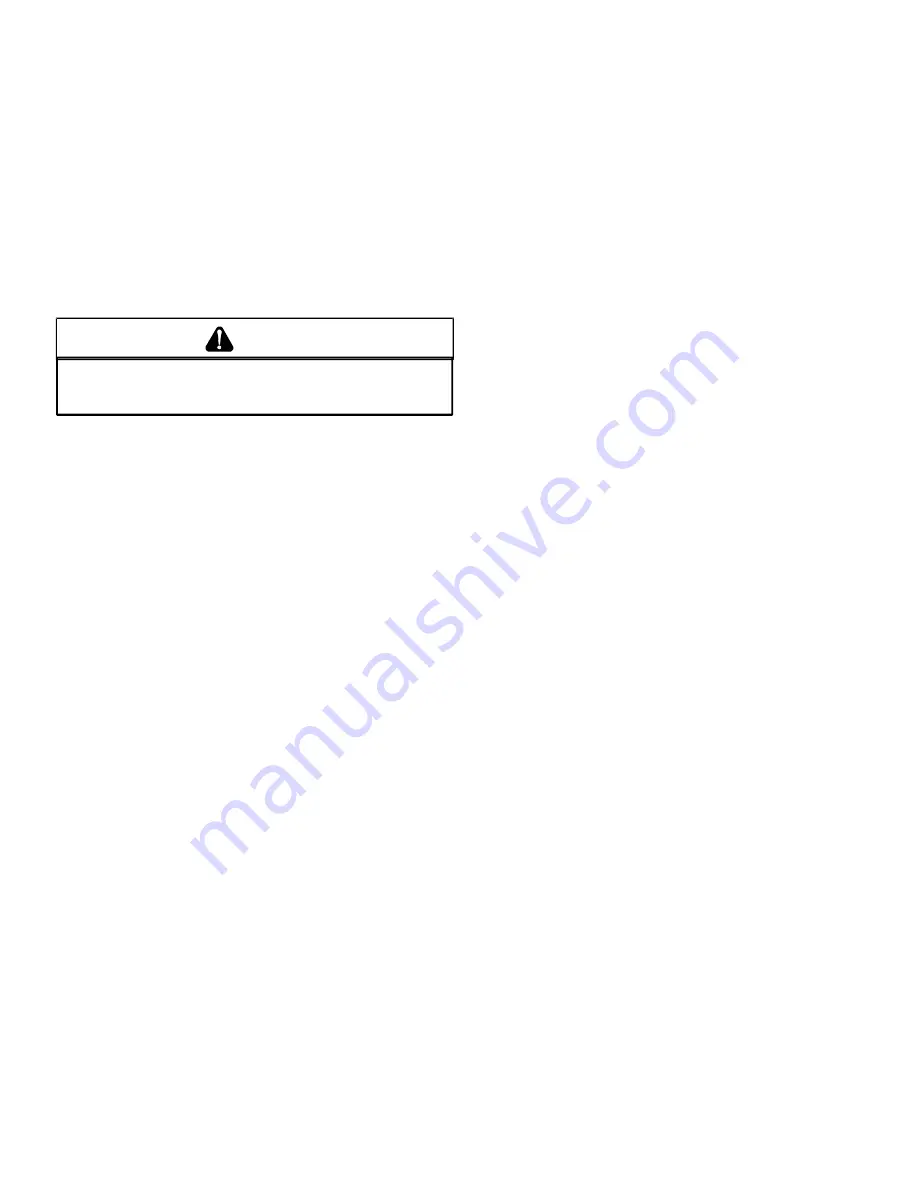
4
NOTE:
When inspecting the unit for transportation damage,
remove all packaging materials. Recycle or dispose of the
packaging material according to local codes.
P
RE
-I
NSTALLATION
C
HECKS
Carefully read all instructions for the installation prior to in-
stalling unit. Ensure each step or procedure is understood
and any special considerations are taken into account be-
fore starting installation. Assemble all tools, hardware and
supplies needed to complete the installation. Some items may
need to be purchased locally.
UNIT LOCATION
T
O
PREVENT
POSSIBLE
EQUIPMENT
DAMAGE
,
PROPERTY
DAMAGE
,
PERSONAL
INJURY
OR
DEATH
,
THE
FOLLOWING
BULLET
POINTS
MUST
BE
OBSERVED
WHEN
INSTALLING
THE
UNIT
.
WARNING
IMPORTANT NOTE:
Remove wood shipping rails prior to
installation of the unit.
A
LL
I
NSTALLATIONS
:
IMPORTANT NOTE:
If a crankcase heater is used, the unit
should be energized 24 hours prior to compressor start up to
ensure crankcase heater has sufficiently warmed the compres-
sor. Compressor damage may occur if this step is not followed.
NOTE:
Appliance is shipped from factory for vertical duct
application.
Proper installation of the unit ensures trouble-free operation.
Improper installation can result in problems ranging from
noisy operation to property or equipment damages, danger-
ous conditions that could result in injury or personal property
damage and could void the warranty. Give this booklet to the
user and explain it’s provisions. The user should retain these
instructions for future reference.
•
For proper operation and condensate drainage, the
unit must be mounted level.
•
Do not locate the unit in an area where the outdoor
air will be frequently contaminated by compounds
containing chlorine or fluorine. Common sources of
such compounds include swimming pool chemicals
and chlorine bleaches, paint stripper, adhesives,
paints, varnishes, sealers, waxes (which are not yet
dried) and solvents used during construction and
remodeling. Various commercial and industrial
processes may also be sources of chlorine/fluorine
compounds.
•
To avoid possible illness or death of the building
occupants, do NOT locate outside air intake device
(economizer, manual fresh air intake, motorized fresh
air intake) too close to an exhaust outlet, gas vent
termination, or plumbing vent outlet. For specific
distances required, consult local codes.
•
Allow minimum clearances from the enclosure for fire
protection, proper operation, and service access (see
Unit Clearances). These clearances must be
permanently maintained.
•
When the unit is heating, the temperature of the return
air entering the unit must be between 50°F and 100°F.
G
ROUND
L
EVEL
I
NSTALLATIONS
O
NLY
:
•
When the unit is installed on the ground adjacent to
the building, a level concrete (or equal) base is
recommended. Prepare a base that is 3” larger than
the package unit footprint and a minimum of 3” thick.
•
The base should also be located where no runoff of
water from higher ground can collect in the unit.
R
OOF
TOP
I
NSTALLATIONS
O
NLY
:
•
To avoid possible property damage or personal injury,
the roof must have sufficient structural strength to carry
the weight of the unit(s) and snow or water loads as
required by local codes. Consult a structural engineer
to determine the weight capabilities of the roof.
•
The unit may be installed directly on wood floors or
on Class A, Class B, or Class C roof covering material.
•
To avoid possible personal injury, a safe, flat surface
for service personnel should be provided.
•
Adequate clearances from the unit to any adjacent
public walkways, adjacent buildings, building openings
or openable windows must be maintained in
accordance with National Codes.
U
NIT
P
RECAUTIONS
•
Do not stand or walk on the unit.
•
Do not drill holes anywhere in panels or in the base
frame of the unit. Unit access panels provide
structural support.
•
Do not remove any access panels until unit has been
installed on roof curb or field supplied structure.
•
Do not roll unit across finished roof without prior
approval of owner or architect.
•
Do not skid or slide on any surface as this may
damage unit base. The unit must be stored on a
flat, level surface. Protect the condenser coil
because it is easily damaged.
R
OOF
C
URB
I
NSTALLATIONS
O
NLY
:
Curb installations must comply with local codes and should
be done in accordance with the established guidelines of the
National Roofing Contractors Association.
Proper unit installation requires that the roof curb be firmly
and permanently attached to the roof structure. Check for
adequate fastening method prior to setting the unit on the
curb.