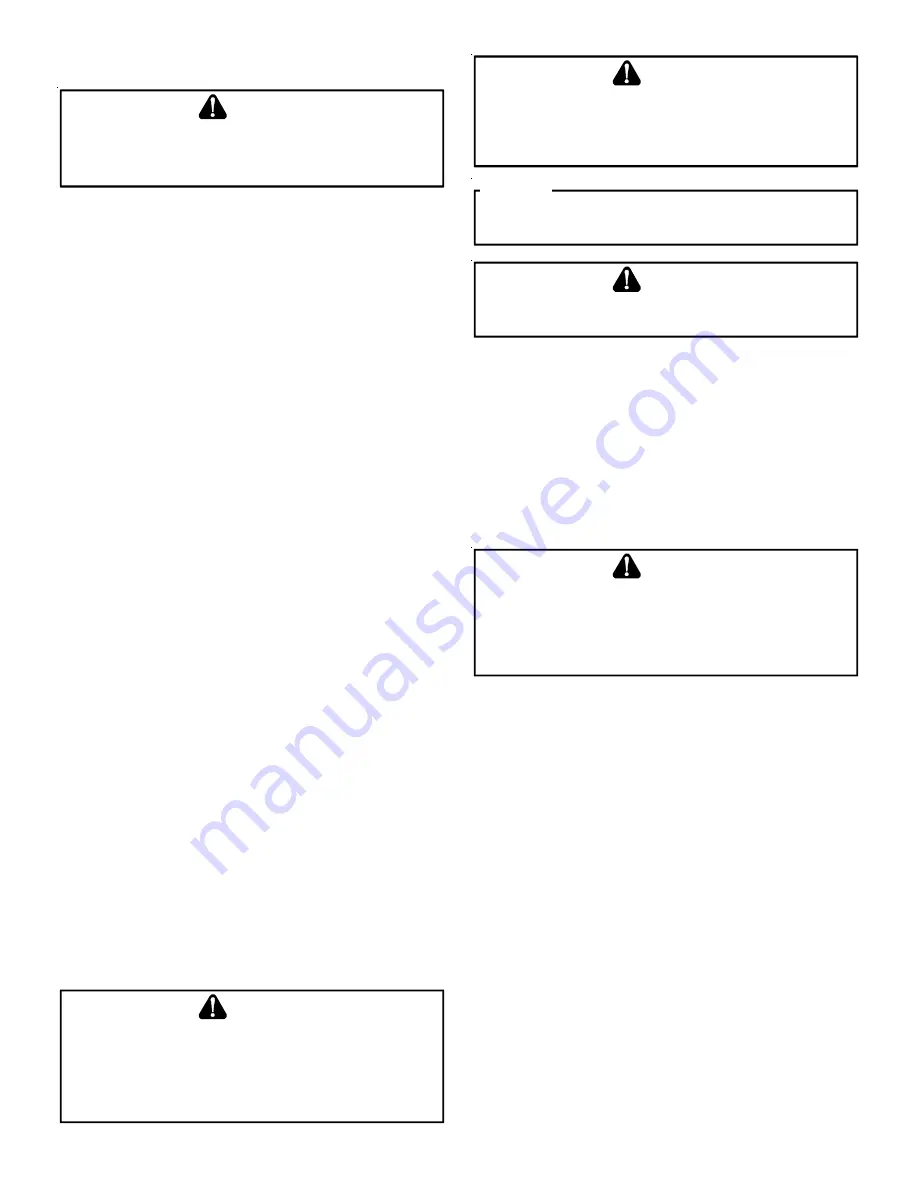
8
S
YSTEM
S
TART
U
P
POSSIBLE
REFRIGERANT
LEAK!
T
O
AVOID
A
POSSIBLE
REFRIGERANT
LEAK
,
OPEN
THE
SERVICE
VALVES
UNTIL
THE
TOP
OF
THE
STEM
IS
1/8”
FROM
THE
RETAINER
.
CAUTION
NOTE:
Power must be supplied to the 18 SEER outdoor units
containing ECM motors before the power is applied to the
indoor unit. Sending a low voltage signal without high voltage
power present at the outdoor unit can cause malfunction of
the control module on the ECM motor.
Adequate refrigerant charge for a matching evaporator and
15 feet lineset is supplied with the condensing unit. If line set
exceeds 15 feet in length, refrigerant should be added at .6
ounces per foot of liquid line.
Open the suction service valve first! If the liquid service valve
is opened first, oil from the compressor may be drawn into
the indoor coil TXV, restricting refrigerant flow and affecting
operation of the system.
When opening valves with retainers, open each valve only until
the top of the stem is 1/8” from the retainer. To avoid loss of
refrigerant, DO NOT apply pressure to the retainer. When open-
ing valves without a retainer remove service valve cap and in-
sert a hex wrench into the valve stem and back out the stem
by turning the hex wrench counterclockwise. Open the valve
until it contacts the rolled lip of the valve body.
NOTE:
These are not back-seating valves. It is not necessary
to force the stem tightly against the rolled lip.
After the refrigerant charge has bled into the system, open the
liquid service valve. The service valve cap is the secondary seal
for the valve and must be properly tightened to prevent leaks.
Make sure cap is clean and apply refrigerant oil to threads and
sealing surface on inside of cap. Tighten cap finger-tight and
then tighten additional 1/6 of a turn (1 wrench flat) to properly
seat the sealing surfaces.
Do not introduce liquid refrigerant from the cylinder into
the crankcase of the compressor as this may damage
the compressor.
1. Break vacuum by fully opening liquid and suction base
valves.
2. Set thermostat to call for cooling. Check indoor and
outdoor fan operation and allow system to stabilize for
10 minutes for fixed orifices and 20 minutes for expansion
valves.
C
HARGE
V
ERIFICATION
REFRIGERANT
UNDER
PRESSURE!
•
D
O
NOT
OVERCHARGE
SYSTEM
WITH
REFRIGERANT
.
•
D
O
NOT
OPERATE
UNIT
IN
A
VACUUM
OR
AT
NEGATIVE
PRESSURE
.
F
AILURE
TO
FOLLOW
PROPER
PROCEDURES
MAY
CAUSE
PROPERTY
DAMAGE
,
PERSONAL
INJURY
OR
DEATH
.
WARNING
U
SE
REFRIGERANT
CERTIFIED
TO
AHRI
STANDARDS
.
U
SED
REFRIGERANT
MAY
CAUSE
COMPRESSOR
DAMAGE
,
AND
IS
NOT
COVERED
UNDER
THE
WARRANTY
.
M
OST
PORTABLE
MACHINES
CANNOT
CLEAN
USED
REFRIGERANT
TO
MEET
AHRI
STANDARDS
.
CAUTION
V
IOLATION
OF
EPA
REGULATIONS
MAY
RESULT
IN
FINES
OR
OTHER
PENALTIES
.
NOTICE
O
PERATING
THE
COMPRESSOR
WITH
THE
SUCTION
VALVE
CLOSED
MAY
CAUSE
SERIOUS
COMPRESSOR
DAMAGE
.
CAUTION
F
INAL
C
HARGE
A
DJUSTMENT
The outdoor temperature must be 60°F or higher. Set the room
thermostat to COOL, fan switch to AUTO, and set the tem-
perature control well below room temperature.
After system has stabilized per startup instructions, check
subcooling and superheat as detailed in the following sec-
tion.
E
XPANSION
V
ALVE
S
YSTEM
T
O
PREVENT
PERSONAL
INJURY
,
CAREFULLY
CONNECT
AND
DISCONNECT
MANIFOLD
GAUGE
HOSES
.
E
SCAPING
LIQUID
REFRIGERANT
CAN
CAUSE
BURNS
.
D
O
NOT
VENT
REFRIGERANT
INTO
THE
ATMOSPHERE
.
R
ECOVER
ALL
REFRIGERANT
DURING
SYSTEM
REPAIR
AND
BEFORE
FINAL
UNIT
DISPOSAL
.
CAUTION
NOTE:
AVPTC air handlers have a non-adjustable TXV. Charge
unit match with this air handler by subcooling only.
Run the remote on low stage cooling for 10 minutes until refrig-
erant pressures stabilize. Use the following guidelines and
methods to check unit operation and ensure that the refriger-
ant charge is within limits. Charge the unit on low stage.
1. Purge gauge lines. Connect service gauge manifold to
base-valve service ports. Run system at least 10 minutes
to allow pressure to stabilize.
2. For best results, temporarily install a thermometer on
the liquid line at the liquid line service valve and 4-6"
from the compressor on the suction line. Ensure the
thermometer makes adequate contact and is insulated
for best possible readings. Use liquid line temperature
to determine sub-cooling and vapor temperature to
determine superheat.
NOTE: An optional method is to locate the thermometer
at the suction line service valve. Ensure the thermometer
makes adequate contact and is insulated for best
possible readings.