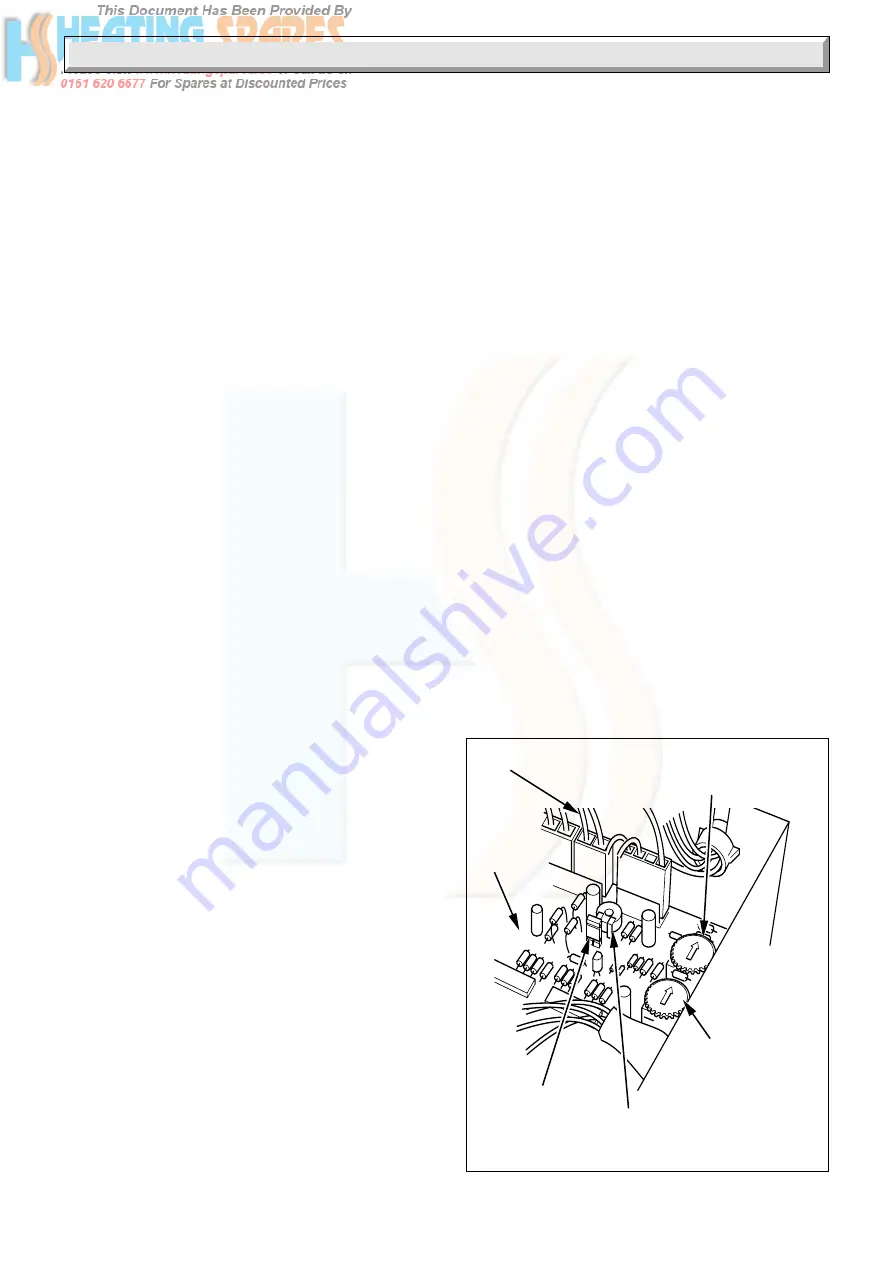
Supplied By www.heating spares.co Tel. 0161 620 6677
24
221474C
11 Commissioning
6390
Diagram 11.3
CONTROL
BOARD
CENTRAL
HEATING
GAS PRESSURE
POTENTIOMETER
MINIMUM
PRESSURE
POTENTIOMETER
HOT WATER
GAS PRESSURE
POTENTIOMETER
FROM
C.V.I.
JUMPER
Fully open a hot water draw off tap.
Check that the burner pressure is 16.8mbar. If this is incorrect, it
may be adjusted by turning the hot water gas pressure potentiometer
with a insulated screwdriver (clockwise to increase pressure), see
diagram 11.3.
Check minimum pressure again.
If the maximum pressure is unobtainable, check that the gas supply
is of adequate size, refer to Section 1.7. Put right as necessary.
11.6 Domestic Water Flow Rate
Adjust the water throttle to obtain a flow rate of 12Litre a minute
(2.6gall/min), clockwise to increase, see diagram 11.4. This is
equal to 5.0 seconds to fill a 1Litre container, 2.8 seconds to fill a
1pint container.
Close the tap when adjustment is satisfactory.
The minimum water flow rate for operation of the boiler is 3.6Litre
a minute, (0.8gall/min), equal to 16.5 seconds to fill a 1Litre
container, 9.5 seconds for 1pint. If this flow rate cannot be achieved,
check that there is no blockage and that the supply pressure is
adequate.
Refer to Table 2.
Close the hot water draw off tap.
11.7 Burner Pressure - Heating
Check that all remote heating system controls, room thermostats,
time switches and the like are switched on/programmed and calling
for heat.
Set switch “C” to “ON”, white flash showing, see diagram 11.1.
The pump will circulate water through the boiler and the main burner
will light.
Check that the burner pressure, with the heating system cold and
temperature control knob at maximum, to prevent any modulation
of the gas pressure, is /-0.2mbar, of 8.0mbar. If the burner
pressure is incorrect, it may be adjusted to the correct setting by
turning the central heating gas pressure adjuster (potentiometer)
using an insulated screwdriver, see diagram 11.3. Turn the adjuster
slowly, always making adjustment by reducing below the required
pressure then increasing up to the required setting, turn clockwise
to increase.
Isolate the boiler from the electrical supply.
Remove the pressure gauge and replace the test point screws on
gas valve and combustion chamber, see diagrams 11.1 and 11.2.
Test for gas soundness around the burner pressure test points with
the main burner alight, using a suitable leak detection fluid.
Refit the cover of the control housing and refit the housing to the
boiler.
11.8 Temperature Settings
The domestic hot water outlet and central heating flow temperatures
are factory preset and sealed.
The nominal temperature setting for the Domestic Hot Water outlet
is 60
o
C (140
o
F) at a flow rate of 5Litre a minute (1.1gal/min).
The specific water rate is 16.8litre per minute based on a 30
o
C
temperature rise.
The nominal flow temperature setting for central heating is 80
o
C
(176
o
F), with the user central heating temperature control set to
maximum.
11.9 Heating System Commissioning
Check that all remote system controls and integral clock are calling
for heat.
Fully open radiator valves, flow control valve “A” and bypass valve
“B”, see diagram 4.2.
Set the heating system in operation and balance the radiators.
Adjust the flow control valve “A” to achieve the required system
differential temperature between the boiler flow and return.
Turn off all radiators, then adjust bypass valve “B” to achieve the
same temperature difference between the boiler flow and return.
Refer to Section 4.6 and diagram 4.1.
Allow the system to reach maximum temperature then switch off,
isolate the boiler from the electrical supply and drain the system
rapidly whilst hot, using the external drain tap at the lowest point of
the system.
Fill and vent the system as described previously in Section 11.2.
Add the inhibitor, if required, refer to Section 4.10.
Lower the pressure to the initial cold fill design pressure, using the
draining tap, close to the boiler, refer to Table 2 and 4 Section 4.11.
Set pointer on the pressure gauge to this pressure.
Lock or remove the handles from the spindles of flow control valve
“A” and bypass valve “B” to prevent unauthorised adjustment.