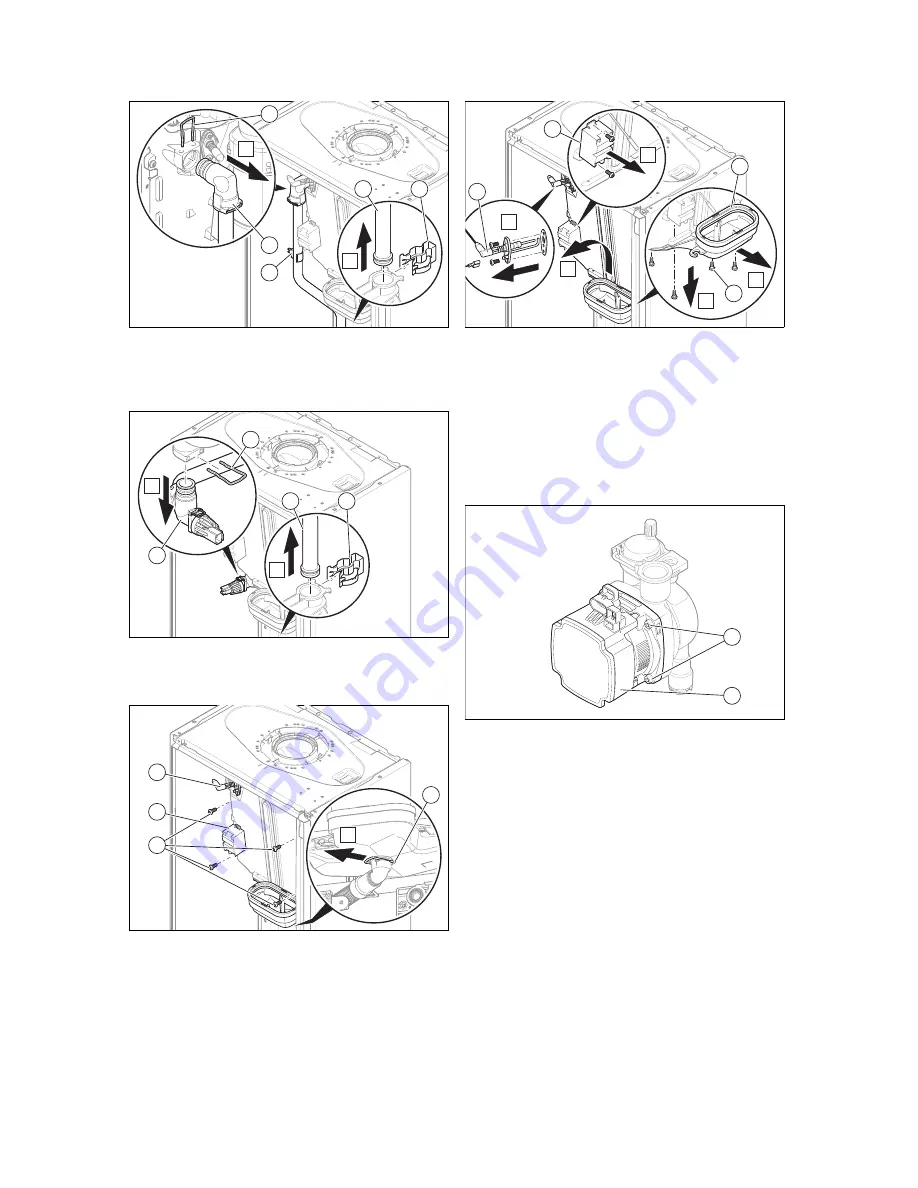
Troubleshooting 12
0020200967_00 SUSTAIN ..s Installation and maintenance instructions
25
1
2
3
5
4
A
B
4.
Remove the temperature sensor
(3)
.
5.
Remove the upper clip
(1)
.
6.
Remove the lower clip
(4)
.
7.
Remove the supply pipe
(5)
.
2
2
3
B
1
A
8.
Remove the upper clip
(1)
.
9.
Remove the lower clip
(3)
.
10. Remove the return pipe
(2)
.
1
A
2
3
4
11. Remove the clip underneath the condensate tray
(1)
.
12. Undo the four screws
(2)
.
1
3
2
4
A
C
B
D
E
13. Lift the heat exchanger up slightly and remove it to-
gether with the condensate tray
(1)
.
14. Undo the four screws
(3)
.
15. Remove the condensate tray.
16. Remove the ignition transformer
(2)
.
17. Use the bolts to secure the condensate tray to the new
heat exchanger.
18. Install the new heat exchanger in reverse order.
12.6.4 Replacing the pump head
1
2
1.
Disconnect the pump cable from the electronics box.
2.
Undo the four bolts
(1)
.
3.
Remove the pump head
(2)
.
4.
Replace the O-ring.
5.
Use four screws to secure the new pump head.
6.
Connect the pump cable to the electronics box.
12.6.5 Replacing the expansion vessel
1.
Drain the product. (
→
Page 23)
Содержание ENERGY 12s-A
Страница 47: ......