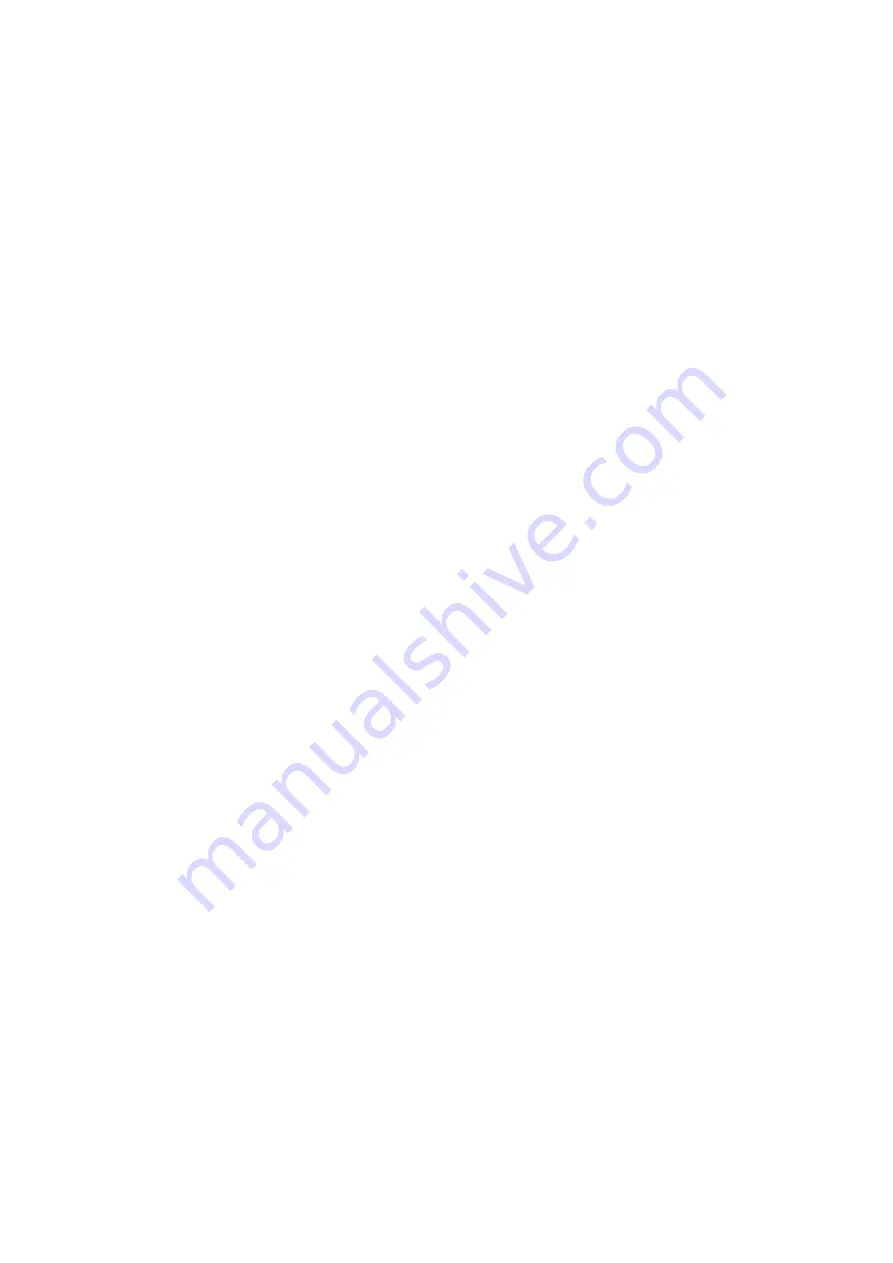
11.
CONTENTS OF PACKAGE
SUPPLIED
•
The following parts are supplied:
•
Boiler body -mounted, tested and complete with doors and
accessories
•
Jacket and insulation
•
Front
door
•
Control
panel
12.
INSTALLATION
(Fig. 4)
The boiler must be installed by a properly qualified person. It
must be installed in a room of a suitable size in compliance with
the relevant safety rules.
The plumbing system must ensure a minimum flow of water into
the boiler as shown in the specification. Figure 5 shows two
examples of plumbing system layout. If a sealed expansion tank
is used, a safety valve must be fitted. Always remember to
comply with any local rules on the safety of heating systems.
LEGEND
1 –Open expansion tank
2 –Pump
3 –One-way valve
4 -Re-circulation pump
5 –Return
6 –Delivery
7 –Heating shell
8 –Sealed expansion tank
9 –Filling valve
10 –Safety valve
13.
HOW TO INSTALL THE BOILER
The boiler is installed in separate stages:
1. Assembly of the jacket.
2. Plumbing connections and hydraulic test.
3. Installation of the control panel.
PRELIMINARIES
(Figs. 5-6-7)
a) Take the boiler, still on its pallet, near the place where it will
be installed;
b) Mount the four feet (40) with the four screws M8x35 (41) and
the four nuts M8 (42);
c) Screw in the four screws M12 (43);
d) Remove the boiler from the pallet;
e) Push the boiler to the place where you want to install it.
13.1 – JACKET ASSEMBLY
(Figs. 8-9-10-11-12)
1. Mount the brackets (22, 24) on the front element (21) and
lock them with flanged nuts M10 (8).
2. Cover the boiler shell with layer of insulation (38) making
sure is centred and adheres properly.
3. Fit the insulating panel (37) onto the rear element,
centring the holes in the tie-rods (3).
4. Mount the rear panel (39), centring the holes in the tie-
rods (3).
5. Mount the side panels (31, 34) of the jacket.
6. Lock the side panels onto the brackets (22, 24) and to the
rear panel (39) using the screws (32).
13.2 - PLUMBING CONNECTIONS AND
HYDRAULIC TEST
(Figs. 3)
Always clean the system completely before making the plumbing
connections.
1. Mount a ½" cock (C) to drain the boiler.
2. Connect the delivery and return pipes using 1" 1/4 the
threaded fittings on the rear elements for the heating circuit.
3. Fill the boiler slowly and relieve it entirely of air. Charge the
system until the pressure is at least 1 bar.
CAUTION!
The maximum working pressure is 4 bar.
13.3 - CONTROL PANEL INSTALLATION
(Figs. 2-13-14-15-16-17-18)
1) Secure the control panel (51) onto the instrument
support (50) using the four screws (52)
2)
Unwind the capillaries of the thermostats (44, 46) and
the thermometer (49). Insert the probes in the sheath
(19) and tighten them with the probe retaining spring.
CAUTION!
When unwinding the capillaries, be very careful not
to create sharp bends or twists.
3)
Mount the complete control panel onto the side panel (31,
34) centring the holes and secure it with the two screws
(36).
4)
Connect the cable of the power supply, insert this in the
wire lead and lock this in position. Refer to paragraph 14.
WIRING for further details.
CAUTION! Connect all earthing cables to the screw.
5)
Mount the electric protection panel (48) has indicated in the
picture 16.
6)
Lastly, mount the top panel (35) and the front panel (33) in
that order.
7)
Stick the rating plate on to the right-hand side panel (31) of
the jacket.
14.
WIRING
(Figs. 2)
The boiler must be have a single-phase power supply 220/230V,
50Hz plus earth ( ) connected to terminals N and L.
CAUTION! Respect PHASE-NEUTRAL polarity!
Key to symbols:
T.R. = Boiler setting thermostat (44)
T.S. = Safety thermostat (46)
B.R. = Burner
S. = ON/OFF Switch (45)
F. = Fuse (47)
15.
CONNECTING TO THE STACK
Check that the dimensions and the status of the stack (parasite
air inlets, obstructions, etc.) are suited to the performance of the
boiler.
The cross section and height of the stack must ensure the
minimum draft as specified in the table for each model.
Proceed as follows:
•
Connect to the rear element.
•
Use a tube with a diameter that is at least the same as for the
exhaust pipe.
•
Reduce the number of bends and avoid sharp changes of
direction.
•
Make sure there is at least 5% angle of inclination for the pipe
and insulate it if necessary.
•
Check the seal of the fittings.
16.
INSTALLING THE BURNER
(Fig.1)
The lower cover (10) has a burner flange corresponding to the
one shown in Fig. 1. If the burner flange is not suited to this
flanging, an adapter and gasket must be provided. The diameter
of the burner head may differ from the diameter of the insulation.
If it is larger, widen the insulation hole. If it is smaller, add
insulation to adapt the hole ad accurately as possible to prevent
backfiring. The maximum diameter allowed is 110 mm. It is
advisable to graphitize the burner screws to facilitate removal
later on.
17.
REGULATING THERMAL
POWER
The boiler's thermal power must be regulated according to the
requirements of the system. Read the burner instructions very
carefully and use nozzles and fuel pressure to get the required
value.
Содержание GIEGA NTG
Страница 1: ...GIEGA NTG 24 75 kW GAS OR OIL BOILER INSTALLATION AND MAINTENANCE HANDBOOK 1312 1312AT2668...
Страница 13: ...GIEGA NTG 24 75 kW MANTEMENIOI 1312 1312AT2668...
Страница 14: ...1 2 1 3 4 5 1 EN 303 MANUFACTURER SERIAL NUMBER MODEL POWER...
Страница 16: ...8 2 3 10 15 3 5 27 14 20 12 18 14 20 1 BAR 100 g 1 2 46 3 44 1 2 3 4 5...
Страница 20: ...711793 Installation and mainteinance handbook GIEGA NTG 24 75 01 04 07 rev 00...