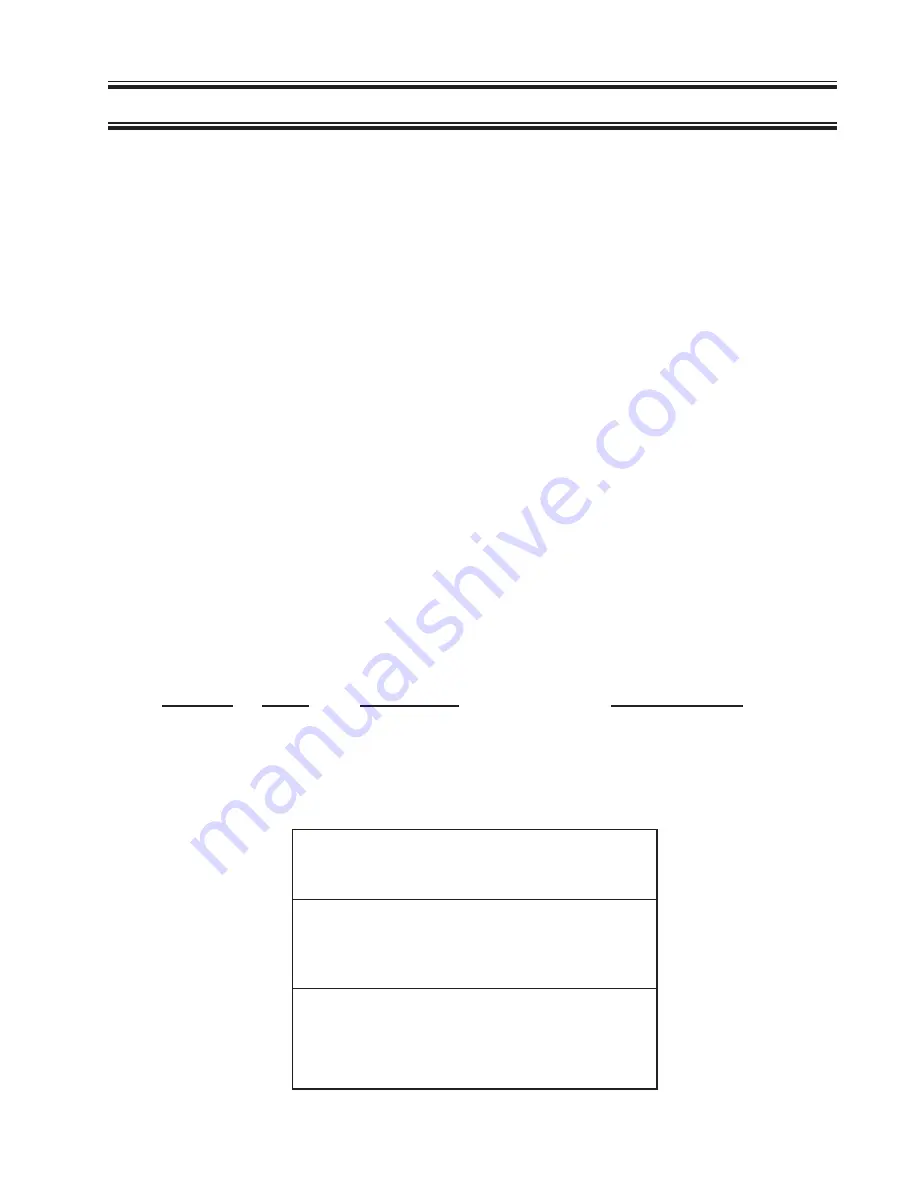
10
TO DISMANTLE GEAR END
After removing valve casing (43) and plunger pipe (29B), drain the oil. Remove the gear cover (4) and
both bearing covers (14). Loosen connecting rod screws (24A) and push the front of the connecting rod
(24) forward as far as possible into the crosshead guide.
IMPORTANT!
Connecting rods (24) are marked for identification. Do not twist connecting rod halves.
Connecting rod is to be reinstalled in the same position on shaft journals.
Turning the crankshaft (22) slightly, hit it out carefully to the side with a rubber hammer.
IMPORTANT!
Do not bend the connecting rod (24) shanks. Check crankshaft (22) and connecting rod
(24) surfaces, radial shaft seals (15) and taper roller bearings (20).
To remove the oil seals (31) use a wooden rod and sharply hit down on the oil seals from the crankcase
(1). Note: when replacing the oil seals, apply a small amount of locktight to the outside edges of each oil
seal before re-inserting them into the crankcase.
To Reassemble
Using a soft tool, press in the outer bearing ring until the outer edge lines up with the outer edge of the
bearing hole. Remove bearing cover (14) together with radial shaft seal (15) and o-ring (16). Fit crank-
shaft (22) through bearing hole on the opposite side. Press in outer bearing and tighten it inwards with
the bearing cover, keeping the crankshaft in vertical position and turning slowly so that the taper roll-
ers of the bearings touch the edge of the outer bearing ring. Adjust axial bearing clearance to at least
0.1mm and maximum 0.15mm by placing fitting discs (20A and 20B) under the bearing cover.
IMPORTANT!
After assembly has been completed, the crankshaft should turn easily with very little
clearance. Tighten connecting rod screws (24A) to 310 in.-lbs. Re-assemble the fluid end (see instruc
-
tions above).
Position
Item#
Description
Torque Amount
24A
13277
Inner Hex Screw, Connecting Rod
310 in.-lbs. (35 NM)
29C
07131-0100
Tension Screw, Plunger
265 in.-lbs. (30 NM)
48
06077-0100
Plug, Discharge
107 ft.-lbs. (145 NM)
49A
07158
Hexagon Nut, Stud Bolts
59 ft.-lbs. (80 NM)
LP301A-5100 / LP600-5100 TORQUE SPECIFICATIONS
Pump Mounting Selection Guide
Bushings
06496
- 35 mm H Bushing
Pulley & Sheaves
07165
- 12.75” Cast Iron - 4 gr.
AB Section
Rails
07357
- Plated Steel Channel Rails
(L=11.75”x W=1.88”x H=3.00”)
REPAIR INSTRUCTIONS