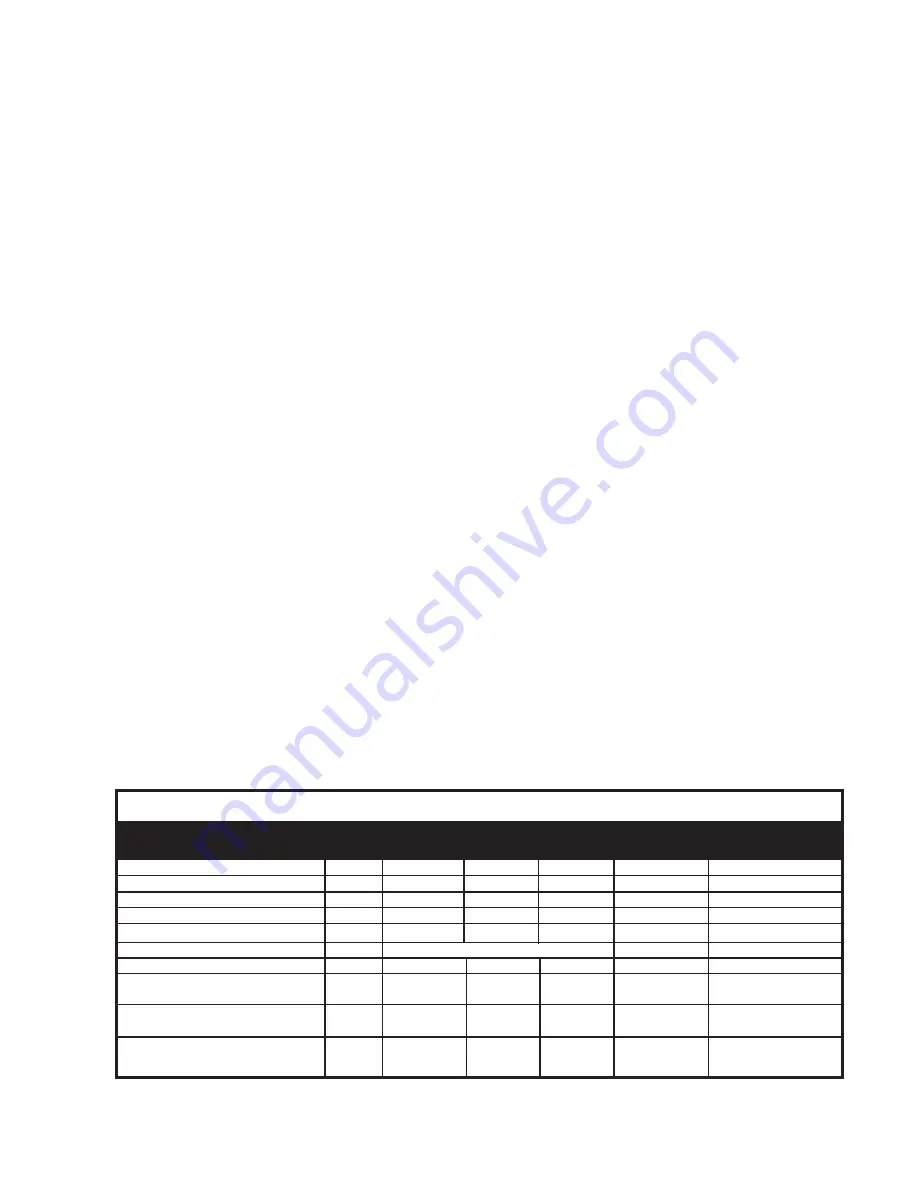
6
TO CHECK VALVES
Loosen plugs (58), take out tension spring (57) and then remove the complete valve assembly
(#51 & 52) with either a valve tool or an M16 hexagon screw. Check sealing surfaces and replace worn parts.
The discharge valve seat (# 52E) can be used on both sides. If you re-use it, make sure you switch the O-
Ring (#51D) to the opposite side. Pumps manufactured after 10/07 are supplied with valve assemblies which
screw together. Check O-rings and support rings. Tighten plugs (58) to 107 ft.-lbs. (145 NM).
TO CHECK SEALS AND PLUNGER PIPE
Loosen nuts (49A) and remove pump head. Separate plunger connection (36A) from crosshead (25) by
means of an open-end wrench (size 36). Pull seal sleeves (39) out of their fittings in the crankcase.
Take seal case (38) out of seal sleeve (39) and remove tension spring (45). Examine plunger parts (36A-
36D), seals (42,39A) and O-rings.
When replacing plunger pipe (36B), tighten tension screws (36C) to 30 ft. lbs (40 Nm).
Replace worn parts; grease seals with Silicone before installing.
CAUTION:
Don’t loosen the 3 plunger connections (36A) before the valve casing has been removed
otherwise the tension screw (36C) could hit against the spacer pipe (51E) when the pump is
being turned. Seal life can be increased if the pretensioning allows for a little leakage. This as-
sists lubrication and keeps the seals cool. It is therefore not necessary to replace seals before
the leakage becomes too heavy and causes output and operating pressure to drop. When
reassembling tighten plunger screws to 33 ft. lbs (45Nm).
MOUNTING VALVE CASING
Check O-rings on seal case (38). Clean surfaces of seal sleeves in gear box and sealing surfaces of valve
casing. Push valve casing carefully on O-rings of seal case and centering studs (50A). Tighten nuts (49A) to
103 ft. lbs (140 Nm).
TO DISASSEMBLE GEAR
Take out plunger and seal sleeves as described above. Drain oil. After removing the circlip ring (33B), lever
out seal retainer (33) with a screw driver. Check seals (32, 32A, 33A) and surfaces of crosshead. Remove
crankcase cover (4). Loosen inner hexagon screws on the connecting rods (24).
Note:
Connecting rods are marked for identification. Do not twist conn-rod halves. Conn-rod is to be
reinstalled in the same position on shaft journals. Push conrod halves together wit hthe cross-
head as far as possible into the crosshead guide. Take out bearing cover to one side and
push out crankshaft taking particular care that the conn-rod doesn’t get bent. Check surfaces
of connecing rod and crankshaft (22). Reassemble in reverse order: Regulate axial bearing
clearance minimum 0.1mm, maximum 0.15mm - by means of fitting disc (20A). Shaft should
turn easily with little clearance. Tighten screws (24) to 30 ft. lbs (40 Nm).
Note:
Connecting rod has to be able to be slightly moved sidewise at the stroke journals.
Note:
Seal (32) must always be installed so that the seal-lip on the inside diameter faces the oil.
Possible axial float of the seal adapter (33) to be compensated with shims (33C).
GP7142 REPAIR INSTRUCTIONS
Preventative Maintenance Check-List & Recommended Spare Part List
Check
Daily Weekly 50hr
Every Every
Every
500 hr 1500 hr 3000hrs
Oil Level / Quality
X
Oil
Leaks X
Water
Leaks
X
Belts, Pulley
X
Plumbing
X
Recommended
Spare
Part
Oil Change (p/n 01154)
X
X
Plunger Packing Kits (1 kit/
Pump) See page 5 for kit list
Oil Seal Kit (1 kit/Pump)
See page 5 for kit list
Valve Assembly Kit ( 1 kit/
pump)See page 5 for kit list
X
X
X
Содержание GP7142
Страница 4: ...4 Exploded View GP7142...