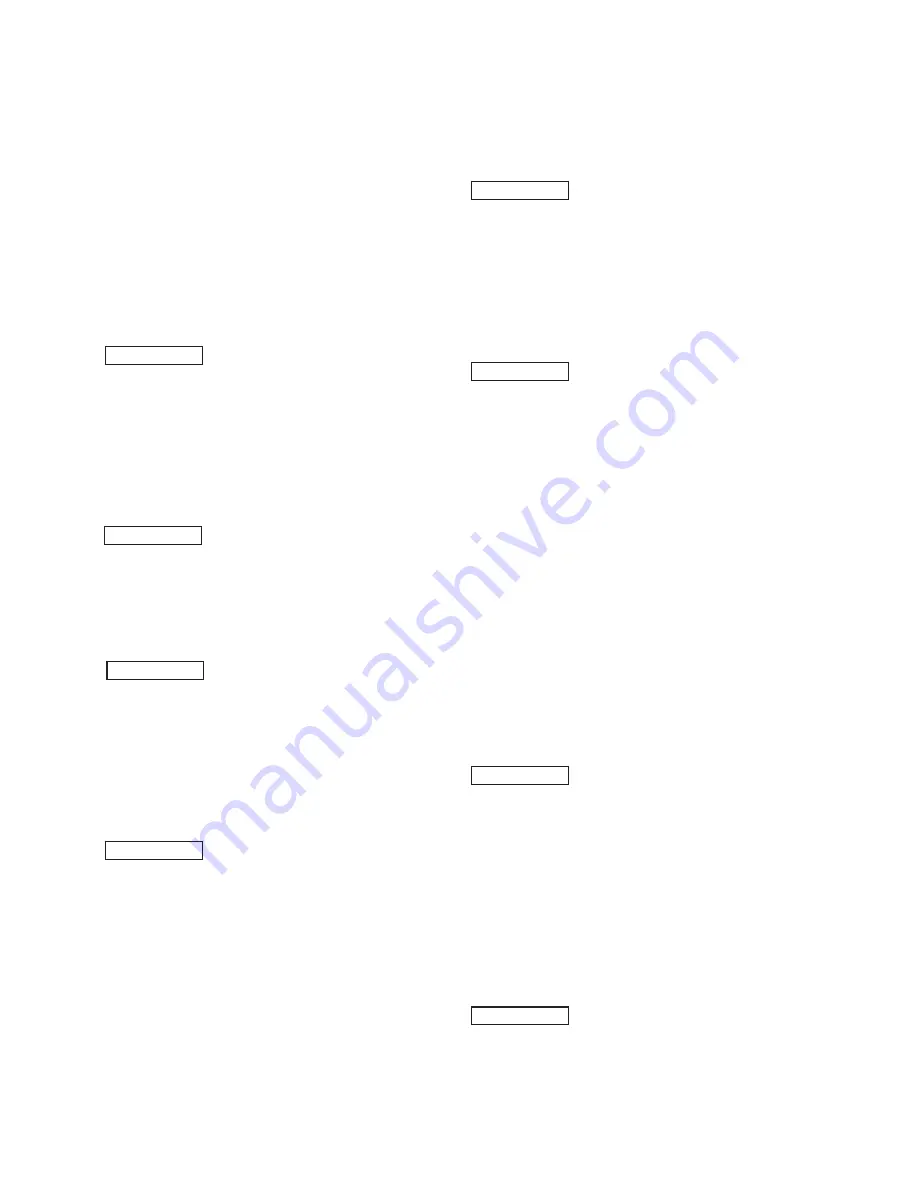
2
20 minutes an hour, with the pump running with-out
pressure or turned off in between. For example, this
can be full load operation for 5 minutes four times an
hour with 10 minute breaks in between or continuous
full load operation for 20 minutes followed by a 40
minute break.
IMPORTANT! If higher medium temperatures or
liquids other than water are involved or aggressive
media such as seawater, demineralised water etc., the
pump must be fitted with a separate cooling circuit.
The separate cooler must have a cooling efficiency of
1700 watt. If there is a danger of frost, an appropriate
amount of antifreeze must be mixed into the cooling
circuit.
When starting up for work, the pump must run first at
zero pressure for approximately 1 minute.
IMPORTANT! The GP8100 series has a black arrow
on the reduction gear which shows the preferred
direction of rotation. The pumps can be de-livered
either with the gear on the left side or right side which
eases the planning of assembling units with regard to
rotational direction.
Gear on right side from behind pump = optimal
rotation: to the left
Gear on left side from behind pump = optimal rotation:
to the right
The preferred/optimal direction of rotation ensures the
motion of the connecting rods correctly shovels the
oil on to the crosshead guides – which is a particular
advantage where continuous operation is involved.
The pump can also be run against the recommended
direction of rotation if operated periodically or at
reduced pressure. If so, the pump has to be run in
in this direction to smoothen the bearing areas. This
is done by a one-time operation at zero pressure for
at least 30 minutes; thereafter the pressure must be
slowly increased over the next hour to the desired
maximum operating pressure; the pump is then run in.
Check the oil temperature during this process.
IMPORTANT! The pump and cooling system must be
emptied if there is a danger of frost. Travel wind can
cause water in pumps fitted on open vehicles to freeze
even if the outside temperature is above freezing
point.
To empty the cooling circuit, remove the L-joints (K11)
on the pump head (50). Blow out the circuit liquid at
the joint connection (K11/K7) using compressed air.
The torque tenson on the valve casing nuts (49A) is to
be checked after approximately 200 operating hours.
Please see the section ‘Maintenance’ concerning the
torque values.
The pump must be at zero pressure when checking
the torque tension.
IMPORTANT! The service life of the seals is
maximized if a minimal amount of leckage is present.
A few drops of water can drip from each plunger every
minute. Leakage has to be examined every day;
the plunger seals must be changed should leckage
become excessive (=constant dripping).
INSTALLATION INSTRUCTIONS
The stated figures are for maximum pressure
and maximum speed (rpm) and apply for interval
operation with cold water.
Required NPSH refers to water (specific weight 1kg/
dm3, viscosity 1°E) at maximum permissible pump
revolutions.
Fluid medium: Clean water filtered with 200μm.
*higher temperatures possible with separate
crankcase cooling system; the manufacturer is to be
contacted in this case.
Operation and Maintenance
Check oil level prior to starting and ensure trouble-
free water supply.
IMPORTANT! If there is a
danger of frost
,
the water in the pump and in the pump fittings
(particularly the unloader valve) must be emptied.
The second discharge port can also be used and the
pump run “dry” for 1-2 minutes for this purpose.
Oil amount:
4.2 gallons (16.0 litres). Only use
ISO
VG 220 industrial gear oil
(e.g. Aral Degol BG220)
or
automobile gear oil SAE 90 GL4
. Initial change
after 50 operating hours and then every 1000
operating hours after one year latest.
IMPORTANT! When operating in damp places
or with high temperature fluctuations. Oil must be
changed immediately should condensate (frothy oil)
occur in the gear box.
NPSH values must be observed.
Cooling the Gear Oil
IMPORTANT! The water input pressure must not
exceed 29 PSI (2 bar) when using the integrated
system for cooling the gear oil (standard version).
If a
separate
cooling circuit (maximum 29 PSI [2
bar]) is installed, it is then possible to have an input
pressure of up to maximum 145 PSI (10 bar) on the
suction side
of the pump.
Make sure that suction pulsation is sufficiently
dampened – water column resonance must be
avoided.
IMPORTANT! The pumps can be run without gear
oil cooling in continuous operation
up to
a power
rating of
93.9 HP (70 kW)
or with major intermit-tent
operation at full performance.
If operational power
exceeds 93.9 HP (70 kW)
or if
continuous operation is the case, the pump must be
run with the integrated oil cooling system. The max.
temperature of the water being pumped and which is
also fed through the cooling system must not exceed
86 °F (30 °C). The water amount which is fed into
the cooling system depends on the pump speed and
is approximately 1.9 GPM (7.0 L/min) at 580 pump
rpm. The cooling water is sucked in by one of the
pumping chambers and pumped away.
Definition of intermittent operation:
operation
at full performance for not more than altogether
Содержание GEARBOX Series
Страница 6: ...6 Exploded View GP8155 GP8160 GP8165 ...