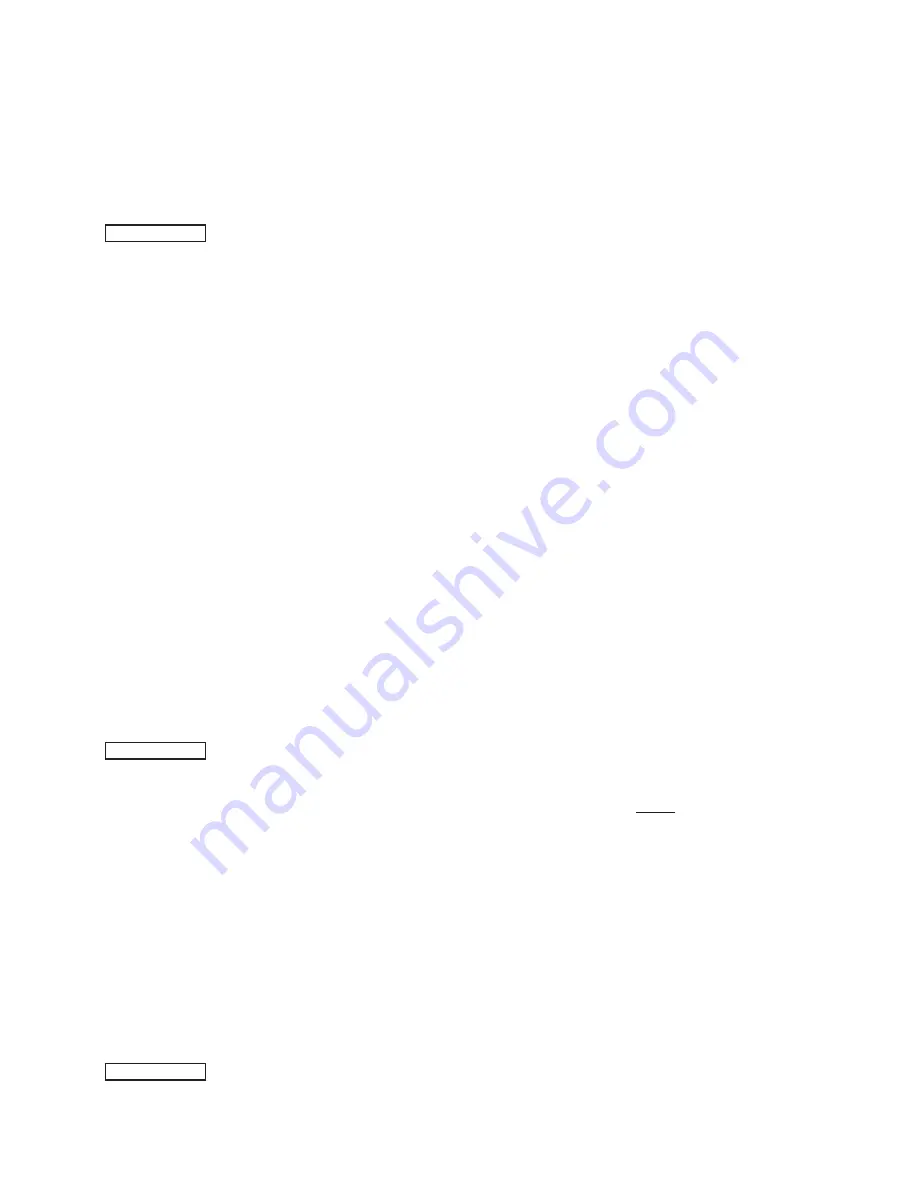
10
Pump Repair Instructions - GP8155/GP8160/GP8165
To Dismantle Gear
Take out plungers and seal sleeves as described above.
Drain oil by taking off plug (12).
After removing the clip ring (33B), remove the seal retainer (33) with a screwdriver. Open hose adaptor (K11).
Remove gear cover (K3) and remove the cooling vane plate (K1) by unscrewing the screws (K4). Remove
connecting rod screws (24).
IMPORTANT!
Connecting rods are marked for identification. Do not twist connecting rod halves or
interchange them. When reassembling, the connecting rods must be fitted in their exact original position on
the crankshaft journals.
Push connecting rod halves together with the crosshead as far as possible into the crosshead guide.
Remove bearing cover (14), remove shims (21A/B).
To Dismantle Gearbox
Remove screws (67). Press off gear cover (66) by screwing two screws into both thread bores. Remove
screw (72) and take off plate (71). Remove the gearwheel (69) from the shaft with a bearing removal tool.
Using a rubber hammer, tap out the crankshaft towards bearing cover (14).
Check surfaces on the connecting rods (24), crankshaft (22) and crossheads (25). Check the surfaces of the
crosshead guides in the crankcase (1) for any unevenness.
Reassemble in reverse order. Thread the crankshaft in from the bearing cover side until the bearing rests
cleanly in the outer ring on flange (19).
Press in the outer ring from bearing (20) and using shims (21A/B/C), adjust the bearing to be free of play. To
achieve this, add shims, screw on cover (14) and turn the crankshaft until it can no longer be turned by hand.
Then remove a shim and establish whether the crankshaft can now be turned. A crankshaft that can be
too easily turned may cause damage to the bearings (20/21) and connecting rods (24) due to the wobble
movements in the conical bearing shells.
If bearings (20 & 21) have been replaced, the flange (19) must be taken off and a new bearing outer ring
pressed in until the surfaces are even. Then mount the holding flange to push the bearing outer ring in
deeper.
Mount connecting rod halves in their exact original position and tighten at 37 ft.-lbs. (50 Nm).
IMPORTANT!
A little clearance must exist to enable slight sideward movement of the connecting rod on its
journal.
Mount cooler plate (K1) and gear cover (K3) with their respective seals (K2). When assembling the cooling
circuit line, make sure that the oil cooler connection (K7) is always joined to the upper connection (K3) of the
gear cover.
To Reassemble Gearbox
Heat ball bearings (74 & 75) first before pressing them onto the pinion. Press the cogwheel slightly onto the
crankshaft (22) so that the pinion shaft (69) together with the bearing (74) can still be inserted.
Move the pinion shaft against the cogwheel and make them mate perfectly when mounting. Carefully tap the
cogwheel and the pinion shaft simultaneously onto the crankshaft and into the bearing seat.
Fit fitting disc (69), and secure screw (72) with Loctite.
Fit the seal (76) onto the cylindrical pins (68).
Push the gear cover (66) carefully onto the bearing (75). Make sure that no damage to the radial shaft seal
(73) occurs during the fitting onto the pinion shaft.
IMPORTANT!
Before putting into operation again, turn the reduction gear shaft by hand at least four full turns
to make sure the gear is correctly aligned.
Содержание GEARBOX Series
Страница 6: ...6 Exploded View GP8155 GP8160 GP8165 ...