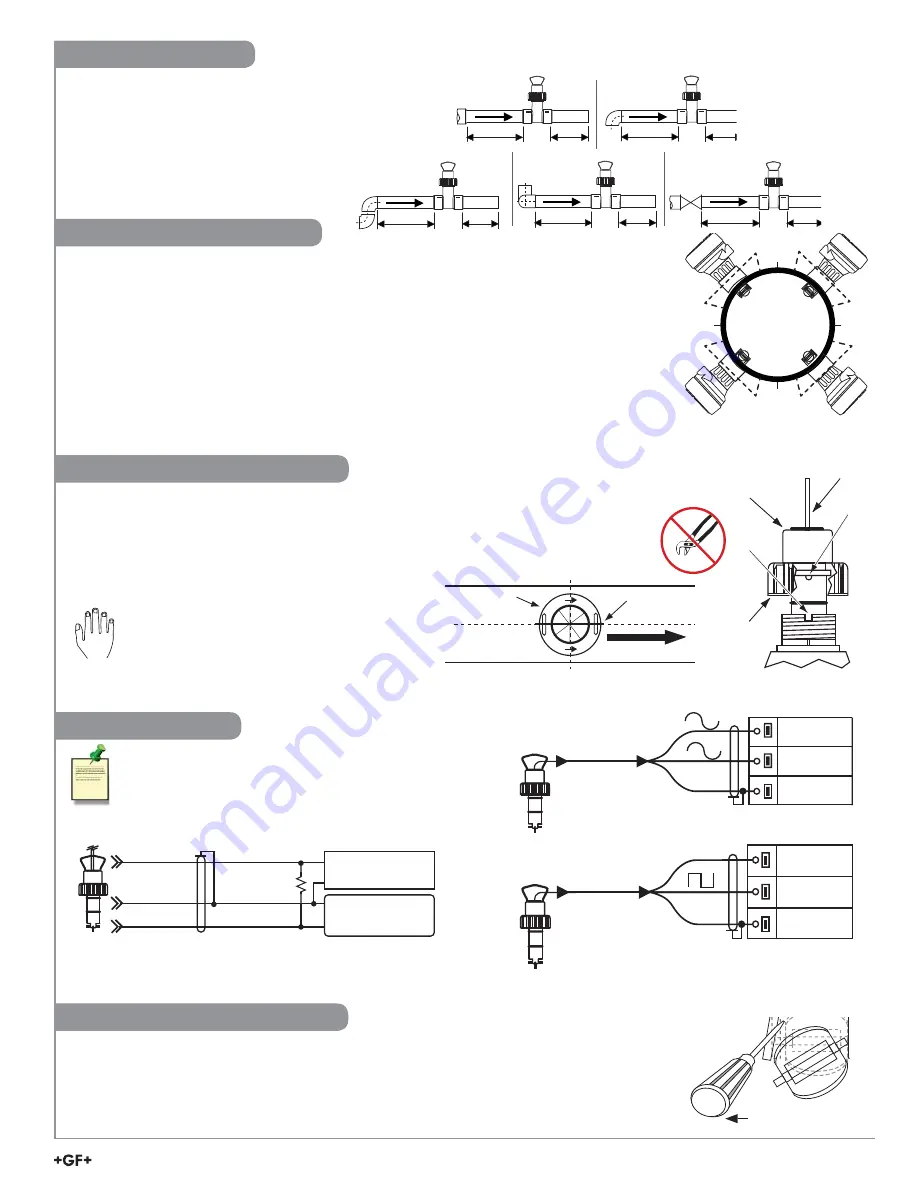
5
Signet 515/2536 Rotor-X Flow Sensors
40x I.D.
5x I.D.
25x I.D.
5x I.D.
50x I.D.
5x I.D.
2 x 90° Elbow
3 dimensions
2 x 90° Elbow
Pump/Valve
15x I.D.
5x I.D.
20x I.D.
5x I.D
Reducer
90° Elbow
Location of Fitting
• To remove the rotor, insert a small screwdriver between the rotor and the ear of the sensor.
• Twist the screwdriver blade to
fl
ex the ear outward enough to remove one end of the rotor and pin.
• DO
NOT
fl
ex the ear any more than necessary! If it breaks, the sensor cannot be repaired.
• Install the new rotor by inserting one tip of the pin into the hole,
then
fl
ex the opposite ear back enough to slip rotor into place.
180°
90°
90°
0°
senso
bale
sensor
cap
tab
black
conduit
cap
notch
Figure B
black conduit
cap
PROCESS PIPE
(TOP VIEW)
direction of flow
sensor bale
Figure A
Black
Frequency (-)
Red
Frequency (+)
Shield
Ground
515 Sensor Connections to
Signet Instruments
Black
5 VDC
Red
Frequency in
Shield
Ground
2536 Sensor Connections to
Signet Instruments
10 K
+
-
Other Brands
DC sensor power supplied from Signet instrument.
10 K
Pull-up resistor may be required for non-Signet brand instrument.
Input
Gnd.
3.3 to 24
VDC
Black
Shield
Red
Other
instrument
• Lubricate O-rings with a non-petroleum based, viscous lubricant (grease)
compatible with the system.
• Using an alternating/twisting motion, lower the sensor into the
fi
tting, making sure the
installation arrows on the black cap are pointing in the direction of
fl
ow, see Figure A.
• Engage one thread of the sensor cap then turn the sensor until the alignment tab is seated in
the
fi
tting notch.
Hand tighten the sensor cap.
DO NOT use any tools on the sensor cap or
the cap threads and/or fi tting fl ange threads
will be damaged, see Figure B.
Technical Notes
• Use 2-conductor shielded cable for cable extensions.
• Cable shield must be maintained through cable splice.
• Refer to your instrument manual for speci
fi
c wiring
details.
Sensor Mounting Position
Standard Sensor Installation
Sensor Wiring
Rotor Replacement Procedure
To ensure the
fl
uid velocity pro
fi
le is fully
developed, without distortion from piping system
components, please adhere to the recommended
straight run geometry.
Horizontal pipe Runs
To minimize adverse effects of air pockets, sediment, or excessive rotor wear (Paddlewheels), avoid
mounting the
fl
ow sensor at the top of the pipe (0º), bottom of pipe (180º), or the sides (90º from
vertical.)
Vertical Pipe Runs
Mount
fl
ow sensors in any direction. To ensure pipe is
fl
owing full, with some back pressure, it’s highly
recommended the
fl
uid
fl
ow is upward.
Gravity and Discharge Lines
It’s recommended to install a trap to ensure pipe is full during
fl
ow conditions, and to minimize
air pockets.