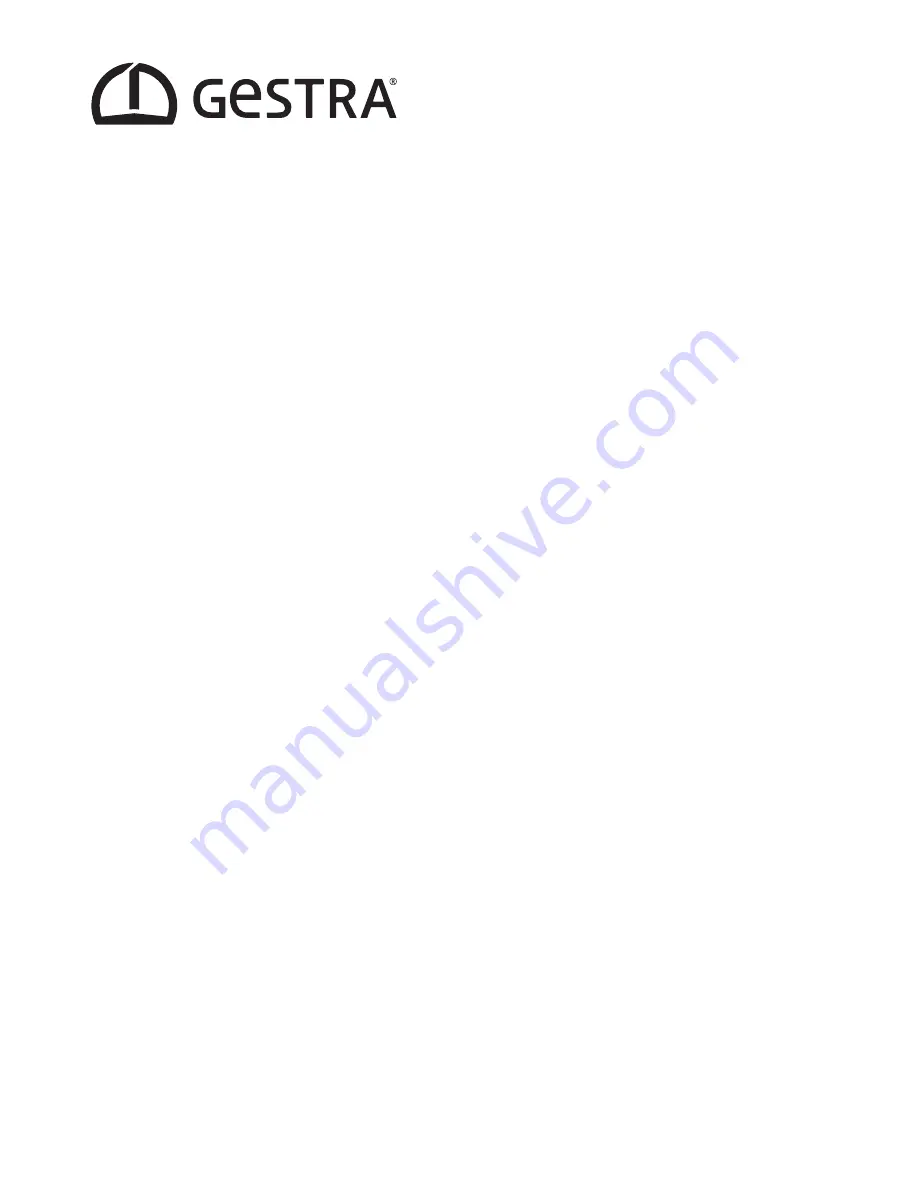
36
818548-02/07-2017cm (808607-02) · GESTRA AG · Bremen · Printed in Germany
GESTRA AG
Münchener Straße 77
28215 Bremen
Germany
Telefon +49 421 3503-0
Telefax +49 421 3503-393
E-mail [email protected]
Web www.gestra.de
Agencies all over the world:
www.gestra.de