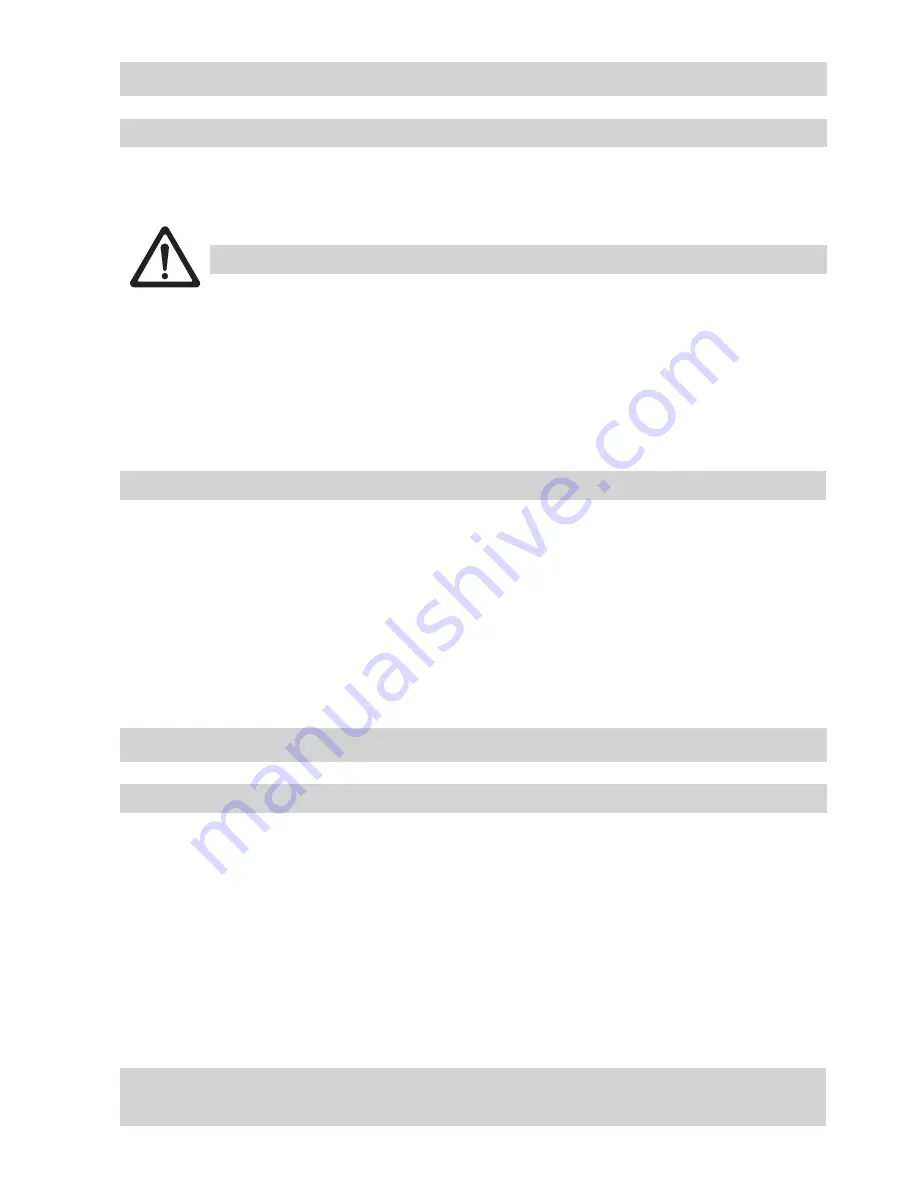
15
If faults occur that are not listed above or cannot be corrected, please contact our service centre or
authorized agency in your country.
Cleaning measuring electrode
1. Loosen screws
a
.
Fig. 8
2. Detach upper part of the terminal box
c
from the conductivity electrode.
3. Before removing the equipment make sure that is is neither hot nor under pressure.
Cleaning the measuring electrode (measuring surface):
Wipe off non-adhesive deposits with a grease-free cloth.
To remove adhesive deposits use emery cloth (medium grain).
Re-install the conductivity electrode. Observe the notes given in section "Installation" and "Electrical
Connection".
Maintenance
Safety note
Danger
When loosening the conductivity electrode steam or hot water might escape!
This presents the risk of severe scalding all over the body!
It is therefore essential not to dismantle the conductivity electrode unless the boiler
pressure is verified to be 0 bar.
The conductivity electrode becomes hot during operation.
Risk of severe burns to hands and arms.
Before carrying out installation and maintenance work make sure that the equipment is
cold.
The equipment must only be installed, wired and commissioned by qualified and competent staff.
Retrofitting and maintenance work must only be performed by qualified staff who - through adequate
training - have achieved a recognised level of competence.
Removing and disposing of the conductivity electrode
Remove and discard conductivity electrode LRG 16-4.
1. Loosen screw
i
.
Fig. 22
2. Detach upper part of the terminal box
k
from the conductivity electrode.
3. Before removing the equipment make sure that is is neither hot nor under pressure.
For the disposal of the equipment observe the pertinent legal regulations concerning waste disposal.