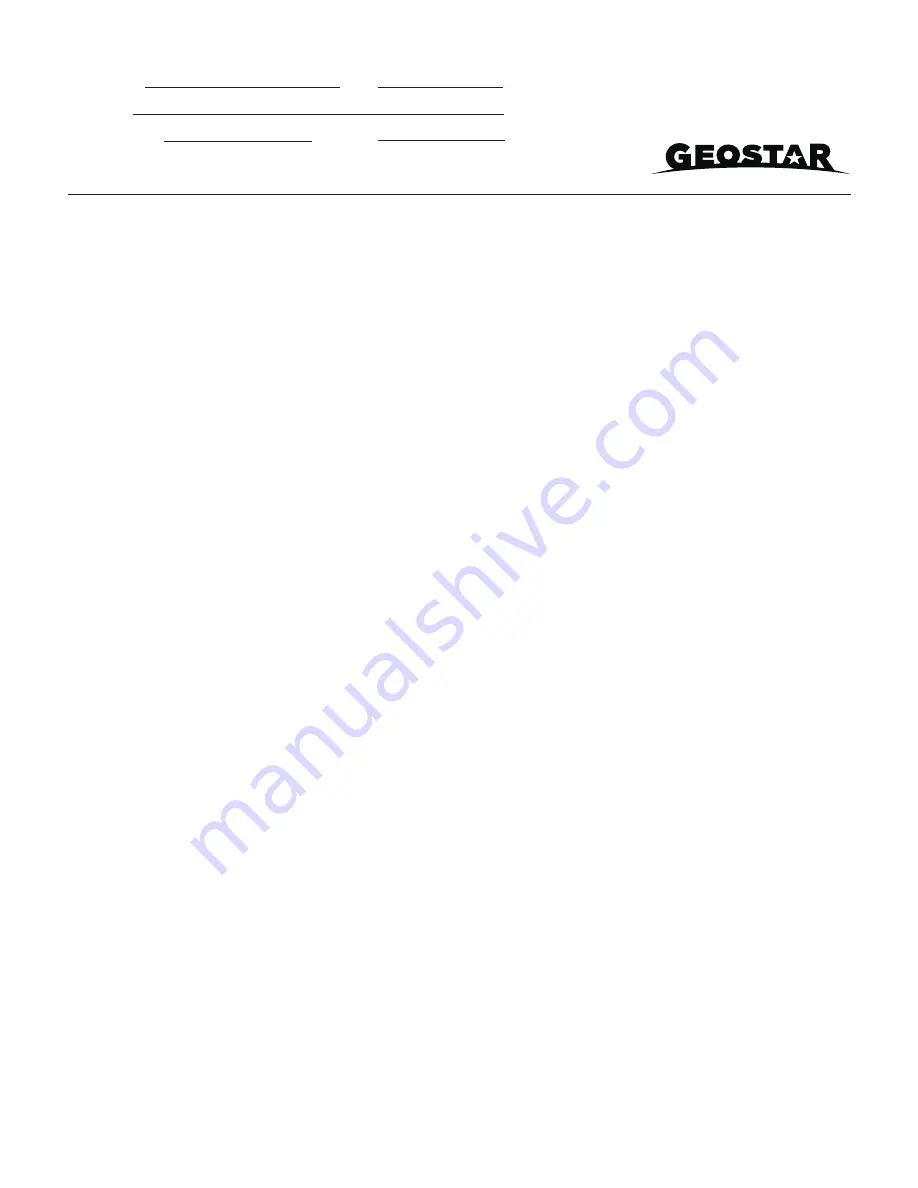
Contractor:
P.O.:
Engineer:
Project Name:
Unit Tag:
The manufacturer works continually to improve its products. As a result, the design and speci
fi
cations of each product at the time of order may be changed without notice. Purchaser’s approval of this data set signi
fi
es that the equipment is acceptable under the provisions
of the job speci
fi
cation. Statements and other information contained herein are not express warranties and do not form the basis of any bargain between the parties, but are merely the manufacturer’s opinion or commendation of its products. York and Af
fi
nity are registered
trademarks of Johnson Controls, Inc., and are used with permission.
Engineering Guide Speci
fi
cations
SD2500AG 05/21
62
Page _____ of _____
Aston Series
1 - 6 Tons 60Hz
General
Furnish and install GeoStar Water Source Heat Pumps, as
indicated on the plans. Equipment shall be completely assembled,
piped and internally wired. Capacities and characteristics as
listed in the schedule and the specifications that follow. The
reverse cycle heating/cooling units shall be either suspended
type with horizontal air inlet and discharge or floor mounted type
with horizontal air inlet and vertical upflow, downflow, or rear air
discharge. Units shall be AHRI/ISO 13256-1 certified and listed
by a nationally recognized safety-testing laboratory or agency,
such as ETL Testing Laboratory. Each unit shall be computer
run-tested at the factory with conditioned water and operation
verified to catalog data. Each unit shall be mounted on a pallet and
shipped in a corrugated box or stretch-wrapped. The units shall be
designed to operate with entering liquid temperature between 20°F
and 120°F [-6.7°C and 48.9°C].
Casing and Cabinet
The cabinet shall be fabricated from heavy-gauge galvanized
steel and finished with corrosion-resistant powder coating. This
corrosion protection system shall meet the stringent 1000 hour
salt spray test per ASTM B117. The interior shall be insulated with
1/2-inch thick, multi-density, cleanable aluminum foil coated glass
fiber with edges sealed or tucked under flanges to prevent the
introduction of glass fibers into the discharge air. Standard cabinet
panel insulation must meet NFPA 90A requirements, air erosion
and mold growth limits of UL-181, stringent fungal resistance
test per ASTM-C1071 and ASTM G21, and shall meet zero level
bacteria growth per ASTM G22. Unit insulation must meet these
stringent requirements or unit(s) will not be accepted.
One (horizontal) to two (vertical) blower and three compressor
compartment access panels shall be ‘lift-out’ removable with supply
and return ductwork in place. The front access panel shall be lift-out
to provide easy access to the electrical/compressor section. The
control box shall be hinged and removable to allow easy access
to the compressor. The internal component layout shall provide for
service access from the front side for restricted installations.
A duct collar shall be provided on the supply air opening. Standard
size 2 in. [5.1 cm] MERV 11 pleated filters shall be provided with
each unit. Vertical units shall have a return air filter rack/duct collar;
the horizontal units shall have a filter bracket each field convertible
from 2 in. [5.1 cm] to 1 in. [2.5 cm]. The upflow vertical (022-072)
units shall have a removable insulated divider panel between the
air handling section and the compressor section to minimize the
transmission of compressor noise and to permit operational service
testing without air bypass. Vertical units shall be supplied with
left or right horizontal air inlet and top, bottom (022-072), or rear
vertical (042-072) air discharge. Horizontal units shall be supplied
with left or right air inlet and side or end air discharge.
The compressor shall be double isolation mounted using selected
durometer grommets to provide vibration free compressor mounting.
The drain pan shall be of plastic construction to inhibit corrosion
and bacterial growth. Drain outlet shall be located on pan as
to allow complete and unobstructed drainage of condensate.
The unit as standard will be supplied with solid-state electronic
condensate overflow protection. Mechanical float switches WILL
NOT be accepted. Vertical units shall be furnished with a PVC
slip condensate drain connection and an internal factory installed
condensate trap.
Refrigerant Circuit
All units shall contain a sealed refrigerant circuit including a
hermetic motor-compressor, discharge line muffler (022-072),
bidirectional thermostatic expansion valve, finned tube air-to-
refrigerant heat exchanger, reversing valve, coaxial tube water-
to-refrigerant heat exchanger, optional hot water generator coil
(018-072), and service ports.
Compressors shall be high-efficiency single speed rotary or
scroll, or dual capacity scroll type designed for heat pump duty
and mounted on vibration isolators. Compressor motors shall
be single-phase PSC with overload protection. The finned tube
air-to-refrigerant heat exchanger will be aluminum tube/fin or
copper tube/aluminum fin and shall be sized for low-face velocity
and constructed of lanced aluminum fins bonded to performance
enhanced tubes in a staggered pattern not less than three rows
deep for superior performance. The aluminum tube and fin air-to-
refrigerant heat exchanger has as optional to be electro-coated
with AlumiSeal. The copper tube aluminum fin air-to-refrigerant
heat exchanger will be constructed of patented 11 element fin
and double electro-coated for corrosion protection. Models 022-
072 shall include discharge mufflers to help quiet compressor
discharge gas pulsations. Refrigerant to air heat exchangers shall
utilize enhanced tube construction rated to withstand 600 psig (4135
kPa) refrigerant working pressure.
The coaxial water-to-refrigerant heat exchanger shall be designed
for low water pressure drop and constructed of a convoluted copper
(cupronickel option) inner tube and a steel outer tube. Refrigerant to
water heat exchangers shall be of copper inner water tube and steel
refrigerant outer tube design, rated to withstand 600 psig (4135 kPa)
working refrigerant pressure and 450 psig (3101 kPa) working water
pressure. The thermostatic expansion valve shall provide proper
superheat over the entire liquid temperature range with minimal
“hunting.” The valve shall operate bidirectionally without the use of
check valves.
All units shall have the source coaxial tube refrigerant-to-water
heat exchanger and the optional hot water generator coil shall
be coated with ThermaShield. Refrigerant suction lines shall be
insulated to prevent condensation at low liquid temperatures.