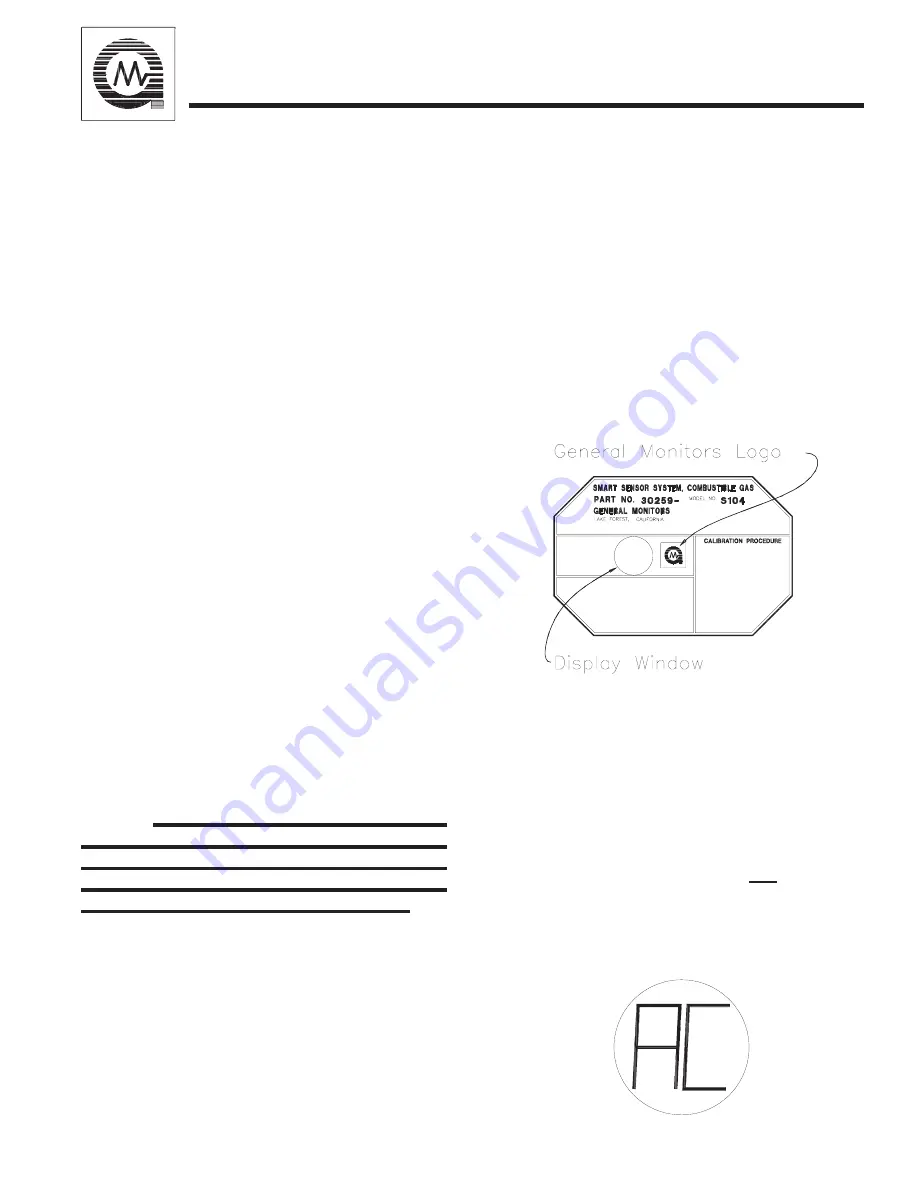
4.0 Operation
4.1
Calibration
Activating the Calibration Switch will auto-
matically disable the alarm circuits by sending
a 1.5mA (0mA optional) output signal. This
will prevent activation of the relay contacts
when using a General Monitors Readout/Re-
lay Display Module with the Model S104.
General Monitors recommends that the Model
S104 Combustible Gas Enhanced Smart Sen-
sor be calibrated one hour after start-up, and
that calibration be checked at least every
ninety (90) days to ensure system integrity.
General Monitors is not implying that the cus-
tomer should expect problems with sensor life
or stability but “frequent” calibration checks
merely ensure the integrity of the life protect-
ing equipment.
The above statement is not intended to dis-
courage the customer from checking calibra-
tion more frequently.
Frequent calibration
checks are recommended for environments
that have problems such as mud collecting on
the sensor head, sensors accidentally being
painted over, etc.
NOTE: A calibration check consists of ap-
plying a known concentration of gas to the
sensor and observing the reading on the
Model S104, the Readout/Relay Module, or
other computer data collecting systems.
General Monitors recommends that a calibra-
tion schedule be established and followed. A
log book should also be kept showing calibra-
tion dates and dates of sensor replacement.
Procedure with digital display:
l
If it is suspected that combustible gas is
present, it will be necessary to purge the
sensor environment with Zero Air. If
Zero Air is not available, cover the sensor
for about thirty seconds before applying
the calibration gas. Zero Air is air that is
hydrocarbon free.
figure 12
l
Place the magnet over the GMI Logo on
the cover (figure 12) of the unit and hold it
there until “AC” (figure 13) appears on
the display (about ten seconds). Allow
about five seconds for the unit to acquire
the zero reading before applying the
calibration gas. If the GMI Portable Purge
Calibrator (P/N 1400150) is not used
when calibrating the Model S104 with
Methane (CH
4
), the SPAN gas flow rate
needs to be 440cc/min to 460cc/min. See
Appendix, section 5.4.
11
figure 13
GENERAL MONITORS
Model S104