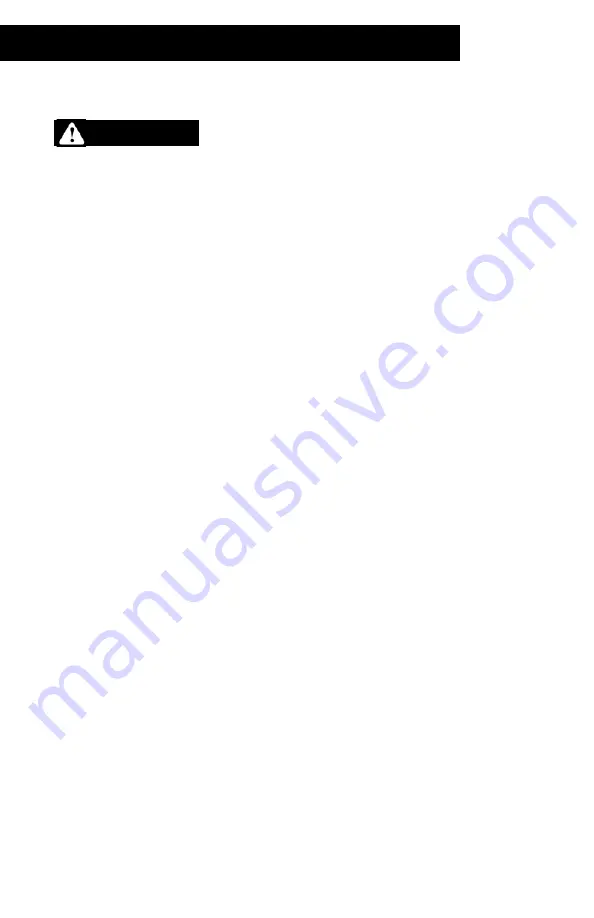
121
50940193/DP0415
CHAPTER 6
MAINTENANCE
Read and understand the “Safety” Chapter in this
manual, starting on page 15, before servicing the
machine. Follow all applicable warnings and instructions. Check for
correct function after performing maintenance. Failure to follow
instructions can result in injury or death.
BEFORE performing any maintenance, perform the “Mandatory Safety
Shutdown Procedure” on page 14.
Fluid leaks from hydraulic hoses or pressurized components can be
difficult to see, but pressurized oil can have enough force to pierce the
skin and cause serious injury. Always use a piece of wood or cardboard
to check for suspected hydraulic leaks. Never use your hands. Obtain
immediate medical attention if pressurized oil pierces the skin. Failure
to obtain prompt medical assistance could result in gangrene or other
serious damage to tissue.
Do not smoke or allow any open flames in the area while checking or
servicing the hydraulic, battery and fuel systems because all contain
highly flammable liquids or explosive gases, which can cause an
explosion or fire if ignited.
Wear a face shield when disassembling spring-loaded components or
working with battery acid. Always wear eye protection to protect eyes
from electric arcs from shorts, fluids under pressure, and flying debris
or loose material. Wear a helmet or goggles with special lenses when
welding or cutting with a torch.
When working beneath a raised machine, always use blocks, jack-
stands or other rigid and stable supports. Wear appropriate protective
clothing, gloves and shoes. Keep feet, clothing, hands and hair away
from moving parts.
Always apply the lift arm support when maintenance work requires the
lift arm in the raised position. See “Lift Arm Support” on page 44.
WARNING
Содержание R135
Страница 130: ...126 50940193 DP0415 Table 17 Maintenance Log Date Hours Maintenance Procedure...
Страница 131: ...127 50940193 DP0415 Table 17 Maintenance Log Date Hours Maintenance Procedure...
Страница 162: ...158 50940193 DP0415 NOTES...
Страница 186: ...182 50940193 DP0415 NOTES...
Страница 200: ...196 50940193 DP0415 NOTES...