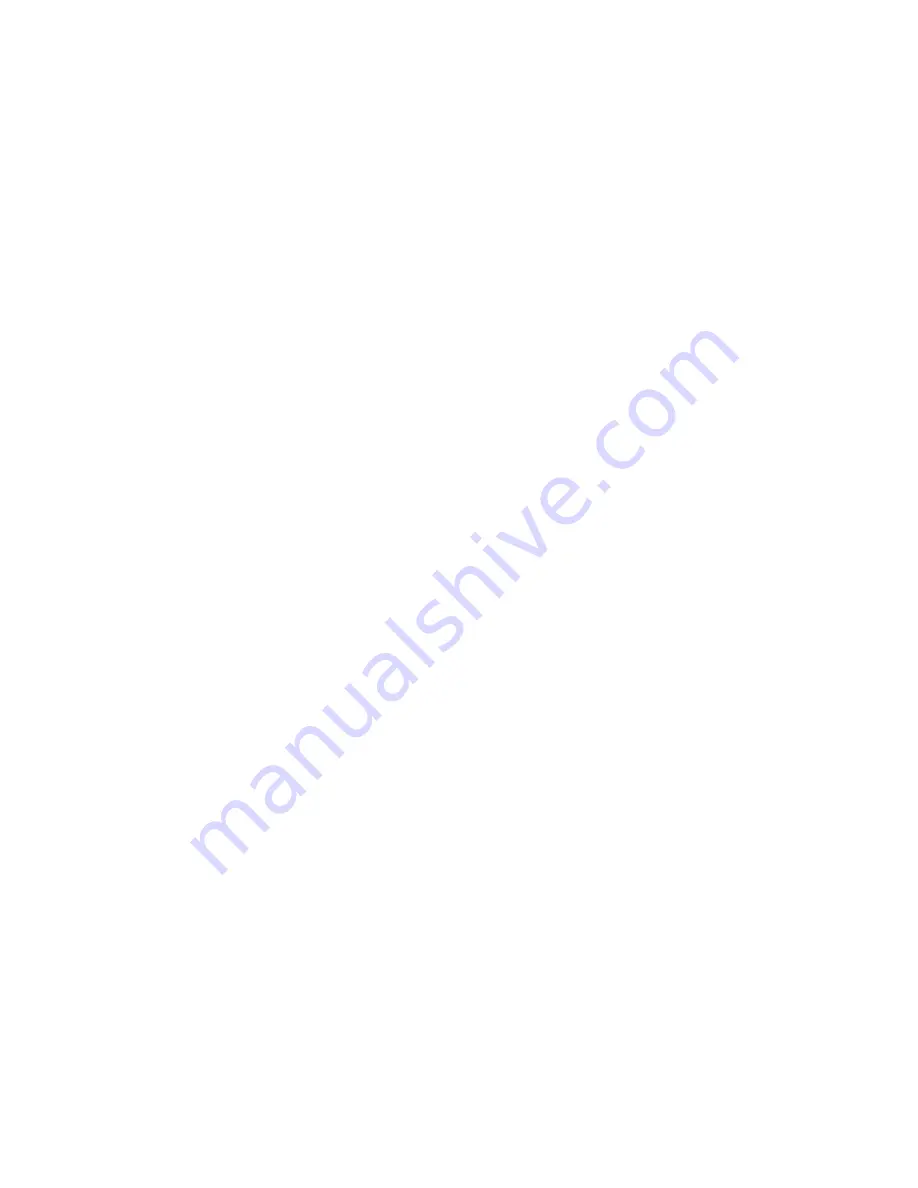
Non-repetitive overcurrent t=20 ms: 600A
I
2
t for blowout:
≤
1010A
2
s
dV/dt critical with output deactivated:
1000V/µs
GT 50 (SCR version)
Nominal currents of the device with
opportune heatsink in continuous work:
50A
Non-repetitive overcurrent t=20 ms: 1150A
I
2
t for blowout:
≤
6600A
2
s
dV/dt critical with output deactivated:
1000V/µs
GT 60 (SCR version)
Nominal currents of the device with
opportune heatsink in continuous work:
60A
Non-repetitive overcurrent t=20 ms: 1150A
I
2
t for blowout:
≤
6600A
2
s
dV/dt critical with output deactivated:
1000V/µs
GT 75 (SCR version)
Nominal currents of the device with
opportune heatsink in continuous work:
75A
Non-repetitive overcurrent t=20 ms: 1300A
I
2
t for blowout:
≤
8000A
2
s
dV/dt critical with output deactivated:
1000V/µs
GT 90 (SCR version)
Nominal currents of the device with
opportune heatsink in continuous work:
90A
Non-repetitive overcurrent t=20 ms: 1500A
I
2
t for blowout:
≤
11200A
2
s
dV/dt critical with output deactivated:
1000V/µs
GT 120 (SCR version)
Nominal currents of the device with
opportune heatsink in continuous work:
120A (complete with fan and standard
thermostat).
Non-repetitive overcurrent t=20 ms: 1500A
I
2
t for blowout:
≤
11200A
2
s
dV/dt critical with output deactivated:
1000V/µs
Isolation
Rated isolation voltage input/output:
4000Vac
Power supply
:
24Vac ±10%, 50/60 Hz
Absorption
: 1.5VA
Max. isolation voltage
: 300Vdc
Options:
Interrupted HB load alarm.
Controls the load by measuring current
on a shunt inside the device.
The alarm limit is set with a multirev
monorev trimmer.
The alarm output is obtained by means of
a solid state relay.
The contact is normally open (max. 30V,
150mA, conduction resistance 15
Ω
).
Thermal features
GT 25
Junction temperature:
≤
125°C
Rth junction/case:
≤
1.25 K/W
Rth junction/ambient:
≤
12 K/W
GT 40
Junction temperature:
≤
125°C
Rth junction/case:
≤
0.65 K/W
Rth junction/ambient:
≤
12 K/W
GT 50
Junction temperature:
≤
125°C
Rth junction/case:
≤
0.35 K/W
Rth junction/ambient:
≤
12 K/W
GT 60
Junction temperature:
≤
125°C
Rth junction/case:
≤
0.35 K/W
Rth junction/ambient:
≤
12 K/W
GT 75
Junction temperature:
≤
125°C
Rth junction/case:
≤
0.3 K/W
Rth junction/ambient:
≤
12 K/W
GT 90
Junction temperature:
≤
125°C
Rth junction/case:
≤
0.3 K/W
Rth junction/ambient:
≤
12 K/W
GT 120
Junction temperature:
≤
125°C
Rth junction/case:
≤
0.25 K/W
Rth junction/ambient:
≤
12 K/W
Solid State Relay Dissipated Power
Calculation
Singol-phase static relay
Pds = 1.4 * IRMS [W]
IRMS = singol phase load current
Heatsink thermal resistance
Calculation
Rth = (90°C - T.amb. max) / Pd
where Pd = dissipated power
T.amb.max = max air temperature inside
the electrical cabinet.
Use a heatsink with thermal resistance
inferior to the calculated one (Rth).
Ambient conditions
• Working temperature: 0 to 80°C.
• Max. relative humidity: 50% at 40°C
• Max. installation altitude:
2000m asl
• Pollution level: 3
• Storage temperature: -20..85°C
Installation notes
- The heat sink must be grounded.
- The device must be protected by an
appropriate high-speed fuse (accessory).
- Applications with solid state power units
must also include an automatic safety
switch to cut out the load power line.
- Protect the solid state relay by using an
appropriate heat sink (accessory).
The heat sink must be sized according to
room temperature and load current (see
the technical documentation).
- Procedure for mounting on heat sink:
The module-heat sink contact surface
must have a maximum planarity error of
0.05mm. and maximum roughness of
0.02mm. The fastening holes on the heat
sink must be threaded and countersunk.
Attention: spread 1 gram of
thermoconductive silicone (we
recommend DOW CORNING 340
HeatSink) on the dissipative metal
surface of the module.
The surfaces must be clean and there
must be no impurities in the
thermoconductive paste.
Alternately tighten the two fastening
screws until reaching a torque of 0.60
Nm for the M4 screws and 0.75 Nm for
the M5 screws.
Wait 30 minutes for any excess paste to
drain.
Alternately tighten the two fastening
screws until reaching a torque of 1.2 Nm
for the M4 screws and 1.5 Nm for the M5
screws.
We advise you to randomly check for
proper installation by dismantling the
module to make sure there are no air
bubbles under the copper plate.
Limits of use
• dissipation of thermal power of device
with restrictions on temperature of
installation site.
• requires exchange with outside air
or an air conditioner to transfer
dissipated power outside the panel.
• installation restrictions (distances
between devices to guarantee dissipation
by natural convection).
• max. voltage limits and derivative
of transients in line, for which the
solid state unit has internal protection
devices (depending on model).
• presence of dispersion current
< 3mA for SCR version GS
< 4mA for TRIAC version GS
(max. value with rated voltage
and junction temperature of 125°C).