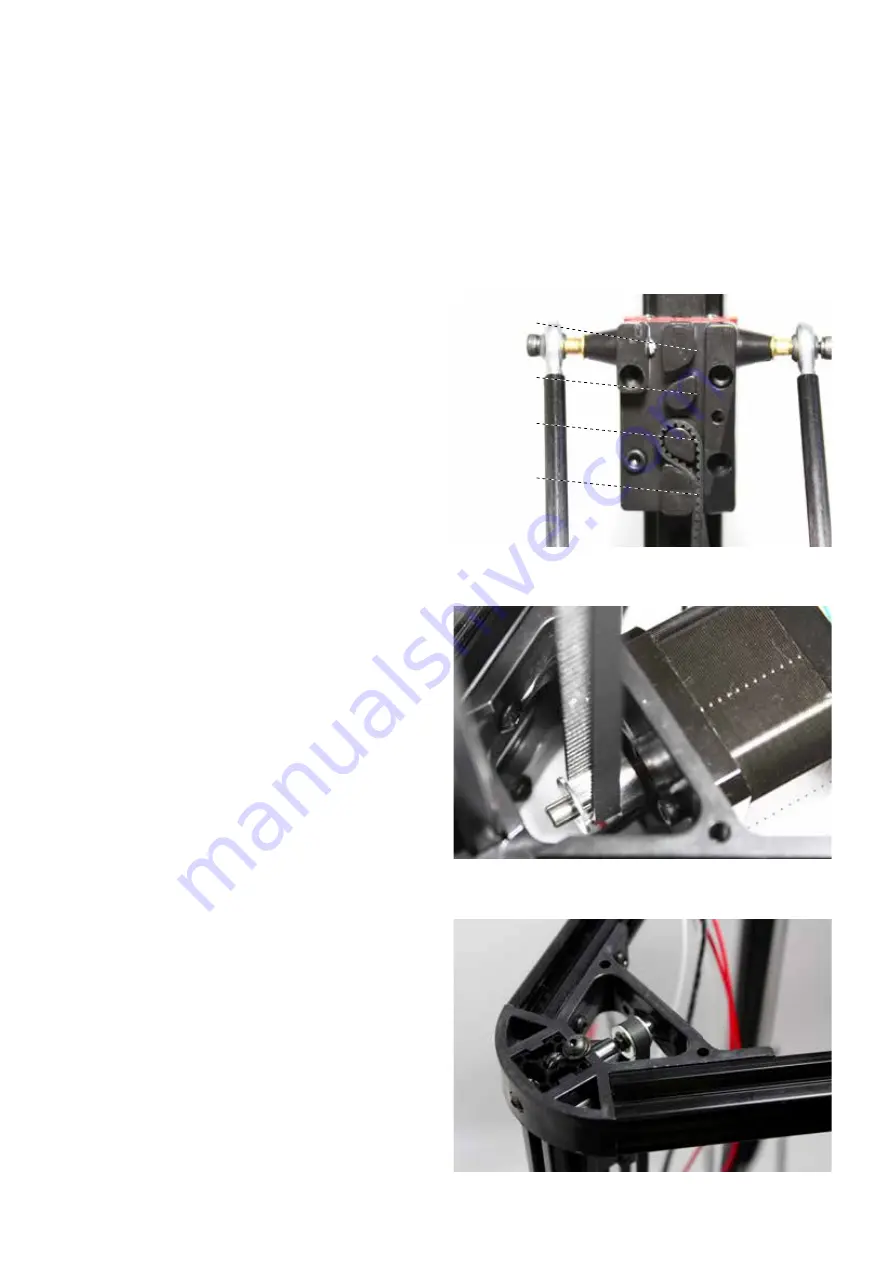
28
ASSEMBLY OF THE BELT
Materials needed for assembly
450cm Belt (1)
Step 1
Divide the belt into 3 equal parts (Approxi
-
mately 150 cm each)
Make a loop at one end of the belt
Loop it around the third chamber on the
belt tensioner as seen in Figure 7.1.
Next loop the other end around the timing
wheel (which is connected to the stepper
motor) (figure 7.2), and guide the belt up
through the other side of the belt tensioner
and around the 608 bearing of the top ver
-
tex (figure 7.3).
Ensure that the belt is routed from the in
-
side the carbon fiber rods.
Figure 7.1
Figure 7.2
Figure 7.3
Chamber 1
Chamber 2
Chamber 3
Chamber 4
Содержание Kinematics
Страница 1: ...KINEMATICS 3D PRINTER MANUAL ...
Страница 2: ......
Страница 3: ...3 ...
Страница 6: ...6 REFERENCE PAGE FOR PARTS ...