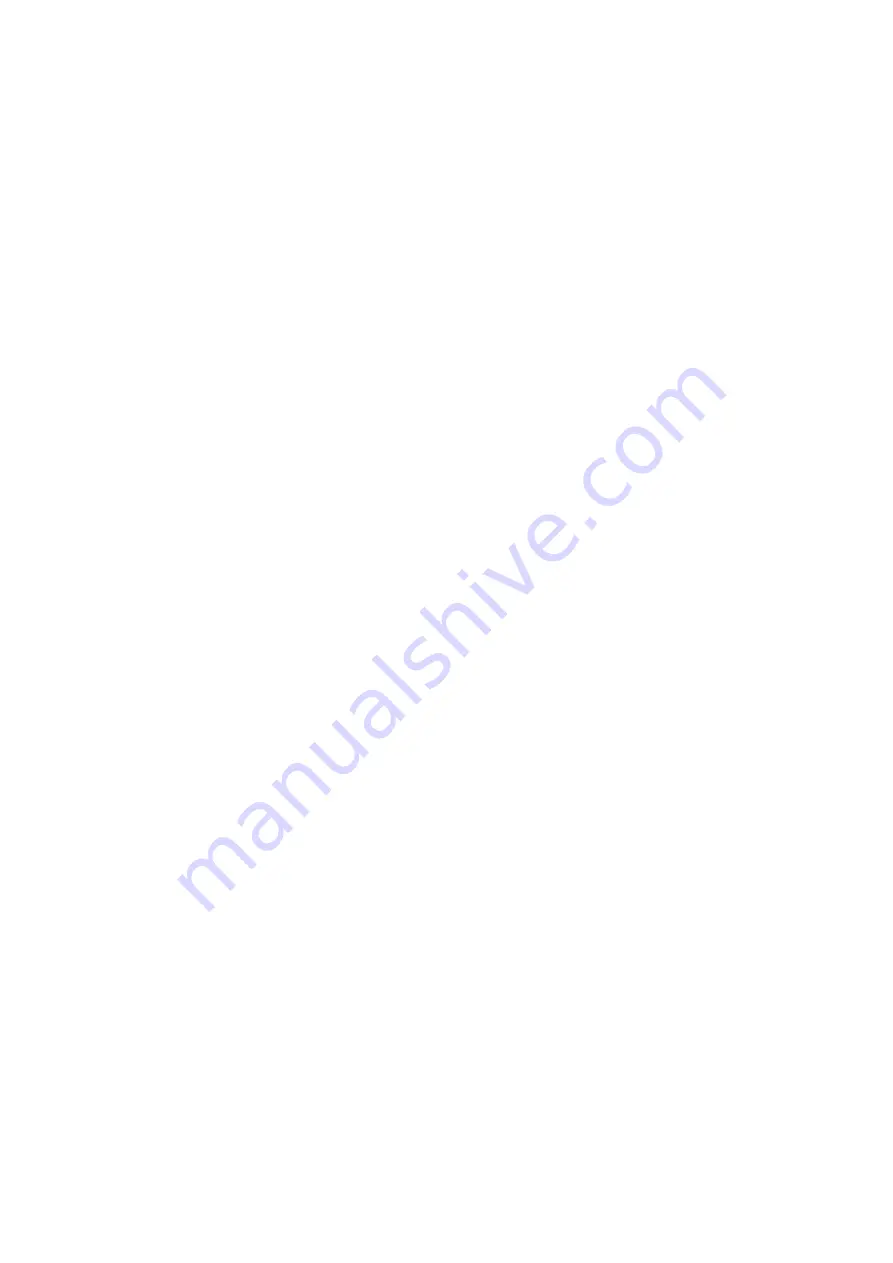
23
2016-09 · Doppelsitz-Bodenventil T_R / T_RL / T_R / Mixproof Bottom Valve T_R / T_RL / T_RC
Aus diesen Faktoren können verschiedene Kombinatio-
nen gebildet werden, die ein optimales Reinigungser-
gebnis wahrscheinlich machen.
Reinigung des Leckageraums
Die Reinigung des Leckageraums erfolgt über eine
Sprühdüse im Doppelteller, die an eine Ventilsitzreini-
gungsleitung angeschlossen wird.
Auch hier können nur allgemeine Empfehlungen gege-
ben werden über die Anzahl und Dauer der Sprühreini-
gungen denn je nach den vor Ort herrschenden Bedin-
gungen wie Art des Produkts, Temperaturen, Reini-
gungsmedien, Reinigungsintervallen usw. können län-
gere oder häufigere Sprüh-Reinigungen erforderlich
sein.
Es wird empfohlen, die Reinigungsbedingungen in der
Anlage in einer Testphase festzulegen, um Reinigungs-
medium einzusparen. Zur Optimierung der Sitzreini-
gung wird dabei durch gelegentliche Kontrollen der
Ventile nach der Reinigung festgestellt, ob die Ventilsit-
ze sauber sind.
Ventile mit Liftreinigung ohne Sprühreini-
gung
Der Leckageraum wird durch Anlüften des oberen oder
unteren Ventiltellers während der jeweiligen Rohrlei-
tungsreinigung gereinigt. Dabei dringt Reinigungsflüs-
sigkeit an den Dichtungen vorbei durch einen metalli-
schen Drosselspalt in den Leckageraum und reinigt
dabei die Dichtungsoberflächen des gelifteten Ventiltel-
lers sowie den Leckageraum.
Diese Art der Leckageraumreinigung wird bei sensiblen
Medien angewendet, bei denen auch die Dichtungsober-
flächen mit gereinigt werden sollten, um eventuell
anhaftende Mikroorganismen abzuspülen. Ebenso zu
empfehlen ist diese Art der Reinigung bei anhaftenden
und auskristallisierenden Medien.
Ventile mit Liftreinigung mit zusätzlicher
Sprühreinigung
Zusätzlich zu der Liftreinigung kann über eine Sprüh-
düse unabhängig von der Rohrreinigung, d.h. auch
während der Produktion, der Leckageraum gereinigt
werden.
Diese Reinigungsart ist bei Doppelsitzventilen zu emp-
fehlen die im Bereich kritischer Medien eingesetzt wer-
den, die stark anhaften, leicht auskristallisieren, klebrig
(z.B. Zuckerlösungen) oder viskos (z.B. Joghurt) sind.
Durch Zwischenspülungen über die Sprühreinigung
kann vermieden werden, dass diese schwer ablaufenden
Produkte über Hitzeübertragung am Leckageraum
anbrennen bevor die nächste Möglichkeit besteht, eine
Ventilteller-Anlüftung auszuführen.
These factors can be combined in such a way as to make
an optimal cleaning result probable.
Cleaning of the leakage outlet system
The leakage chamber is cleaned via a spray nozzle in the
double disk, which is connected to a valve seat cleaning
pipe.
Here, only general recommendations can be made about
the number and duration of spray cleaning. Because
depending on the prevailing conditions such as type of
product, temperatures, cleaning agents, cleaning inter-
vals, etc., longer or more frequent cleanings may be
required.
It is recommended to set the cleaning conditions in the
system in a test phase to save cleaning medium. To opti-
mize the seat cleaning is thereby determined by occa-
sional checks valves after cleaning, if the valve seats are
clean.
Valves with lift cleaning without spray
cleaning
The leakage outlet is cleaned by ventilating the upper or
lower valve discs when the particular pipe is cleaned.
During this process, cleaning fluid flows past the seals
via a metal throttle gap in the leakage outlet and cleans
the seal surfaces of the lifted valve disc and the leakage
outlet.
This kind of leakage outlet cleaning process is used for
sensitive media, in which the seal surfaces also need to
be cleaned in order to flush away microorganisms that
may have adhered to them. This kind of cleaning is also
recommended for media that adheres and crystallises.
Valves with lift cleaning with spray
cleaning
In addition to lift cleaning the leakage outlet can also be
cleaned via a spray nozzle, independently of the pipe
cleaning process, i.e. also during production.
This type of cleaning is recommended for double-seat
valves used in the area of critical media, which adhere
strongly, crystallise easily, and are sticky (e.g. sugar
solutions) or are viscous (e.g. yoghurt). With an interme-
diate cleaning process via spray cleaning, products
which do not flow off easily can be prevented from bur-
ning onto the leakage outlet via heat transfer before the
next opportunity arises to ventilate the valve disc.