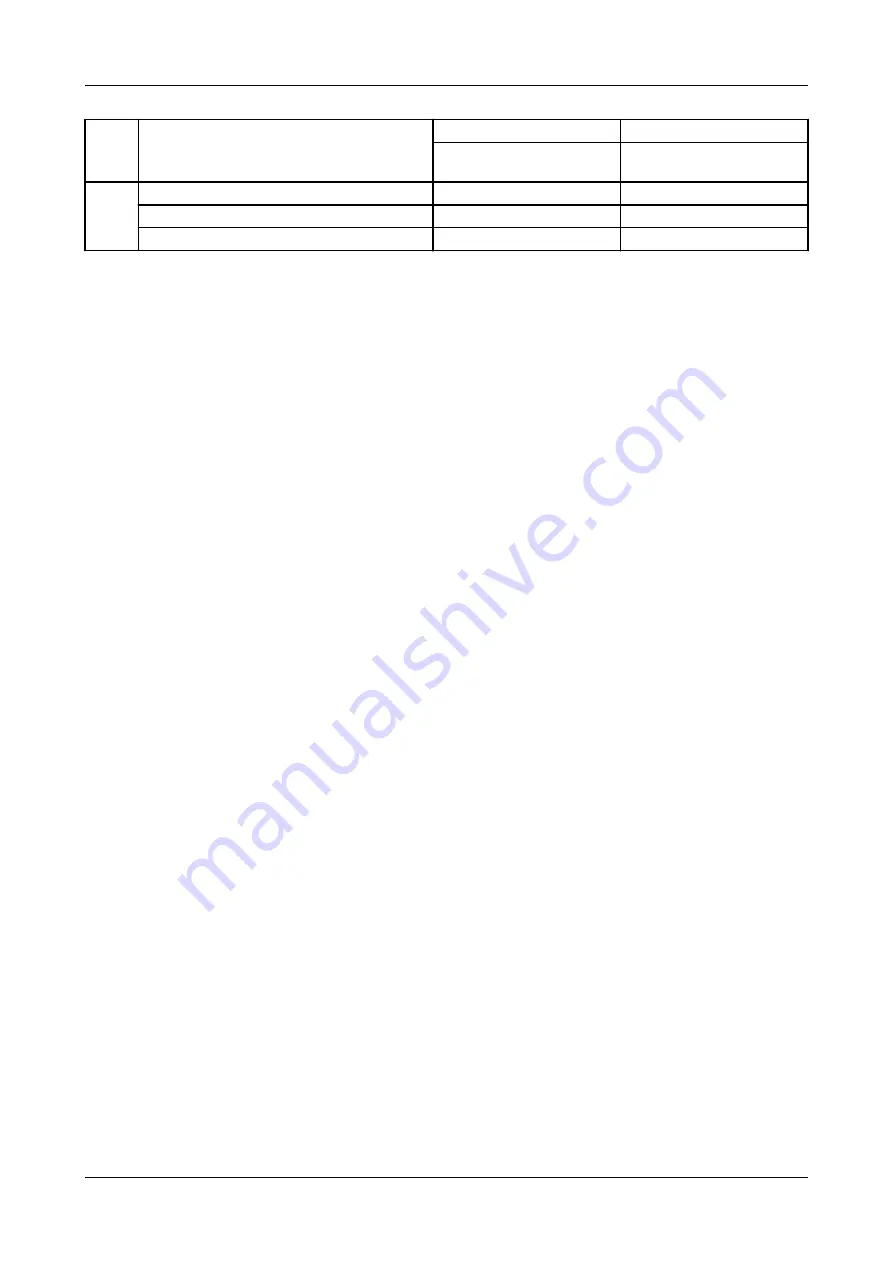
Item
Designation
Nominal width
Nominal width
DN 25 - DN 65
2" OD - 2.5" OD
DN 100 / DN 80
3” OD / 4” OD
X
Square
12 mm
14 mm
Manual actuator
224-001055
224-001056
Proximity switch holder
224-001058
224-001058
Dimension sheet - Manual operation hygienic leakage butterfly valve
430BAL010337EN_7
58
29.07.2021