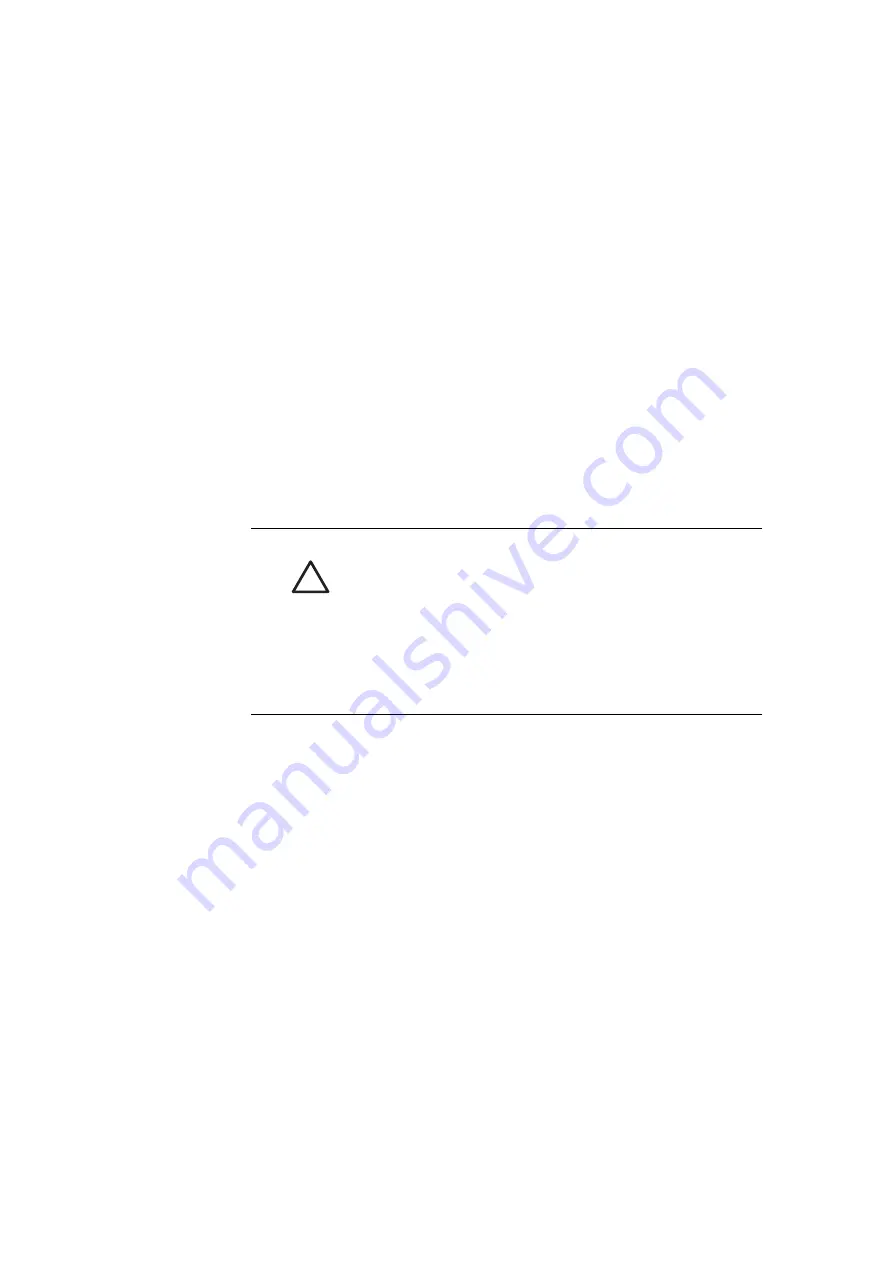
Product description
12
BA.10A.CNY.001.01.10.GB
3.2.1 Areas of application
Standard design
Pumps of the standard design are used for:
•
industrial application
•
CIP processes
•
all systems and processes involved in the food product,
dairy, and beverage industries
Hygienic Design
Because of the consistent hygienic design and the use of ma-
terials which are free of both pores and inclusions, the pump
is highly suitable for use in:
•
pharmaceutical Industry
•
medical technology
•
processes in bioengineering
Special areas of application can be found in the delivery of ul-
tra pure water and water for injection and in systems for the
production of FDA-approved parental and infusion solutions.
3.3 Proper usage
W A R N I N G
!
Improper usage is dangerous.
Operating the pump in a manner that differs from the informa-
tion provided in the order may result in death, severe bodily
injury, or damage to property.
•
Pump only media that are specified in the order. The
pump has been specially designed for that purpose!
•
Operate the pump only in the electrical network specified
in the order!
3.3.1 Pumped liquids
Only pure or slightly contaminated liquids with a maximum
particle size of 0.4 mm may be pumped. These liquids may
not chemically or mechanically attack the pump materials or
lower their strength. If liquids with a viscosity greater than that
of water are to be pumped, make sure that the motor will not
be overloaded. The pump may not be operated beyond the
maximum allowable values. Even short periods of pressure
overload (e.g., as a result of a pressure surge) should be
avoided.
3.3.2 Minimum flow rate
Do not operate the pump below minimum flow rate of
Q
min
= 10 - 15 % Q
opt
.
3.3.3 Connections and pipelines
The nominal diameters of the system pipelines should be
equal to or greater than the nominal diameters of the pump,
i.e., DNE (suction side) and DNA (pressure side), and the
connecting elements to the pump must conform exactly to the
design standard/specification of the mating connector piece
installed on the pump. The suction line must be absolutely
leak-tight and laid in such a way that no air pockets can form.
Avoid tight elbows and do not install valves immediately up-
stream of the pump. The suction head of the system may not
be greater than the suction head guaranteed by the pump.
3.3.4 Motor activation
Do not start and stop the motor more than 15 times per hour.